photoelectric sensor range
- time:2025-07-24 03:08:51
- Click:0
Understanding Photoelectric Sensor Range: From Millimetres to Metres
Imagine a critical assembly line grinding to a halt. Why? A box wasn’t detected at a conveyor transfer point. The culprit? A photoelectric sensor operating beyond its effective range. The photoelectric sensor range, often called the sensing distance or operating range, isn’t just a number on a datasheet; it’s the fundamental boundary determining where and how reliably a sensor can detect an object. Choosing the right sensor with the appropriate range is paramount for efficiency, accuracy, and preventing costly downtime in automation systems. This article delves deep into the factors influencing photoelectric sensor range, exploring the capabilities of different sensor types and key considerations for optimal selection.
Why Range Matters: The Core of Detection Reliability
A photoelectric sensor’s range defines the physical distance over which it can consistently and accurately detect a specified target. Operating a sensor near or beyond its maximum sensing distance leads to unreliable performance – missed detections (false negatives) or triggering without a target present (false positives). This unreliability cascades into production errors, safety risks, and maintenance headaches. Conversely, selecting a sensor with ample range headroom for the specific application ensures robust, dependable operation even under less-than-ideal conditions, like target variations or minor misalignments. Crucially, range isn’t a standalone spec; it’s intrinsically linked to the sensor’s type and the environment in which it operates.
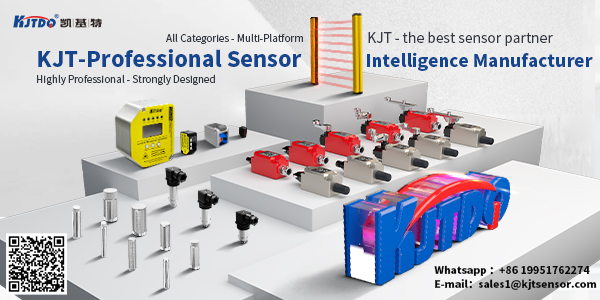
Photoelectric Sensor Types and Their Range Capabilities
The achievable range varies dramatically depending on the photoelectric sensing principle employed:
- Through-Beam Sensors (Emitter/Receiver Pair): These offer the longest possible range for photoelectric sensors, often extending many metres (up to 100m or more with high-power variants). The emitter and receiver are separate units mounted opposite each other. Detection occurs when the target physically interrupts the direct light beam travelling from the emitter to the receiver. This inherent strength stems from the focused beam path and the receiver’s dedicated role of solely looking for its paired emitter’s signal. Max Range Advantage: Ideal for large-scale applications like monitoring long conveyors, warehouse doorways, or detecting vehicles.
- Retroreflective Sensors: These combine the emitter and receiver into a single housing, relying on a reflector (like a prismatic tape) mounted opposite. The sensor detects when the target blocks the light beam travelling to and from the reflector. Their range is significant but generally less than through-beam sensors, typically ranging from around 0.5 metres up to 10-15 metres depending on size and power. Range Consideration: Excellent for applications where wiring both sides is impractical, offering a good balance of range and convenience, though less than through-beam.
- Diffuse Reflective Sensors (Proximity Mode): Emitter and receiver are also housed together, but they detect light reflected directly off the target itself. Consequently, their operating range is significantly shorter than through-beam or retroreflective types, usually measured in centimetres (e.g., 10mm to 1m, with many common models maxing out around 300mm). Range Limitation: The sensing distance is highly dependent on the target’s size, colour, reflectivity, and surface texture. Dark, non-reflective, or small targets drastically reduce the effective range. Suited for close-proximity detection of objects on conveyors or presence sensing.
- Background Suppression (BGS) & Fixed Field (Foreground Suppression - FGS) Sensors: These are sophisticated diffuse sensors. They employ triangulation principles or specialized optics to gauge the distance of the reflected light, ignoring reflections beyond (BGS) or in front of (FGS) a specific set point. Precise Range Control: While their absolute maximum range might still be limited (often similar to standard diffuse, 10mm - 500mm), their key strength is consistent detection within a narrow, defined sensing window, relatively unaffected by background objects or target reflectivity variations. This allows for precise positioning tasks within their shorter operating range.
Key Factors Influencing Effective Sensor Range
Understanding the datasheet’s nominal maximum sensing distance is just the starting point. The real-world effective range is influenced by several critical variables:
- Target Properties: This is especially crucial for diffuse, BGS, and FGS sensors. Size, colour (light vs. dark), material (shiny metal vs. matte plastic), and surface texture (glossy vs. rough) dramatically impact the amount of light reflected back to the receiver. A large, white, matte target will be detectable at a much longer range than a small, black, glossy target using the same diffuse sensor.
- Environmental Conditions: Dust, fog, steam, heavy rain, or intense ambient light (like direct sunlight) can scatter or overpower the sensor’s light beam. This significantly degrades the effective range. Conversely, clean, dry, controlled lighting environments allow sensors to operate closer to their nominal range specifications. Choosing sensors with modulated light (pulsed beams) and appropriate housings (IP ratings) helps mitigate environmental interference.
- Sensor Alignment (Critical for Thru-Beam & Retro): Precise alignment between emitter and receiver (or sensor and reflector) is essential for maximizing range and reliability. Misalignment directly translates to reduced effective range or complete failure to detect.
- Lens Optics and Light Source: The quality and design of the lens focus the emitted light and collect the reflected light. Higher quality optics generally yield better range performance and signal strength. LED type and power output also play a role; higher power LEDs typically offer longer range.
- Sensitivity Settings: Many sensors offer adjustable sensitivity (gain). Increasing sensitivity can extend the perceived range slightly, particularly for diffuse sensors on difficult targets, but often at the cost of increased susceptibility to background reflections or ambient light interference (higher risk of false triggers). Decreasing sensitivity increases resistance to interference but shortens the effective range.
- Power Supply: Operating voltage fluctuations can sometimes affect the intensity of the emitted light, potentially impacting range.
Selecting the Right Sensor Range: A Practical Approach
Choosing the optimal photoelectric sensor isn’t simply about picking the one with the longest listed range. Follow this logic:
- Define the Application: Determine the physical distance between the sensor mounting point and the target’s detection point. Add a safety margin (e.g., 20-50%) to account for potential installation variations, vibration, or tolerance stack-up. This is your required sensing distance.
- Analyze the Target: Size? Material? Colour? Surface? Is it consistent? For diffuse/BGS/FGS sensors, difficult targets will necessitate choosing a sensor where your required distance falls comfortably within the lower half of its specified range for that target type (often detailed in charts within the datasheet).
- Assess the Environment: Clean factory floor or dusty lumber mill? Indoors or outdoors? Bright ambient light? Harsh conditions push you towards through-beam sensors (for range and reliability despite grime) or sensors with high IP ratings and resistance to ambient light.
- Choose the Sensor Type Based on Range & Constraints:
- Need maximum range? Through-beam is king.
- Need moderate range and simpler wiring? Retroreflective is a strong contender.