photoeye sensor
- time:2025-07-24 05:01:19
- Click:0
The Invisible Sentinels: Unlocking the Power of Photoeye Sensors in Automation
In the intricate world of modern automation, where precision and efficiency reign supreme, countless unseen heroes work tirelessly. Among them, photoeye sensors operate silently but indispensably. Often the first line of interaction between machines and their environment, these sophisticated photoelectric sensors detect the presence, absence, or position of objects with remarkable reliability. Understanding how they function and where they excel is crucial for engineers, technicians, and anyone navigating automated systems. This isn’t just about technology; it’s about enabling smarter, safer, and faster operations across countless industries.
Demystifying the Photoeye: Seeing with Light
At its core, a photoeye sensor is a device that uses a beam of light – typically visible red, infrared, or laser – to detect objects. It operates on a simple yet elegant fundamental principle: interruption. The sensor comprises two main components (though sometimes integrated into a single housing):
- Emitter: Generates the light beam.
- Receiver: Detects the light beam.
The magic happens when an object interrupts the path of this beam, changing the state detected by the receiver. This change triggers an electrical signal output, communicating crucial information to the machine’s control system – “something is here,” or “the path is clear.” The elegance lies in their non-contact detection. Unlike mechanical switches, photoeye sensors don’t need physical touch, eliminating wear and tear and enabling detection of fragile, fast-moving, or oddly shaped objects.
The Spectrum of Sensing: Key Photoeye Technologies
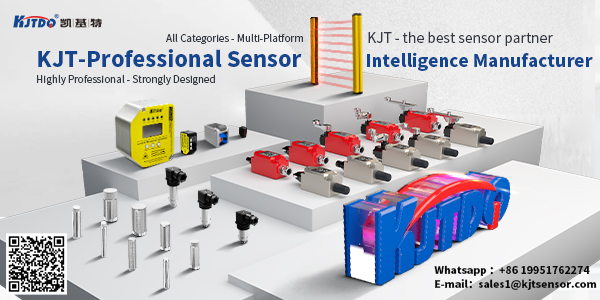
Not all photoeyes are created equal. Three primary operating modes dominate the landscape, chosen based on application requirements like sensing distance, environmental conditions, and target object characteristics:
- Through-Beam (Opposed Mode): This configuration features separate emitter and receiver units, positioned directly opposite each other. The emitter sends a beam continuously to the receiver. Detection occurs when an object breaks this beam. Through-beam sensors offer the longest sensing ranges and highest immunity to environmental factors like target color, transparency, or surface finish. They are ideal for high-precision, long-range applications and detecting tiny objects. Think of verifying bottles on a high-speed filling line or ensuring pallets are correctly positioned on a conveyor.
- Retroreflective (Reflex Mode): Here, the emitter and receiver are housed within a single unit. They rely on a reflector mounted opposite the sensor. The emitted light beam travels to the reflector and bounces back to the receiver within the sensor unit. An object is detected when it blocks the return beam. Retroreflective sensors offer simpler installation (only wiring one device) but have a shorter range than through-beam. They can be affected by highly reflective targets or dirty reflectors. Common uses include detecting vehicles at gates, monitoring production lines for large objects, or presence detection on conveyor belts.
- Diffuse (Proximity Mode): Also featuring an integrated emitter and receiver, diffuse sensors detect objects by relying on the diffuse reflection of the emitted light off the target object itself. The receiver detects this reflected light. Detection occurs when sufficient light bounces back. Diffuse sensors are the easiest to install as they only require mounting on one side. However, their effective range is shortest and performance is highly sensitive to the target’s color (darker objects reflect less light), surface texture, and background conditions. They excel in close-range presence detection, counting opaque objects on a conveyor, or verifying the position of parts.
Why Photoeyes Dominate Industrial Automation
The widespread adoption of photoeye sensors across manufacturing, packaging, material handling, and beyond is no accident. Their advantages are compelling:
- Speed & Responsiveness: They detect objects extremely fast, making them ideal for high-speed production lines where milliseconds matter.
- Non-Contact Sensing: Eliminates mechanical wear, reduces maintenance, and allows detection of objects without physical interaction.
- Versatility: Capable of detecting a vast array of objects – metal, plastic, wood, glass, liquid levels (with appropriate accessories), and even transparent films (using specialized sensors).
- Reliability & Precision: Modern photoelectric sensors offer exceptional accuracy and repeatability, crucial for quality control and process consistency.
- Long Sensing Ranges: Particularly through-beam models can detect objects several meters away.
- Cost-Effectiveness: Reliable detection capability at a relatively low cost per point compared to complex mechanical or other sensing solutions.
Photoeyes in Action: Real-World Applications
The applications for photoeye sensors are virtually limitless within automation. Here are just a few critical examples:
- Conveyor Systems: Detecting product presence to control sorting gates, counting objects, verifying stack height, preventing jams (by detecting blockages), and indicating end-of-line.
- Packaging Machinery: Ensuring cartons are present before filling, verifying labels are applied, checking cap placement on bottles, and detecting film/web breaks.
- Material Handling: Positioning verification of pallets on AGVs (Automated Guided Vehicles), detecting vehicles at loading docks or gates, and safeguarding robotic workcells by monitoring entry points.
- Assembly Lines: Confirming part presence before a robotic operation, checking orientation of components, and verifying assembly completion before moving to the next stage.
- Printing & Converting: Register mark detection for precise printing alignment, web guiding to keep materials centered, and detecting splices or tears.
- Safety Systems: Used as part of safety light curtains or area guarding solutions to detect personnel entering hazardous zones, triggering machine shutdown.
Choosing and Optimizing Your Photoeye Solution
Selecting the right photoeye sensor requires careful consideration:
- Operating Mode: Through-beam, Retroreflective, or Diffuse? Determine the best fit based on range, target, and installation constraints.
- Sensing Range: How far away does the sensor need to detect?
- Target Characteristics: Size, color, material (opaque, transparent, translucent), surface finish (shiny, matte)?
- Environment: Dusty, humid, wet, extremes of temperature, potential for background interference? Look for appropriate IP (Ingress Protection) ratings.
- Output Type: Standard NPN/PNP discrete, analog, or IO-Link for advanced diagnostics and parameterization?
- Response Time: How quickly must the sensor react?
Proper installation is crucial. Ensure the light beam is correctly aligned (especially for through-beam and retroreflective). Keep lenses clean. Consider potential background interference for diffuse sensors and shield them if necessary. Protect sensors physically in harsh environments.
The Future is Bright: Evolving Photoeye Capabilities
Photoelectric sensor technology continues to evolve. Smart sensors with IO-Link communication deliver valuable diagnostic data (e.g., signal strength, temperature, contamination warnings) directly to control systems, enabling predictive maintenance. Enhanced optics and algorithms improve reliability for difficult-to-detect targets like clear glass or shiny metal. Laser-based photoeye sensors offer even finer precision and longer ranges for specialized applications. The core function remains elegantly simple, but the intelligence and connectivity surrounding it are pushing boundaries, solid