proximity sensor m8
- time:2025-07-05 03:37:01
- Click:0
M8 Proximity Sensors: The Compact Powerhouses Driving Industrial Precision
In the intricate ballet of modern manufacturing and automation, every component counts, especially when space is at a premium. Enter the M8 proximity sensor – a small but mighty workhorse, leveraging its standardized 8mm diameter threaded barrel to deliver reliable, non-contact detection in environments where larger sensors simply won’t fit. Understanding the capabilities and applications of these proximity sensor M8 units is key to optimizing efficiency and reliability in countless systems.
Defining the M8 Form Factor: More Than Just Size
The “M8” designation primarily refers to the sensor’s threaded housing diameter – 8 millimeters. This standardization is crucial in industrial settings. It dictates the size of the mounting hole required (typically M8 x 1.0 or M8 x 1.25 thread pitch) and facilitates easy installation using standard nuts and lock washers. While other form factors exist (like M12, M18, M30), the M8 proximity sensor shines in scenarios demanding minimal spatial footprint without sacrificing performance.
Most commonly, M8 sensors employ inductive technology. This means they generate an electromagnetic field from a coil in their sensing face. When a conductive metal target (like steel, aluminum, brass, etc.) enters this field, it induces eddy currents within the target. The sensor detects the resulting change in the oscillation amplitude or frequency within its own coil. This detection is translated into a clean electrical output signal (usually a transistor switch), indicating the presence or absence of the target – all without physical contact. This non-contact nature is fundamental to their longevity and reliability.
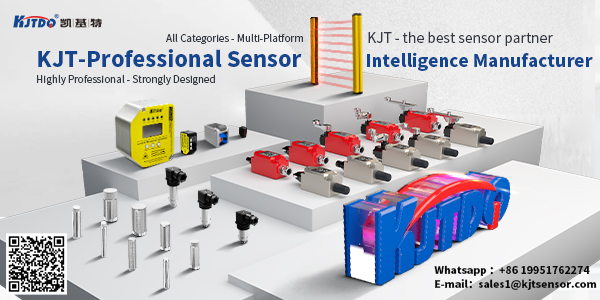
Where Space is Scarce: Key Applications of M8 Sensors
The compactness of the proximity sensor M8 makes it indispensable across numerous sectors:
- Robotics and Cobotics: Inside articulated robot arms, grippers, and collaborative workspaces, space is incredibly constrained. M8 sensors monitor end effector positions, detect part presence in grippers, and ensure safe limits for human-robot interaction.
- Conveyor Systems: Tracking small parts, verifying component placement on pallets or carriers, and detecting jams on densely packed assembly or packaging lines all benefit from the M8’s small profile.
- Machine Tools (CNC Mills, Lathes): Verifying tool changer positions, confirming workpiece clamping/unclamping, and monitoring slide or turret positions often require reliable detection within tight machine cavities.
- Printing and Paper Handling: Detecting paper edge, verifying paper feed through narrow paths, and monitoring roller positions are common uses where larger sensors obstruct the material path.
- Semiconductor Manufacturing: Precision handling and positioning of delicate wafers and components frequently utilize arrays of compact M8 inductive proximity sensors within complex machinery.
- Filling & Dispensing Systems: Monitoring valve positions or verifying bottle/cap presence on high-speed lines leverages their speed and reliability.
Understanding Specifications: Beyond the M8 Thread
Selecting the right proximity sensor M8 requires careful attention to its specifications:
- Sensing Range (Sn): This is the nominal detection distance (e.g., 1mm, 2mm). Crucially, this is standardized for a specific target material (usually mild steel). Detection ranges for other metals (like aluminum, brass, copper) are significantly less – often only 25-50% of the rated Sn. Always check the datasheet for correction factors!
- Sensing Principle: While inductive is dominant for metal detection, M8 sensors are also available in other types:
- Capacitive: Detect both metallic and non-metallic targets (liquids, plastics, wood, etc.) based on changes in electrical capacitance.
- Magnetic (Reed): Activated by the presence of a magnetic field, often used for detecting cylinder piston position via an embedded magnet.
- Photoelectric: Less common in a true M8 threaded barrel, but miniature variants exist. Use light beams (visible, infrared) to detect object presence, color, or contrast.
- Shielded (Flush Mountable) vs. Unshielded (Non-Flush): This impacts mounting and detection field shape.
- Shielded (Flush Mountable): The sensing face is surrounded by a metal shield. This focuses the electromagnetic field forward, allowing the sensor to be mounted flush with (or even recessed into) metal mounting surfaces without interference. Ideal for confined spaces. Sensing range is typically shorter than unshielded equivalents.
- Unshielded (Non-Flush): Lack the front shielding, resulting in a wider, more extended lateral sensing field. They require a small clearance (free zone) from surrounding metal to prevent false triggering. Offer slightly longer sensing ranges than shielded types of the same size.
- Output Type: Determines how the sensor signal interfaces with the control system.
- NPN (Sinking): The output transistor connects the load (like a PLC input) to ground (-) when active. Common in Europe and Asia.
- PNP (Sourcing): The output transistor connects the load to the positive supply voltage (+) when active. Common in North America.
- NO (Normally Open) / NC (Normally Closed): Describes the switching state when no target is present. NO opens the circuit when inactive, closes it when detecting. NC closes the circuit when inactive, opens it when detecting.
- Operating Voltage: Typically ranges from 10-30V DC for standard industrial sensors. Ensure compatibility with your system.
- Environmental Rating (IP Rating): Look for IP67 as a minimum for reliable operation in industrial environments, indicating protection against dust ingress and temporary immersion in water. IP68 or IP69K offer higher protection levels for harsher conditions.
- Connection Type: M8 sensors often feature a pre-wired cable (e.g., 2m length) with flying leads or a molded-on M8 connector (typically 3-pin or 4-pin). M8 connectors provide quick, secure, and standardized connections, simplifying installation and maintenance.
The Enduring Advantages: Why Choose M8?
The proximity sensor M8 offers a compelling set of benefits:
- Extreme Compactness: Fits where larger sensors physically cannot, enabling design flexibility and miniaturization.
- High Reliability: Solid-state design with no moving parts ensures long operational life and resistance to shock and vibration.
- Fast Response Times: Capable of detecting objects at very high speeds, essential for modern high-throughput automation.
- Non-Contact Operation: Eliminates mechanical wear and tear on both the sensor and the target.
- Resilience: Designed to withstand harsh industrial environments – dirt, dust, oil, coolant (with appropriate IP rating).
- Cost-Effectiveness: Provide a reliable detection solution at a competitive price point, especially considering their longevity.
Implementing Effectively: Best Practices
To maximize the performance of your proximity sensor M8:
- Mind the Gap: Respect the specified sensing distance and correction factors for different target materials. Ensure targets consistently enter the effective sensing zone.
- Mount Correctly: Adhere to flush-mounting requirements for shielded sensors and provide adequate clearance for unshielded types. Use the correct tightening torque.
- Consider the Environment: Protect sensors from physical