sensor photo electric
- time:2025-07-24 04:51:06
- Click:0
Photoelectric Sensors: Your Gateway to Precision Industrial Automation
Imagine a production line where components glide flawlessly into position, quality checks happen in the blink of an eye, and safety systems react faster than human reflexes. This isn’t science fiction; it’s the everyday reality powered by a fundamental industrial workhorse: the photoelectric sensor. Often simply referred to as a “photo eye” or “photo sensor,” this ingenious device leverages light to detect the presence, absence, distance, color, or surface properties of objects with remarkable speed and accuracy. Understanding photoelectric sensor technology is key to unlocking smarter, safer, and more efficient automation solutions across countless industries.
The Core Principle: Light as a Messenger
At the heart of every photoelectric sensor lies a simple yet powerful concept: light interaction. Essentially, these devices consist of two key components:
- An Emitter: This is a light source, typically a Light Emitting Diode (LED), that generates a beam of light. Common types include visible red, infrared (IR), or laser LEDs, chosen for their specific properties like range, visibility to humans, or precision.
- A Receiver: This component detects the emitted light. It can be a photodiode, phototransistor, or similar light-sensitive element.
Detection happens by monitoring how the emitted light beam interacts with the target object. The sensor’s electronics analyze the condition of the received light signal (its presence, absence, or intensity) and trigger an output signal accordingly (usually a simple ON/OFF electrical switch). This reliability and non-contact nature make photoelectric sensors vastly superior to mechanical switches in demanding industrial environments, eliminating wear and tear issues.
Unlocking Potential: Key Sensing Modes
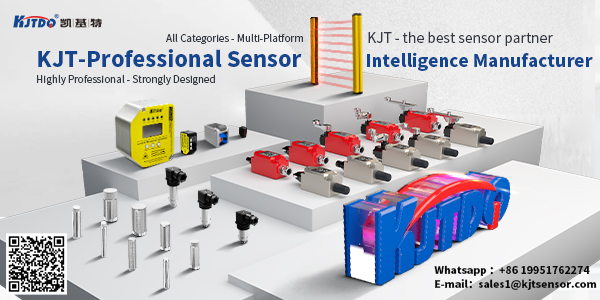
Photoelectric sensors implement this core principle through different configurations, known as sensing modes, each tailored for specific challenges:
- Through-Beam (Opposed Mode): The most reliable and longest-range configuration. The emitter and receiver are housed in separate units, facing each other. Detection occurs when the target object interrupts the direct light beam between them. Ideal for detecting small objects or over large distances.
- Retroreflective: Both emitter and receiver are housed in a single unit. The sensor uses a specialized reflector (corner-cube retroreflector) placed opposite it. The emitter’s light beam travels to the reflector and bounces directly back to the receiver. Detection occurs when the target object breaks this reflected beam. Offers easier alignment than through-beam but requires a reflector.
- Diffuse-Reflective (Proximity Mode): The emitter and receiver are in a single unit. The emitter sends light out, and the receiver detects the light reflected diffusely off the target object itself. Detection occurs when enough reflected light intensity is received. Simplest to install (no separate reflector required) but sensitive to target color, reflectivity, and surface finish. Range is generally shorter than opposed or retro modes. Advanced versions use background suppression (BGS) or foreground suppression (FGS) to enhance reliability by focusing sensing within a precise distance window, minimizing interference from the background or objects beyond the target.
- Convergent Beam (Fixed-Focus): A specialized diffuse mode where the emitter and receiver lenses are precisely focused at a fixed, relatively short distance. Only objects exactly at this focal point reflect enough light back effectively. Excellent for precise positioning or detecting objects on a conveyor at a specific height.
- Color Mark / Color Contrast: These sensors detect differences in color or contrast (e.g., a label on a bottle). They analyze the specific wavelength or intensity of the reflected light, rather than just its presence or absence.
Why Photoelectric Sensors Dominate Industrial Sensing (Key Advantages)
The ubiquity of photoelectric sensors in factories, warehouses, and processing plants isn’t accidental. They offer a compelling combination of benefits:
- Non-Contact Detection: Eliminates physical wear, damage to targets, and maintenance issues associated with mechanical switches. Crucial for delicate objects or high-speed applications.
- High Speed and Response Time: Detect objects moving at incredible speeds, often measured in milliseconds, making them indispensable for modern high-throughput production lines.
- Long Sensing Ranges: Depending on the mode (particularly through-beam), they can detect objects over distances ranging from millimeters to tens of meters.
- Versatility: Available in a vast array of form factors, housing materials (stainless steel, plastic), output types (PNP/NPN, relay, analog), and light sources to tackle virtually any detection challenge – presence, absence, counting, positioning, level control, edge guidance, color recognition.
- Reliability in Harsh Environments: Modern designs offer robust protection against dust, dirt, moisture (IP67/IP69K ratings), vibration, and even specific lighting conditions (resistance to ambient light interference).
- Precision: Laser sensors and convergent beam sensors provide exceptional accuracy for positioning tasks and detecting very small objects or features.
Real-World Applications: Where Photoelectric Sensors Shine
The applications are virtually limitless, but here are some common examples demonstrating their critical role:
- Object Detection on Conveyors: Counting bottles, detecting missing caps, verifying package presence. (Diffuse-reflective, through-beam).
- Precision Positioning: Ensuring robotic arms pick components correctly, verifying parts are inserted fully into fixtures. (Convergent beam, laser).
- Level Control: Monitoring fill levels in bins, tanks, or bottles without contact. (Through-beam, diffuse-reflective with background suppression).
- Packaging Machinery: Detecting film breaks, verifying label placement, counting items going into cartons. (Through-beam, color mark, diffuse-reflective).
- Material Handling: Detecting pallet presence at loading docks, guiding AGVs (Automated Guided Vehicles), confirming stack height. (Retroreflective, diffuse-reflective).
- Printing and Paper Processing: Web break detection, edge guiding for paper rolls, verifying registration marks. (Through-beam, color contrast).
- Safety Systems: Creating light curtains or safety barriers to protect personnel in hazardous machinery zones (a specialized application of the through-beam principle).
Choosing the Right Photoelectric Sensor: Key Considerations
Selecting the optimal sensor requires careful assessment of the application’s demands:
- Sensing Distance: How far away is the target?
- Target Characteristics: What is its size, shape, color, material, surface texture (shiny/matte)?
- Required Precision: How critical is the exact position or distance? (Laser/BGS/FGS excel here).
- Environmental Conditions: Dust, dirt, moisture, temperature extremes, vibration, ambient light levels? (IP rating and ambient light immunity are critical).
- Mounting Constraints: Space limitations? Can a reflector be used? Is a separate emitter/receiver feasible?
- Output Requirements: What type of signal does the control system need (digital ON/OFF, analog distance)?
Leveraging the Power of Light for Industrial Excellence
From the basic presence detection of a box to the sophisticated color verification of a pharmaceutical label, the photoelectric sensor stands as a cornerstone of industrial automation. Its elegance lies in harnessing the fundamental properties of light – speed, precision, and non-contact interaction – to provide reliable, efficient, and versatile sensing solutions. Understanding the different operating modes and their strengths allows engineers and technicians to deploy these sensors effectively, solving complex detection challenges. As technology advances, developments in areas like fiber optic sensing extensions, enhanced background suppression algorithms, and IO-Link communication for diagnostics continue to push the boundaries of what these essential components can achieve. In the