linear proximity sensor
- time:2025-07-05 03:43:02
- Click:0
Linear Proximity Sensors: Revolutionizing Precision Measurement in Modern Industry
Imagine unlocking your smartphone with a glance, the screen detecting your presence instantly and effortlessly. Or picture a robotic arm assembling intricate electronics, its movements guided by an unseen eye ensuring perfect alignment every millisecond. This invisible precision isn’t magic; it’s frequently powered by the remarkable capabilities of linear proximity sensors. These unsung heroes of modern automation provide critical non-contact measurements of an object’s position along a straight line, enabling accuracy, reliability, and efficiency where mechanical contact fails.
What Exactly is a Linear Proximity Sensor?
At its core, a linear proximity sensor is a specialized device designed to detect the linear displacement or position of a target object relative to the sensor itself, without requiring physical contact. Unlike simple proximity switches that only indicate presence or absence within a fixed range, linear sensors provide continuous, high-resolution position feedback along a specific axis. This makes them indispensable for applications demanding precise real-time monitoring of movement, distance, or vibration.
The Core Principle: Sensing Without Touch
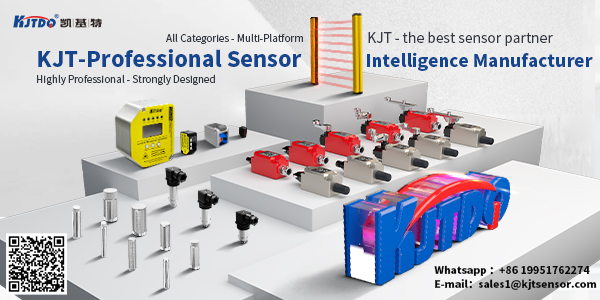
The most common technology underpinning industrial linear proximity sensors is inductive sensing. Here’s how it generally works:
- Generating the Field: An energised coil within the sensor generates a high-frequency alternating electromagnetic field at its active face.
- Target Interaction: When a conductive metal target (like steel, aluminum, brass, or copper) enters this field, eddy currents are induced within the target material.
- Field Dampening: These eddy currents generate their own opposing electromagnetic field, which dampens the original field generated by the sensor’s coil.
- Measuring the Change: The sensor’s sophisticated electronics precisely measure the change in amplitude or phase of the original oscillating circuit caused by this field dampening.
- Position Output: The magnitude of this change is directly proportional to the distance between the sensor’s face and the target. The sensor converts this change into a standard, continuous output signal (typically analog voltage like 0-10V or current like 4-20mA, or digital formats) corresponding linearly to the target’s position.
While inductive sensors dominate for metallic targets, other technologies like capacitive (for non-metals or liquids at close range) and magnetostrictive (for high-precision, long-stroke measurement) also power specialized linear proximity sensors.
Why Choose Linear Proximity Sensing? Key Advantages
The non-contact nature of linear proximity sensors unlocks a suite of compelling benefits that make them superior to traditional contact-based measurement methods like potentiometers or LVDTs in many demanding scenarios:
- Zero Wear & Endless Lifespan: With no physical contact, there’s virtually no mechanical wear on the sensor or the target, leading to significantly extended operational life and reduced maintenance costs.
- High Accuracy and Repeatability: Modern inductive sensors offer exceptional accuracy (often down to micrometer levels) and repeatability, providing reliable data for critical process control.
- Robustness in Harsh Environments: Sealed against dust, dirt, oil, coolants, and high-pressure washdowns, they thrive where other sensors fail. Their immunity to most contaminants makes them ideal for demanding industrial settings like machine tools, foundries, and food processing.
- High Resolution: Capable of detecting minute positional changes, enabling precise control over machinery and processes.
- Maximum Speed: Non-contact sensing allows for measurement of incredibly fast-moving or vibrating targets without introducing drag or bounce.
- Measurement Independence: Performance is generally unaffected by the target’s surface finish, color, or transparency (for inductive types), focusing purely on distance to the conductive surface.
- Simplified Installation: Often require less complex mounting arrangements compared to contact sensors needing linkages or bearings.
Where Precision Matters: Core Applications
The unique advantages of linear proximity sensors make them ubiquitous across countless industries:
- Industrial Automation: Monitoring cylinder rod position in pneumatic/hydraulic systems, controlling press ram position, verifying part placement, checking fill levels through tank walls (capacitive).
- Machine Tooling: Real-time feedback on spindles, slides, and tool positions for precision machining (milling, turning, grinding), ensuring geometric tolerances. Vibration monitoring of spindles and critical components to predict maintenance needs.
- Automotive Manufacturing: Precise measurement of suspension components during assembly, brake pedal travel sensing, throttle position feedback, robotics guidance on assembly lines.
- Robotics: Providing position detection feedback for robotic arm joints and end-effectors, enabling precise path control and object handling.
- Hydraulic & Pneumatic Systems: Accurate monitoring of valve spool positions and actuator piston rods for closed-loop control.
- Material Handling & Packaging: Gauging product thickness or stack height, controlling conveyor positioning, verifying flap or door closure on automated packaging lines.
- Renewable Energy: Monitoring blade pitch or hydraulic actuator positions in wind turbines.
- Semiconductor Manufacturing: Ultra-precise stage positioning in lithography and inspection equipment.
Selecting the Right Sensor: Critical Factors
Choosing the optimal linear proximity sensor requires careful consideration:
- Target Material: Inductive sensors require conductive metals; capacitive sensors work with metals, plastics, liquids, or granular materials.
- Measuring Range: The distance over which the sensor must accurately measure position. Select a sensor whose nominal range comfortably encompasses the application’s travel distance.
- Required Accuracy & Resolution: Define the necessary positional precision and the smallest detectable movement.
- Output Signal: Voltage (0-10V), Current (4-20mA), digital (SSI, IO-Link, CANopen), or discrete switching? Match to the control system input.
- Environmental Conditions: Temperature extremes, presence of dust, moisture, oils, chemicals, or strong electromagnetic fields dictate housing material (stainless steel preferred for harsh environs) and ingress protection (IP) rating.
- Mounting Constraints: Consider sensor size, shape, and required mounting flange or thread.
- Response Time & Frequency: How fast does the target move? Ensure the sensor’s bandwidth can track changes effectively.
- Operating Temperature: Verify the sensor’s specified temperature range suits the application environment.
From the precision required in building a jet engine to ensuring your car’s suspension reacts instantaneously on a bumpy road, linear proximity sensors deliver the non-contact, high-precision position detection that modern technology demands. Their inherent reliability, robustness, and ability to operate in harsh environments make them a fundamental building block for smarter, more efficient, and higher-performing machinery across the global industrial landscape. As automation and precision requirements continue to escalate, the role of these versatile sensors will only become more critical.