industrial photocell sensor
- time:2025-07-28 09:07:50
- Click:0
Industrial Photocell Sensors: The Invisible Workhorses Powering Modern Automation
Imagine bustling factory floors and intricate assembly lines operating with seamless precision – objects counted, positioned, monitored, and controlled at lightning speed, often without human intervention. At the heart of much of this automated magic lies an unsung hero: the industrial photocell sensor. Far more robust and reliable than simple home automation light sensors, these devices form a critical backbone for efficiency, safety, and quality control across countless industries. This article dives deep into the world of industrial photocell sensors, exploring their function, types, applications, and the immense value they bring to modern industrial operations.
Photocell sensors, technically known as photoelectric sensors in the industrial context, operate on a fundamental yet powerful principle: they detect the presence, absence, distance, or characteristics of objects using light. An emitter projects a light beam (typically visible red, infrared, or laser), and a receiver detects changes in this beam – whether it’s broken, reflected back, or its intensity altered. This simple interaction translates into a decisive electrical signal used by control systems like PLCs (Programmable Logic Controllers) to trigger actions instantly.
The Core Mechanisms: How Industrial Photocells “See”
Understanding the primary sensing modes is crucial to appreciating the versatility of industrial photocell sensors:
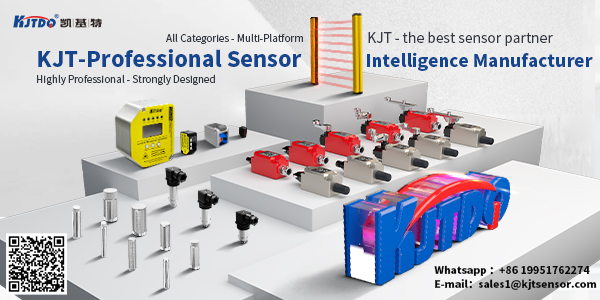
- Through-Beam (Opposed Mode): This configuration offers the longest sensing range and highest reliability. The emitter and receiver are separate units placed directly opposite each other. Detection occurs when an object physically interrupts the direct light beam traveling from emitter to receiver. This method is highly immune to target color, surface finish, or ambient light interference, making it ideal for long-range detection and challenging environments.
- Retro-Reflective (Reflex Mode): Here, a single unit houses both the emitter and receiver. The emitted light beam is directed towards a specialized reflector. When an object passes between the sensor and the reflector, it blocks the beam, preventing the reflected light from reaching the receiver. This setup simplifies installation (only one device and reflector need wiring/mounting) while offering good range and reliability, though it can be susceptible to highly reflective objects potentially mimicking the reflector’s return signal.
- Diffuse-Reflective (Proximity Mode): All components (emitter and receiver) are again in a single housing. This sensor works by detecting light reflected directly off the target object itself. The emitter sends out light; if the target is close enough and within the field of view, some light bounces back to the receiver. Detection is based on the intensity of this returned light. While offering the simplest installation (only one device), detection range is shorter than other modes, and performance is heavily influenced by the target object’s color, reflectivity, and surface texture. Advanced photoelectric sensors often use background suppression techniques within this mode to mitigate the influence of color/reflectivity variations.
Robustness for Demanding Environments
What truly distinguishes an industrial photocell sensor from its simpler counterparts is its construction. These devices are engineered to thrive in environments that would cripple standard sensors:
- Rugged Enclosures: Typically made from durable metals (stainless steel, nickel-plated brass) or high-strength engineering plastics, offering significant resistance to physical impact and vibration common on machinery and production lines.
- IP (Ingress Protection) Ratings: High IP ratings (e.g., IP67, IP68, IP69K) signify exceptional resistance to dust and water ingress. They can withstand washdowns with high-pressure jets, exposure to chemicals, oils, and challenging weather conditions common in food processing, foundries, or outdoor applications.
- Extended Temperature Ranges: Reliable operation is maintained across wide temperature extremes, from sub-zero freezer units to scorching foundry environments.
- Electrical Resilience: Built to handle electrical noise, surge voltages, and reverse polarity protection common in industrial electrical panels and power supplies.
Pervasive Applications: Where Industrial Photocells Shine
The adaptability and reliability of photoelectric sensors make them indispensable across a vast industrial spectrum:
- Automated Production & Assembly Lines: Detecting part presence/absence at key stages, counting products, controlling cycle starts, verifying part orientation, triggering robotic actions, monitoring bin levels, and detecting jams. Through-beam sensors are often the go-to choice for critical position verification.
- Packaging Machinery: Precise label detection, bottle cap presence verification, case counting for filling, detecting film breaks, and controlling carton erectors or sealers. Diffuse-reflective sensors with background suppression excel at detecting labels on different backgrounds.
- Material Handling (Conveyors & Sorting Systems): Object detection on conveyors (starting, stopping, diverting lines), package sizing for routing, pallet position detection, and triggering sortation mechanisms. Retro-reflective sensors are frequently used for object detection on conveyors where mounting opposite sides is impractical.
- Safety Systems: Integrating into machine safety light curtains or presence-sensing devices to create invisible barriers, halting machinery instantly when personnel enter hazardous zones (Safety-rated through-beam sensors are fundamental here).
- Logistics & Warehousing: Detecting vehicles at dock doors, monitoring pallet positions in racks, guiding AGVs (Automated Guided Vehicles), and verifying door/gate positions. Laser-based photoelectric sensors offer very precise positioning.
- Food & Beverage Processing: Counting bottles/cans on high-speed lines, detecting liquid levels in clear containers, verifying cap application, and ensuring products are correctly positioned for filling or capping – all while withstanding harsh washdown cleaning cycles. Stainless steel housings with IP69K ratings are essential.
The Tangible Benefits: Why Industry Relies on Them
The widespread adoption of industrial photocell sensors is driven by concrete advantages:
- Enhanced Efficiency & Productivity: Automating detection tasks eliminates human error and slowdowns, enabling significantly faster production cycles and continuous operation. Real-time detection feeds PLCs for immediate response.
- Improved Quality Control: Consistent detection ensures processes only proceed when components are present and correctly positioned, reducing defects and rework. Sensors can flag missing parts or process deviations instantly.
- Boosted Operational Safety: Integrating with safety systems creates critical protective barriers, preventing accidents around moving machinery and robotic cells. Safety-rated photocells are vital components.
- Reduced Operational Costs: Automation lowers labor requirements, minimizes waste from errors, and prevents costly equipment damage caused by jams or misaligned parts. Precision detection avoids costly mistakes.
- Flexibility & Versatility: With various sensing modes (through-beam, retro-reflective, diffuse with background suppression), light sources (LED, laser), and specialized models (fiber optic attachments, long-range, high-temperature), a solution exists for nearly any detection challenge.
- Reliability & Longevity: Engineered for harsh conditions, industrial sensors offer years of dependable service with minimal downtime, maximizing return on investment.
Selecting the Right Sensor: Key Considerations
Choosing the optimal photoelectric sensor requires careful assessment of the application:
- Sensing Mode: What’s the detection principle needed (object interruption, reflection from target, long range)? Through-beam for max reliability/long range, diffuse for proximity to target.
- Range: How far away is the target?
- Target Characteristics: Size, color, material (