hall effects sensor
- time:2025-07-05 03:49:04
- Click:0
Hall Effect Sensors: The Invisible Force Detectors Powering Modern Technology
Think of the last time you flipped open a laptop or a smartphone cover and the screen instantly woke up. Or consider the precise control of a modern electric vehicle’s motor, or the confidence of an anti-lock braking system activating in milliseconds. These seemingly magical feats often rely on a remarkable piece of technology working silently behind the scenes: the Hall effect sensor. Far from being obscure physics lab curiosities, these versatile devices are fundamental building blocks, invisibly enabling precision, reliability, and efficiency across countless industries.
So, what exactly is the Hall effect, and how does it translate into a practical sensor? Discovered by Edwin Hall in 1879, it describes a fascinating phenomenon: when an electrical current flows through a conductor (or semiconductor) placed within a magnetic field, a voltage develops perpendicular to both the current and the field direction. This generated voltage is known as the Hall voltage. Crucially, its magnitude is directly proportional to the strength of the magnetic field and the current, and its polarity depends on the field’s direction (North or South pole).
Hall effect sensors capitalize on this principle. They are essentially semiconductor devices engineered to be highly sensitive to magnetic fields. A basic Hall sensor incorporates:
- A thin strip of semiconductor material (like Gallium Arsenide or Indium Antimonide).
- A constant current source passing through this strip.
- Output electrodes placed perpendicular to the current path to measure the Hall voltage.
When a magnetic field applied perpendicularly to the sensor’s surface interacts with the flowing current, it deflects the charge carriers (electrons or holes), creating a measurable Hall voltage difference across the output electrodes. This tiny voltage signal is then amplified and conditioned by integrated electronics within modern Hall sensor ICs, transforming it into a clean, usable digital or analog output signal.
Why Hall Effect Sensors Dominate Numerous Applications
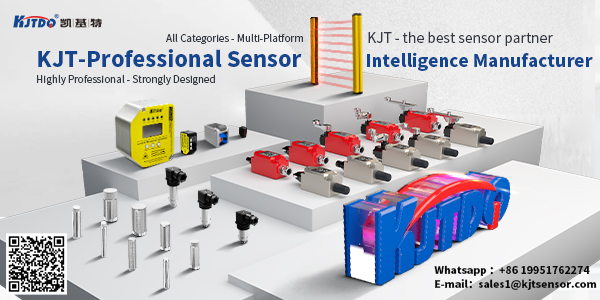
Their unique operating principle grants Hall effect sensors several critical advantages over other sensing technologies:
- Non-Contact Operation: They detect magnetic fields without needing physical contact with the target. This eliminates wear and tear, enhances reliability, and allows sensing through non-magnetic barriers.
- Solid-State Reliability: With no moving parts, they boast exceptional longevity and resistance to shock, vibration, and dust.
- Speed and Frequency Response: Hall sensors can detect rapidly changing magnetic fields, making them ideal for high-speed applications like motor commutation or RPM sensing.
- Operation in Harsh Environments: Many variants are designed to function reliably in extreme conditions – wide temperature ranges, humidity, and even contaminated atmospheres where optical or mechanical sensors might fail.
- Versatility in Output: Modern Hall ICs offer digital (on/off switches), analog (linear output proportional to field strength), and specialized outputs (like PWM or SENT), catering to diverse interface needs.
- Ability to Sense Multiple Parameters: While primarily used for position and movement (via moving magnets), they are equally adept at current measurement (by detecting the field around a current-carrying conductor) and even proximity detection.
Where You’ll Find Hall Effect Sensors in Action (Likely More Places Than You Think!)
The applications of Hall effect sensors are astonishingly broad:
- Automotive: This is a massive market. They are crucial for:
- Wheel Speed Sensing (ABS/TCS/ESP): Detecting the rotation of each wheel for anti-lock braking and stability control.
- Transmission Gear Position: Identifying gear selection (Park, Reverse, Neutral, Drive, etc.).
- Throttle/Pedal Position: Determining accelerator pedal angle for engine management.
- Electric Power Steering (EPS): Sensing torque and position on the steering column.
- Brushless DC (BLDC) Motor Commutation: Precisely controlling the switching sequence in EV motors, fans, and pumps.
- Current Sensing: Monitoring battery charge/discharge and motor currents.
- Industrial Automation & Robotics:
- Linear/Rotary Position Feedback: Gauging the position of actuators, cylinders, and robotic arms.
- End-of-Travel Limit Switches: Providing non-contact position limits.
- Speed Detection (RPM): Measuring rotational speed on conveyor belts, shafts, and motors (e.g., using encoder rings).
- Current Sensing: Protecting motors and drives by monitoring current flow.
- Flow Meters: Detecting the movement of magnetized impellers in fluid flow systems.
- Proximity Switching: Detecting the presence of ferrous metal objects.
- Consumer Electronics:
- Lid/Screen Open/Close Detection: Waking devices when a cover is opened (laptops, flip phones, tablets).
- Joystick/Control Stick Position: Translating stick deflection in game controllers or drones.
- Smartphone Compasses (Magnetometers): Utilizing Hall effect principles for determining direction (though more complex sensors like AMR are often used now).
- Non-Contact Buttons/Dials: Creating sleek, sealed user interfaces.
Medical Devices: Used in equipment requiring reliable, non-contact sensing, such as infusion pumps, ventilators, and robotic surgical tools.
Aerospace & Defense: Critical for flight control systems, engine monitoring (RPM, position), and various instrumentation requiring high reliability.
Power Tools & Appliances: Controlling BLDC motors in drills, vacuum cleaners, and washing machines; detecting door closures.
Choosing the Right Hall Sensor and Key Considerations
Selecting the appropriate Hall effect sensor depends heavily on the application:
- Type: Do you need a simple on/off switch (Digital Bipolar/Unipolar/Omnipolar Hall switch), a linear output proportional to field strength (Linear Hall sensor), or specialized features like latch behavior or gear-tooth sensing (Hall IC)?
- Sensitivity: How strong is the magnetic field you need to detect? Sensor sensitivity is rated in millivolts per Gauss (mV/G) or similar.
- Operating Voltage/Current: Ensure compatibility with your system’s power supply.
- Output Type & Drive Capability: Digital (Open Drain/CMOS), Analog, or specialized? What load can it drive?
- Temperature Range: Will it operate in extreme cold or heat?
- Package & Mounting: Surface-mount (SMD) or through-hole? Considerations for magnetic field orientation are crucial.
- Magnetic Field Direction: Bipolar sensors respond to North and South poles, while Unipolar typically only respond to one pole (usually South).
Hall Effect Sensors vs. Alternatives
While incredibly versatile, Hall sensors aren’t the only solution. Comparing them highlights their strengths:
- Reed Switches: Also magnetic switches, but mechanical (contacts open/close). Less reliable long-term, slower, susceptible to shock/vibration compared to solid-state Hall sensors.
- Optical Encoders: Offer high precision but can be sensitive to dust, dirt, and lighting conditions. Hall sensors excel in dirty/dark environments.
- Inductive Sensors: Detect metal proximity through eddy currents. Work well with ferrous metals but require AC excitation and typically have a shorter sensing range than magnetic Hall sensors.
- Potentiometers: Provide analog position via physical