telemecanique inductive proximity sensor
- time:2025-07-05 03:30:59
- Click:0
Telemecanique Inductive Proximity Sensors: Precision Detection for Demanding Industry
Imagine this: A critical assembly line grinding to a halt because a metal component wasn’t detected, causing a jam. Or a robotic arm misfiring because its position wasn’t accurately sensed. Downtime costs mount, productivity plummets. Reliable object detection isn’t a luxury; it’s the bedrock of efficient, safe, and continuous industrial operation. This is where Telemecanique inductive proximity sensors step in, offering a robust, non-contact solution trusted across countless global applications.
Understanding Inductive Proximity Sensing
At its core, an inductive proximity sensor detects the presence or absence of ferrous and non-ferrous metal objects without physical contact. It generates an electromagnetic field using an oscillator coil. When a metallic target enters this field, it induces eddy currents within the target. This causes a measurable change in the sensor’s own oscillation amplitude or frequency, triggering an output signal (typically switching a relay or transistor). The key advantage? No moving parts, no physical wear, just pure electronic detection.
The Telemecanique Advantage: Built for Industry
Telemecanique Sensors, a flagship brand of Schneider Electric, brings decades of expertise in industrial automation to the table. Their inductive proximity sensor range isn’t just about detection; it’s about delivering reliability, precision, and resilience in the most challenging environments. What sets them apart?
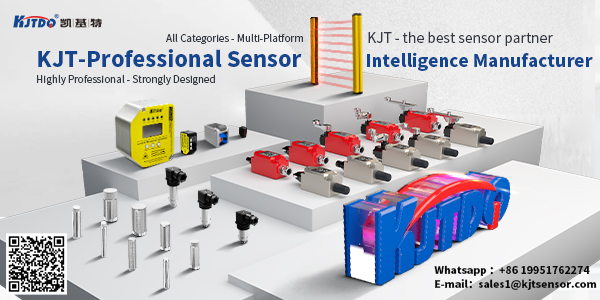
- Uncompromising Durability: Engineered to withstand harsh realities. Many models feature rugged stainless steel housings or robust PBT (polybutylene terephthalate) bodies, offering exceptional resistance to impacts, vibration, and mechanical stress.
- Environmental Protection: Critical for industrial settings. Telemecanique sensors boast high IP (Ingress Protection) ratings (commonly IP67, IP68, IP69K), safeguarding against dust ingress and high-pressure water jets. This makes them ideal for washdown areas in food & beverage or chemical plants.
- Exceptional Sensing Performance: Offering various sensing ranges tailored to specific application needs – from close-range precision detection to longer ranges for bulkier targets. Advanced designs minimize the impact of surrounding metal (shielding) and ensure stable switching points.
- Electrical Robustness: Built with overvoltage, reverse polarity, and short-circuit protection. They resist electromagnetic interference (EMI), ensuring stable operation near motors, drives, and welders. Wide operating voltage ranges guarantee compatibility with diverse control systems.
- Flexible Outputs & Configurations: Available with PNP (sourcing) or NPN (sinking) transistor outputs, along with NO (Normally Open) or NC (Normally Closed) configurations. Diverse form factors (tubular, block, rectangular) and mounting options (flush, non-flush) provide installation flexibility.
- Extended Temperature Tolerance: Designed to perform reliably in extreme temperatures, often ranging from -25°C to +70°C (-13°F to +158°F), with specific models going even wider.
Where Telemecanique Inductive Proximity Sensors Excel
The robustness and versatility of these sensors make them indispensable across a vast spectrum of industries:
- Factory Automation: Counting parts on conveyors, detecting machine tool positions (spindle up/down, turret indexing), verifying presence of pallets or fixtures, monitoring cylinder end positions, and safeguarding machinery through position confirmation (machine guarding).
- Material Handling: Detecting metal containers, verifying bin levels (if metal), controlling sorting gates, confirming package position on lines, and monitoring lift positions.
- Packaging Machinery: Verifying the presence of metal lids or caps, detecting cans or metal containers, confirming the position of filling heads, and monitoring rotary stages.
- Automotive Manufacturing: Precise positioning of robots, detecting engine blocks or chassis components, verifying fixture clamping, and monitoring welding gun position.
- Food & Beverage Processing: Monitoring metal conveyor chains, detecting metal trays or containers (often with specific hygienic designs or IP69K ratings for washdown), and verifying position of metal cutters or fillers (ensuring components are free from food debris build-up).
- Heavy Machinery: Monitoring hydraulic cylinder positions, detecting bucket or boom angles, verifying gear shifts, and safeguarding access doors.
Choosing the Right Telemecanique Sensor
Selecting the optimal inductive proximity sensor hinges on specific application parameters:
- Target Material: Primarily ferrous steel? Or non-ferrous metals like aluminum, brass, or copper? Note: Non-ferrous metals typically require shorter sensing distances.
- Required Sensing Distance: The maximum distance at which the target needs to be reliably detected. Always consider factors like target size, shape, and approach direction.
- Environment: Exposure to chemicals, oils, extreme temperatures, high pressure washdown? Dictates the needed housing material (stainless steel highly recommended for harsh chem/food) and IP rating.
- Electrical Requirements: Supply voltage available? Needed output type (PNP/NPN)? Load current requirements?
- Mounting Constraints: Space limitations? Flush or non-flush mounting permissible? Preferred form factor?
- Special Requirements: Need extra-long cables? High-temperature variants? Resistance to specific chemicals?
Telemecanique’s extensive portfolio, including renowned series like the XS (global workhorse), XCS (metal barrel, stainless steel), XU (universal block style), XZA (specialized for aluminum detection), and XVB (very small factor), ensures a solution exists for virtually any industrial detection challenge.
Beyond the Sensor: The Schneider Electric Ecosystem
Choosing Telemecanique means integrating into the broader Schneider Electric ecosystem. This offers advantages like seamless compatibility with other Telemecanique/Schneider control products (PLCs, HMIs, drives), extensive global technical support, reliable supply chains, and comprehensive documentation. Global availability and support networks minimize downtime risks.
Investing in Reliability and Uptime
In the relentless pursuit of operational efficiency, every component matters. Sensor failures translate directly to costly downtime and lost production. Telemecanique inductive proximity sensors are engineered to be a dependable, long-lasting asset on the factory floor. Their combination of rugged construction, precise detection capabilities, environmental resilience, and Schneider Electric’s backing provides a compelling solution for engineers and maintenance professionals seeking to maximize equipment uptime and process reliability. When consistent, non-contact metal detection is mission-critical, specifying Telemecanique is a strategic choice for industrial success.