photo electric sensor working
- time:2025-07-25 02:33:08
- Click:0
The Invisible Engine: How Photoelectric Sensors Work to Automate Our World
Ever pushed a grocery cart through those automatic sliding doors, watched a production line flawlessly sort bottles, or noticed your printer sense when it’s out of paper? Chances are, a silent, unseen workhorse is making it happen: the photoelectric sensor. These remarkable devices are fundamental pillars of modern automation, leveraging the power of light to detect presence, absence, position, distance, and even color or surface characteristics. Understanding how photoelectric sensors work unlocks a world where machines interact reliably and intelligently with their surroundings.
The Core Principle: Light Becomes Information
At its heart, a photoelectric sensor operates on a beautifully simple yet ingenious concept: it uses a beam of light (typically infrared light, invisible to the human eye, though visible red or laser light are also used) to detect an object. The core functionality relies on the interaction between an emitter (light source) and a receiver (light detector), with the object itself playing the crucial role of interrupting or altering this light path. When the light beam is disturbed by the presence (or absence) of an object, the sensor translates this change in light intensity into an electrical signal – a simple ON/OFF switch for the control system. This photoelectric effect – where light energy is converted into electrical energy – is the fundamental physics principle behind their operation.
Key Components: The Emitter and Receiver Duo
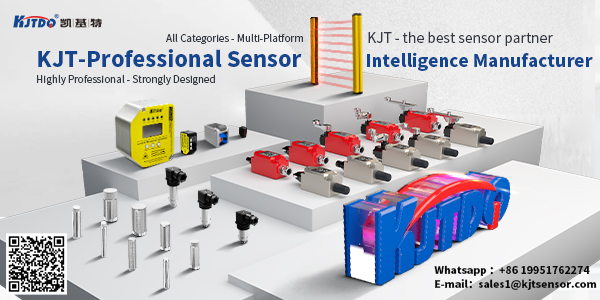
- Emitter (Light Source): This component generates the light beam. Modern sensors predominantly use Light Emitting Diodes (LEDs) due to their long life, low power consumption, and compact size. Infrared LEDs are particularly favored because they are less susceptible to interference from ambient light. The light beam is often modulated – pulsed at a specific high frequency – making the sensor highly resistant to stray light sources like sunlight or room lighting, ensuring reliable detection even in challenging environments.
- Receiver (Photodetector): Positioned to receive the light signal from the emitter (depending on the sensor type), the receiver converts incoming photons (light particles) back into an electrical current. Common receiver types are photodiodes or phototransistors. The receiver’s circuitry is finely tuned to detect the specific modulated frequency emitted by its paired emitter, further enhancing noise immunity.
The Three Primary Operating Modes
The magic of photoelectric sensors lies in their versatility, achieved through three distinct physical configurations:
- Through-Beam (Opposed Mode):
- How it Works: The emitter and receiver are housed in separate units, positioned directly opposite each other. The emitter sends a continuous beam of light directly to the receiver. An object is detected when it physically blocks the beam, interrupting the light path to the receiver.
- Key Advantage: This mode offers the longest sensing ranges (often meters) and is generally the most reliable because it requires a complete physical obstruction. It’s highly immune to factors like object color, surface finish, or reflectivity – if it’s opaque and breaks the beam, it’s detected.
- Common Uses: Detecting large objects, product counting on conveyors, checking for presence in machine guarding (safety light curtains are a specialized form), gate control, package height verification.
- Retro-Reflective (Reflex Mode):
- How it Works: The emitter and receiver are combined into a single housing unit. The emitted beam is directed towards a specially designed reflector (corner-cube or fresnel lens type). This reflector sends the beam precisely back to the receiver within the sensor housing. An object is detected when it interrupts the light beam traveling to the reflector or from the reflector back to the sensor.
- Key Advantage: Offers good sensing distances (comparable to, but usually slightly less than, through-beam at the same power level) with simpler wiring, as only one device needs to be mounted and wired. Reliable detection of opaque objects. Requires a reflector opposite the sensor.
- Consideration: Highly reflective objects passing nearby can sometimes bounce enough light back to the receiver without the reflector, causing a false “beam present” signal. Polarized filters are often used (both on the sensor and reflector) to mitigate this – the sensor emits polarized light, and the reflector rotates the polarization, so only light coming from the reflector is recognized by the polarized receiver filter.
- Common Uses: Pallet detection in warehouses, conveyor transfer points, detecting vehicles or objects on assembly lines, door open/close detection where mounting two separate units is impractical.
- Diffuse (Proximity Mode):
- How it Works: Again, the emitter and receiver are housed together. The emitter sends out a beam of light. When this light strikes a target object within its range, the object diffusely reflects (scatters) some of the light back towards the sensor. The receiver detects this reflected light. Detection occurs when the amount of reflected light exceeds a preset threshold.
- Key Advantage: The simplest installation – no separate reflector or separate receiver unit is needed. Only one device is mounted. Excellent for detecting objects without requiring access to the opposite side.
- Consideration: Sensing range is generally shorter than through-beam or retro-reflective. Detection is highly dependent on the target object’s size, color, surface texture, and reflectivity. A matte black object reflects much less light than a shiny white one, requiring careful adjustment of the detection threshold or sensor selection. Background suppression variants use triangulation principles to detect objects only within a specific distance range, ignoring objects beyond (the background). Convergent beam models focus sharply at a set distance for small object detection.
- Common Uses: Detecting objects on conveyors (especially smaller parts), fill level detection in transparent bottles or containers (using specific models), label detection, presence sensing in machinery, robotics end-effector positioning, detecting objects in bins.
The Output: Speaking the Machine Language
Once the sensor determines an object is present or absent (based on the beam state), it communicates this state to the control system (like a PLC) via its output circuit. The two most common output types are:
- Digital Output (Discrete): The simplest and most common. Provides a straightforward ON/OFF signal. It’s either Light Operated (LO) / Light-On (L-On) - Output ON when beam is received/unobstructed. Or Dark Operated (DO) / Dark-On (D-On) - Output ON when beam is blocked/object present.
- Analog Output: Provides a continuous signal (e.g., 0-10V or 4-20mA) proportional to the distance the object is from the sensor or the amount of light received. Used for precise distance measurement or detecting subtle changes in position. (More common in specialized distance sensors).
Outputs are typically implemented using either NPN (sinking) or PNP (sourcing) transistors, defining how they interface with the control system’s input card.
Why They Reign Supreme in Automation
The widespread adoption of photoelectric sensors stems from compelling advantages:
- Non-Contact Sensing: Detection occurs without physically touching the object, eliminating wear and tear and allowing detection of delicate or fast-moving items.
- High Speed and Precision: Capable of detecting objects moving at high speeds with pinpoint accuracy.
- Long Sensing Ranges: Through-beam and retro-reflective models offer detection over significant distances.
- Versatility: The three main modes cover an enormous range of applications. Specialized variants exist for challenging conditions (e.g., fiber optic sensors for tiny spaces or high temperatures, color sensors, luminescence sensors).
- Reliability: Robust construction and advanced features like *modulation