photoelectric sensor emitter and receiver
- time:2025-07-24 03:03:44
- Click:0
Photoelectric Sensor Emitters and Receivers: The Invisible Eyes of Automation
Look around any modern factory, warehouse, or even your local supermarket checkout. Unseen beams of light are constantly at work, detecting objects, counting products, ensuring safety, and enabling precision. This ubiquitous, often invisible technology relies on a fundamental duo: the photoelectric sensor emitter and its counterpart, the *receiver*. Understanding this pair is key to appreciating how countless automated processes function seamlessly every day.
At its heart, a photoelectric sensor is a device that uses light to detect the presence, absence, or distance of an object without physical contact. This non-contact detection is its superpower, enabling high-speed operation, reliability, and minimal wear and tear. The magic, however, hinges on the specific roles played by the photoelectric sensor emitter and the photoelectric sensor receiver.
- The Emitter (The Light Source): This is the “transmitter” of the sensor pair. Its sole purpose is to generate a focused beam of light, typically infrared (IR), though visible red light, laser, and sometimes even modulated visible light beams are used for specific applications. Common emitter technologies include:
- Light-Emitting Diodes (LEDs): The most prevalent type due to their reliability, long lifespan, energy efficiency, and cost-effectiveness. IR LEDs are particularly common.
- Laser Diodes: Used when a highly collimated (tightly focused), long-range, or extremely precise beam is required.
- The Receiver (The Light Detector): Positioned strategically relative to the emitter, the receiver acts as the “listener.” Its job is to detect the light beam sent out by the emitter. It contains a photosensitive element that converts incoming photons (light particles) into an electrical signal. Common receiver technologies include:
- Phototransistors: Amplify the light signal, making them sensitive and popular for general-purpose detection.
- Photodiodes: Offer very fast response times, crucial for high-speed applications.
The Core Principle: Light Modulation and Interruption
The fundamental operation of a photoelectric sensor relies on the interaction between the emitter’s light beam and the receiver:
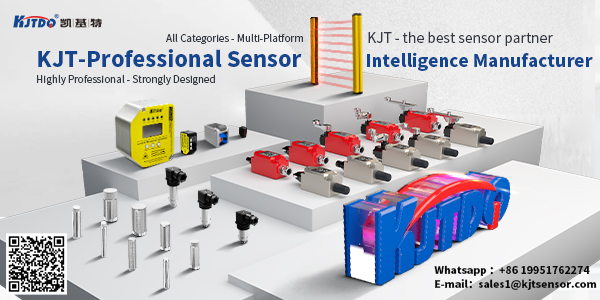
- Transmission: The emitter continuously sends out its light beam.
- Reception: Under normal conditions (no object present), this beam travels to the receiver.
- Signal Generation: The receiver detects the beam and generates a corresponding electrical output signal (e.g., a “high” state).
- Interruption: When an object enters the path of the beam, it blocks or significantly reduces the amount of light reaching the receiver.
- Signal Change: The receiver detects this drop in light intensity and changes its output signal accordingly (e.g., switches to a “low” state).
This change in the receiver’s output signal is what the connected control system (like a PLC or robot controller) recognizes as an object detection event. It triggers actions like stopping a conveyor belt, incrementing a counter, or activating a sorting mechanism.
How the Emitter and Receiver are Arranged: Sensor Types
The physical arrangement of the photoelectric sensor emitter and receiver defines the three main types of photoelectric sensors, each suited for different challenges:
- Through-Beam (Opposed Mode - Separate Emitter & Receiver):
- How it Works: The emitter and receiver are separate physical units, mounted directly opposite each other. The emitter sends a beam directly to the receiver.
- Detection: Detection occurs only when the beam is completely broken by an opaque object.
- Key Advantages: Longest sensing ranges, highest reliability, and most immune to ambient light or object surface conditions (color, reflectivity, texture). Very robust for demanding environments.
- Considerations: Requires mounting on two sides of the detection point, which can be challenging. Alignment is critical.
- Retroreflective (Reflector Mode - Combined or Separate Unit):
- How it Works: The emitter and receiver are housed in the same unit. A special reflector (like a corner-cube or tape) is mounted opposite the sensor unit. The emitter sends a beam to the reflector, which bounces it directly back to the receiver within the same housing.
- Detection: Detection occurs when an object interrupts the beam traveling to or from the reflector.
- Key Advantages: Simplifies wiring and mounting (only one side needed). Sensing range longer than diffuse types. Generally more reliable than diffuse against challenging surfaces. Reflectors are often designed to work only with the specific wavelength of the sensor, aiding ambient light rejection.
- Considerations: Requires a reflector. Shiny objects passing between sensor and reflector can sometimes reflect enough light themselves to prevent detection (“shiny object problem” – sensors often have polarization filters to mitigate this). Range is typically less than through-beam.
- Diffuse (Proximity Mode - Combined Unit):
- How it Works: The emitter and receiver are housed together in one unit. The emitter sends out a light beam. The target object itself acts as the reflector, diffusing some light back towards the receiver in the same unit.
- Detection: Detection occurs when the receiver detects enough light reflected back from the object.
- Key Advantages: Easiest mounting (only one unit on one side). Detects objects regardless of what’s behind them (no reflector needed). Cost-effective.
- Considerations: Sensing range is the shortest. Detection is highly dependent on the object’s size, color, texture, and reflectivity. Light-colored, matte objects reflect well; dark, shiny, or black objects are hardest to detect. Background suppression variants help but add complexity. Susceptible to ambient light interference if not properly designed.
Where They Shine: Applications
The reliability and versatility of the emitter/receiver pair make photoelectric sensors indispensable across industries:
- Manufacturing: Detecting parts on conveyors, robot guidance, fill level control, packaging verification, machine guarding (safety curtains), bottle counting, end-of-travel detection. Through-beam excels on fast lines; diffuse handles presence detection on machines.
- Material Handling & Logistics: Pallet detection, box counting on high-speed sorters, object presence on AGVs (Automated Guided Vehicles), warehouse door safety beams. Retroreflective is common for safety light curtains; through-beam handles high-speed counting.
- Automotive: Assembly line monitoring, component placement verification, paint booth safety, robotic welding cell presence detection.
- Food & Beverage: Bottle/cap presence on filling lines, label detection, case packing verification. Washdown sensors are designed for cleaning.
- Printing & Paper: Web break detection, sheet counting, registration mark sensing. Through-beam often used for breaks.
- Building Automation: Automatic doors (safety and activation), people counting, elevator leveling. Diffuse and retroreflective are common here.
Why Choose Photoelectric Sensors? The Emitter/Receiver Advantage
The core technology offers compelling benefits driven by this light-based detection principle:
- Non-contact Sensing: No physical wear, ideal for delicate objects or high-speed applications. The emitter and receiver never touch the target.
- Long Sensing Range: Especially through-beam and retroreflective sensors can detect objects several meters away.
- Fast Response Time: The emission and detection of light happens nearly instantaneously (microseconds), enabling detection on very high-speed lines.
- Versatility: Available in various sizes, mounting options