photoelectric detector
- time:2025-07-25 03:44:36
- Click:0
The Invisible Guardians: How Photoelectric Detectors Power Our Automated World
Photoelectric Detectors: Sensing Light to Shape Modern Automation
Look around you. The automatic doors glide open as you approach the supermarket. That hands-free soap dispenser activates the moment your hand moves near it. The conveyor belt at the factory stops precisely when an object is misaligned. Behind these seemingly mundane actions lies a critical, often unseen technology: the photoelectric detector. These remarkable sensors, fundamental components of optoelectronics, convert light signals into electrical signals, acting as the eyes of countless automated systems. Understanding how they work, their types, and their diverse applications reveals the pervasive influence of this essential technology in shaping efficiency, safety, and convenience in our daily lives and industrial landscapes.
The Core Principle: From Photons to Electrons
At its heart, the operation of a photoelectric sensor hinges on the photoelectric effect, a phenomenon famously explained by Albert Einstein. When light (photons) strikes a photosensitive material within the detector (typically a photodiode, phototransistor, or sometimes a photoresistor), it imparts energy to electrons. If the photon energy exceeds the material’s work function, electrons are liberated, generating an electrical current or changing the material’s electrical resistance. This conversion of light energy into an electrical signal is the fundamental magic. The resulting electrical change is then detected, processed, and used to trigger an action – turning a machine on or off, counting items, detecting presence, or signaling an alarm. The wavelength sensitivity of the detector element is crucial, determining whether it responds best to infrared, visible light, or ultraviolet sources, often paired with an emitter like an LED or laser diode.
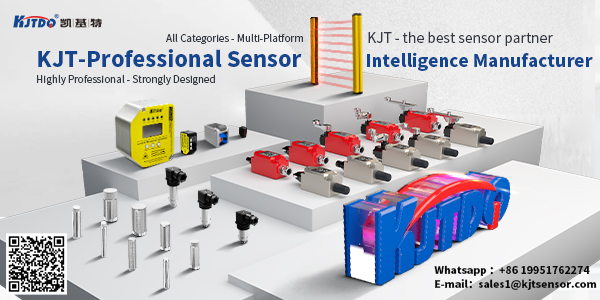
Major Types: Tailoring Light Sensing to the Task
Not all detection scenarios are the same. Photoelectric detectors have evolved into distinct configurations to solve specific challenges:
- Through-Beam Sensors (Opposed Mode): This classic setup features a separate light emitter and photoelectric receiver positioned opposite each other. The emitter sends a constant beam of light (often infrared for reliability) directly to the receiver. An object is detected when it interrupts this beam. Key advantages include long sensing ranges and high reliability, as the receiver gets a strong, uninterrupted signal until blocked. They are ideal for detecting opaque objects over significant distances or in demanding environments like large conveyor systems.
- Retroreflective Sensors: Here, the emitter and receiver are housed in a single unit. A specialized reflector (corner-cube prism or tape) is placed opposite the sensor, bouncing the emitted light beam directly back to the receiver. Detection occurs when an object breaks the path between the sensor and the reflector. This offers simpler installation (only one device to wire and mount) compared to through-beam while still achieving good range and reliability. Transparent or shiny objects can sometimes be challenging if they reflect enough light back to the sensor.
- Diffuse Reflective Sensors (Proximity Mode): The most compact solution, diffuse sensors integrate both emitter and receiver into one housing. They detect an object based on the reflection (diffusion) of the emitted light off the target object itself back to the receiver. Ease of installation is a major benefit here, as no separate reflector or receiver unit is needed. However, sensing range is generally shorter than through-beam or retroreflective types. Performance is also influenced by the object’s color, reflectivity, and surface texture – darker, matte objects reflect less light and are harder to detect at range. Modern background suppression (BGS) and foreground suppression (FGS) variants intelligently focus the detection zone, largely mitigating these limitations for precise positioning.
- Convergent Beam & Fixed-Field Sensors: These specialized diffuse types use lenses to create a sharply focused beam (convergent) or a very narrow, consistent detection zone close to the sensor face (fixed-field). Excellent for detecting small objects or ensuring detection only occurs at a very specific distance, ignoring background reflections – perfect for assembly verification or small part sorting.
Ubiquitous Applications: Where Photoelectric Sensors Shine
The versatility of photoelectric detectors ensures their presence across nearly every sector:
- Industrial Automation: The backbone of modern manufacturing. Used for object detection on conveyors, part counting, fill level control in bottling plants, height verification, web break detection, robot positioning guidance, and packaging integrity checks. Their speed, reliability, and non-contact nature are essential for high-throughput lines.
- Material Handling & Logistics: Guiding automated guided vehicles (AGVs), controlling palletizing/depalletizing robots, triggering sortation gates in warehouses, and detecting packages on chutes. Through-beam sensors often monitor large entry/exit points.
- Building Automation & Security: Enabling touchless faucets, soap dispensers, automatic doors, and elevator call buttons. Used in security systems for intrusion detection (beam interruption), occupancy sensing for lighting control, and smoke detectors (detecting light scattering in smoke chambers).
- Consumer Electronics: Found in printers for paper jam detection and media sensing, smartphones for ambient light sensing (screen brightness control) and proximity sensing (turning off the screen during calls). Photodiodes are the key component in optical mice.
- Transportation: Vehicle detection at traffic lights (inductive loops often supplement them), presence detection in automated car washes, safety curtains on train doors, and obstacle detection on automated guided vehicles.
- Food & Beverage Industry: Critical for container inspection (ensuring bottles or cans are properly filled and capped), label detection, cap presence verification, and detecting product levels in transparent containers. Hygienic designs are crucial here.
- Renewable Energy & Sustainability: Monitoring solar panel orientation, detecting contaminants in water treatment processes, or controlling ventilation based on ambient light.
Choosing the Right Detector: Key Considerations
Selecting the optimal photoelectric sensor isn’t arbitrary. Key factors drive the decision:
- Detection Task: What needs sensing? (Presence, absence, position, count, level, color/mark?) Is it opaque, transparent, shiny, matte? Geometry? Size? This dictates the sensor type (e.g., through-beam for long-range object blockage, diffuse reflective with BGS for precise position on shiny targets).
- Sensing Range: The required operating distance between the sensor and the target. Through-beam offers the longest reliable ranges, while diffuse reflective is more limited.
- Environment: Exposure to dust, dirt, moisture (IP rating), chemicals, temperature extremes, or vibration? Requires ruggedized housings and sealed optics. Ambient light conditions? Sunlight can overwhelm some sensors unless designed for immunity.
- Target Properties: Material, color, reflectivity, surface finish. Transparent objects may necessitate polarized or specialized sensors. Dark objects challenge standard diffuse reflective sensors.
- Output Requirements: Does the control system need a simple digital on/off signal (PNP/NPN transistor output), an analog signal (for distance/grayscale), or a data protocol (IO-Link)? Relay outputs handle higher power loads.
- Response Speed: How fast does the sensor need to detect and signal? Critical for high-speed counting or sorting applications.
Reliability and Maintenance: Ensuring Continuous Operation
While renowned for durability, photoelectric detectors require consideration for sustained performance. Proper alignment is critical, especially for through-beam and retroreflective types; misalignment causes false signals or failure. Keeping the emitter and receiver lenses clean is paramount – dust, dirt, grease, or condensation can scatter or block light beams, leading to malfunctions