rca photoelectric sensor
- time:2025-07-24 03:59:57
- Click:0
Beyond the Connector: Unveiling the Power of Photoelectric Sensors (Including RCA Considerations)
Picture an automated factory: boxes glide seamlessly down a conveyor, robotic arms pick and place with uncanny precision, and production counts are tracked flawlessly. Hiding in plain sight, orchestrating much of this efficiency, are unsung heroes – photoelectric sensors. While the term “RCA Photoelectric Sensor” might initially evoke thoughts of vintage audio connectors, in the industrial automation lexicon, it often signifies a specific form factor or interface type for reliable optical sensing. Let’s illuminate what these vital components truly are and how they drive modern operations.
The Core Principle: Seeing with Light
At its heart, a photoelectric sensor operates on a beautifully simple principle: it emits a beam of light (visible, infrared, or laser) and detects changes in that light’s properties. These changes are caused by the presence, absence, distance, or specific characteristics of a target object interrupting or reflecting the beam.
This interaction triggers the sensor’s output, sending a signal to a programmable logic controller (PLC) or other machinery. This signal essentially says, “Something is here,” “Something moved,” “This object has the correct surface properties,” or “This bottle is filled to the right level.” The versatility of this basic function is what makes photoelectric sensors indispensable across countless industries.
Unpacking the Key Variations: Choosing the Right Beam
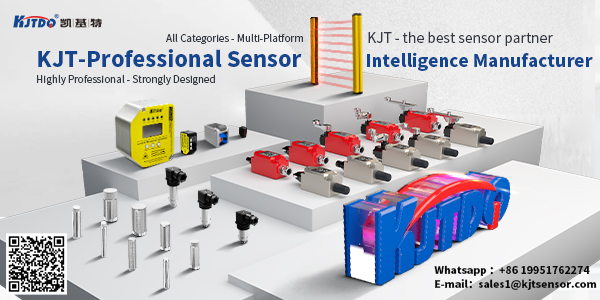
Not all sensing tasks are created equal. Photoelectric sensors come in distinct configurations, each excelling in specific scenarios:
- Through-Beam (Opposed Mode): The undisputed champion for long-range detection and highest reliability. This system uses two separate units: an emitter projecting a continuous beam and a receiver positioned directly opposite. When the beam is broken by an object, detection occurs. Ideal for detecting small objects, opaque materials, or in dusty environments where beam strength matters. However, installation requires precise alignment of two components.
- Retroreflective: Offering a balance of range and simpler installation than through-beam. The emitter and receiver are housed in one unit. A reflector (prismatic or tape) is placed opposite the sensor. The sensor detects the object when it interrupts the beam bouncing back from the reflector. Requires a clean reflector surface but simplifies wiring and mounting significantly. Highly effective for standard presence/absence detection.
- Diffuse (Proximity Mode): The most compact and easiest-to-install option. Emitter and receiver are in one housing. The sensor detects light reflected directly off the target object. Simplicity comes with trade-offs: sensing distance is generally shorter and performance is highly dependent on the target’s color, size, texture, and reflectivity. Bright, reflective objects are easiest to detect. Advanced variations include:
- Background Suppression (BGS): Uses triangulation to detect objects only within a specific, adjustable distance range, ignoring more distant background surfaces. Essential for precise positioning or detecting objects against potentially reflective backgrounds.
- Foreground Suppression (FGS): Focuses detection on objects beyond a set minimum distance, ignoring very close objects or the sensor’s own mounting bracket.
Decoding “RCA”: Connector, Not Sensor Type
This brings us to the “RCA” part of the query. Crucially, RCA in the context of electronic components primarily refers to a specific type of connector – the familiar coaxial plug/socket historically common in audio/video equipment (think old DVD players and TVs). Using an RCA connector on an industrial sensor would be highly unusual and generally impractical today.
It’s far more likely that someone using the term “RCA Photoelectric Sensor” is either:
- Referring to a Specific Brand or Historical Model: RCA Corporation, known for electronics, did manufacture various industrial components decades ago. Someone might be searching for a replacement part for very old machinery using RCA-branded or RCA-connector-equipped sensors.
- Mistakenly Using “RCA” instead of “Retroreflective”: The abbreviation “RCA” could be confused with “RR” (for RetroReflective) in informal communication or documentation.
- Describing a Sensor with M12 Connectors: Modern industrial sensors predominantly use robust, standardized connectors like M8 or M12 (circular connectors with 4, 5, or 8 pins). Occasionally, someone unfamiliar might loosely associate the cylindrical shape of an M12 connector with an RCA plug, though they are functionally and physically distinct.
Therefore, when selecting a photoelectric sensor today, focus is on the sensing mode (through-beam, retroreflective, diffuse) and the target/environment characteristics, not an RCA connector. Modern sensors feature reliable M-series connectors providing power, output signals, and often diagnostic capabilities.
Selecting the Optimal Sensor: Key Considerations
Choosing the right photoelectric sensor isn’t about the connector; it’s about matching the technology to the challenge:
- Sensing Range: How far away is the object?
- Target Characteristics: What is it made of? What color, size, and surface finish (shiny, matte, transparent)? Is it liquid?
- Environmental Factors: Dust, dirt, fog, ambient light, temperature extremes, washdown requirements? Look for appropriate Ingress Protection (IP) ratings.
- Required Output: Simple presence detection (discrete on/off signal) or analog distance measurement?
- Mounting Constraints: Space limitations? Accessibility for adjustment?
- Response Time & Accuracy: How fast must the detection be? How precisely must the object’s position be known?
The Ubiquity of Photoelectric Sensing: Where They Shine
The practical applications are vast and critical:
- Object Detection on Conveyors: Confirming presence, counting items, triggering actions (like sorting or labeling).
- Level Control: Monitoring fill levels in tanks, bins, or bottles (using through-beam or specific diffuse variants).
- Part Positioning: Ensuring components are correctly placed before assembly or machining (Background Suppression excels here).
- Web Breaks: Detecting tears in paper, film, or foil processing lines.
- Robotic Guidance: Providing precise object location for pick-and-place robots.
- Safety Light Curtains (Specialized): Creating protective “light barriers” around hazardous machinery.
- Contrast Detection: Differentiating between labels, marks, or materials based on surface reflectivity.
- Barcode Scanning: Many barcode readers utilize photoelectric sensing principles.
Conclusion: Light as the Ultimate Tool
Photoelectric sensors are fundamental building blocks of automation, providing unmatched versatility and reliable performance in countless detection tasks. Understanding the core working principles – through-beam, retroreflective, and diffuse (with its BGS/FGS variants) – is key to selecting the optimal solution. While the term “RCA Photoelectric Sensor” likely points to historical context or a misconception about connectors, modern sensors focus on sophisticated optics, rugged construction, and standardized M-series interfaces. By harnessing the simple power of light and its interaction with objects, these unsung heroes of industry enable the speed, precision, and efficiency that define modern manufacturing and logistics.