safety photo sensor
- time:2025-07-28 09:33:22
- Click:0
Safety Photo Sensors: The Invisible Shield Protecting Workers and Machinery
Imagine the sudden whirr of a massive hydraulic press descending, the rapid arc of an industrial robot arm, or the relentless motion of a high-speed conveyor belt. Now, imagine the catastrophic consequences if a worker’s hand, clothing, or tool inadvertently entered these danger zones. This is the harsh reality of industrial environments, where achieving peak productivity cannot – and must not – come at the expense of human safety. Enter the often overlooked but critically important guardian: the safety photo sensor. These sophisticated electronic sentinels form an invisible barrier, tirelessly monitoring hazardous areas and triggering immediate machine shutdown to prevent accidents before they occur.
Beyond Basic Sensors: The Dedicated Purpose of Safety Integrity
It’s crucial to distinguish standard industrial photo sensors from their safety-rated counterparts. While both may use light (typically infrared) for detection, safety photo sensors are engineered to an entirely different standard. Their sole mission is functional safety – preventing harm to people and damage to equipment in potentially dangerous situations. This translates into rigorous design and certification requirements governed by international standards like IEC 61496 (types 1 to 4) and ISO 13849-1. Key differentiators include:
- Redundancy & Self-Monitoring: Safety sensors incorporate multiple, independent internal channels. They constantly perform self-checks, scrutinizing component health, LED output intensity, lens cleanliness, alignment stability, and signal reception integrity. If any internal fault is detected (e.g., a failing emitter, blocked lens, or misalignment), the sensor immediately forces its output relays into the safe state (usually “off”), halting the connected machinery. A standard sensor might just give an incorrect signal.
- Fault Exclusion Design: Safety sensors are meticulously designed to make certain types of dangerous failures physically impossible or extremely improbable. This principle, known as fault exclusion, is fundamental to achieving high Safety Integrity Levels (SIL) or Performance Levels (PL).
- Reliable Output Switching: Safety outputs are designed as “positively driven” or “force-guided” relays. These contacts have a mechanical linkage ensuring that if one contact welds shut (a dangerous failure), the opposite contact cannot close, maintaining the safe state. This prevents a single failure from misleadingly signaling “all clear.”
- Certification: Reputable safety photo sensors carry certifications like TÜV or UL, explicitly validating their compliance with relevant functional safety standards for specific PL or SIL ratings. Never assume a standard sensor meets safety requirements.
How They Work: Creating Invisible Safety Barriers
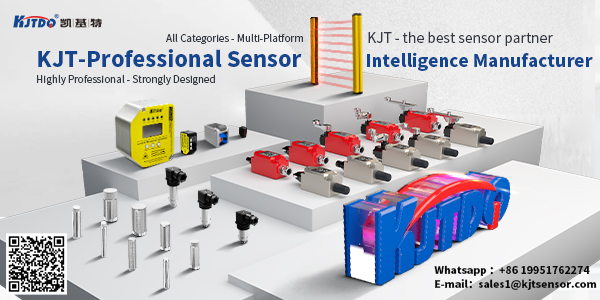
The fundamental principle is elegantly simple but executed with high reliability:
- Emitter: A dedicated safety light emitter projects an infrared beam. This could be a focused beam or a diffuse field, depending on the sensor type.
- Receiver: A corresponding safety receiver detects the presence (or absence) of this beam.
- Monitoring & Logic: The receiver constantly analyzes the beam’s integrity. If the beam is uninterrupted (in access denial applications), the sensor signals “Area Clear” to the machine safety controller or monitored relay. If the beam is intentionally or unintentionally interrupted (e.g., by a hand, body, or object), the sensor signals “Intrusion Detected” within milliseconds.
- Safe Response: The safety controller reacts instantly by cutting power to the machine’s dangerous actuators via safety relays or contactors, initiating an emergency stop. The machinery remains locked out until the hazard is cleared and the system is deliberately reset.
Common Configurations for Diverse Needs
Safety light curtains and light grids are the most prevalent photo-based safety devices, but several configurations exist:
- Safety Light Curtains/Grids: These consist of multiple, closely spaced, parallel infrared beams creating a vertical or horizontal detection screen. Used extensively to safeguard machine perimeters, entry points to robotic cells (robot safeguarding), and access points on presses and automated assembly lines. Interrupting any beam triggers the stop.
- Safety Through-Beam Sensors: Consist of a separate emitter and receiver facing each other. Best for long-range protection (up to tens of meters), perimeter guarding of large machinery, or monitoring entry/exit points to hazardous zones. Requires precise alignment.
- Safety Retro-Reflective Sensors: Emitter and receiver are housed together, using a reflector bounced back. Suitable for shorter ranges where installing a separate receiver is impractical. Often include filters to ignore non-reflector surfaces.
- Safety Diffuse/Proximity Sensors: Emitter and receiver in one housing, detecting reflection from an object close by. Less common for personnel safeguarding due to shorter range and susceptibility to reflective backgrounds, but used for presence detection within pre-secured zones.
The Tangible Benefits: More Than Just Compliance
Integrating safety photo sensors delivers significant advantages:
- Enhanced Personnel Protection: Dramatically reduces the risk of crush, impact, shearing, and amputation injuries by creating reliable, non-contact detection zones. They act as the primary safeguard for point-of-operation hazards.
- Minimized Machine Damage: Preventing collisions between humans and machines also prevents costly damage to equipment, tools, and products.
- Increased Productivity & Uptime: Compared to physical barriers, safety sensors allow for partial access for tasks like feeding materials or inspection without a full safety door opening and lengthy lockout cycle, enabling flexible automation. Intelligent muting functionality allows safe, temporary suspension of the light curtain for pallet passage, further optimizing flow.
- Cost-Effectiveness: While initial investment is higher than standard sensors, the reduction in accidents, downtime, insurance premiums, and regulatory fines offers substantial long-term savings.
- OSHA/ISO Compliance: Essential for meeting stringent workplace safety regulations and achieving machine safety certification for sale and operation.
Where They Are Essential: Key Applications
The versatility of safety photo sensors makes them indispensable across numerous sectors:
- Presses & Stamping: Guarding the point of operation on mechanical and hydraulic presses.
- Robotic Workcells: Creating restricted access zones around industrial robots (robot safeguarding), especially collaborative applications where proximity is necessary.
- Material Handling & Logistics: Safeguarding palletizing/depalletizing stations, conveyor entry/exit points, and automated guided vehicle (AGV) paths.
- Packaging Machinery: Protecting operators during machine feeding, jam clearance points, and wrapping stations.
- Plastic Molding: Guarding injection molding machines, particularly during mold closing.
- Automotive Manufacturing: Line side protections, transfer press safeguarding, and assembly station access control.
- Woodworking & Metalworking: Protection around saws, CNC machines, and milling operations.
Implementing Effectively: Choosing and Integrating
Selecting and installing the right safety photo sensor demands careful consideration:
- Risk Assessment First: Always start with a machine risk assessment (ISO 121