irb mon photoelectric sensor
- time:2025-07-25 02:28:04
- Click:0
IRB Mon Photoelectric Sensors: The Essential Eyes for ABB Robotic Precision
The relentless drive for automation demands more than just powerful robotic arms; it requires perception. In the intricate dance of modern manufacturing, where ABB’s renowned IRB series robots execute tasks with superhuman speed and accuracy, their true potential is unlocked only when they can “see” and respond to their environment. This critical vision is often provided by photoelectric sensors, and understanding their synergy with the ABB IRB platform – particularly the concept encapsulated in searches like “irb mon photoelectric sensor” – reveals a cornerstone of industrial efficiency. Let’s explore why these sensors are indispensable companions for ABB robotics.
Beyond Muscle: Why Robots Need Sensory Perception
Imagine a robotic arm tasked with picking components off a moving conveyor belt. Without sensing:
- It might grasp thin air if a part is missing.
- It could collide with an unexpected obstacle.
- Precise placement becomes a gamble without confirmation.
- Jams go undetected, leading to costly downtime.
This is where photoelectric sensors come in. Acting as the robot’s primary “eyes,” they detect the presence, absence, position, distance, or characteristics of objects without physical contact. They achieve this by emitting a light beam (visible, infrared, or laser) and analyzing how that light interacts with the target – either through reflection, interruption, or beam reception.
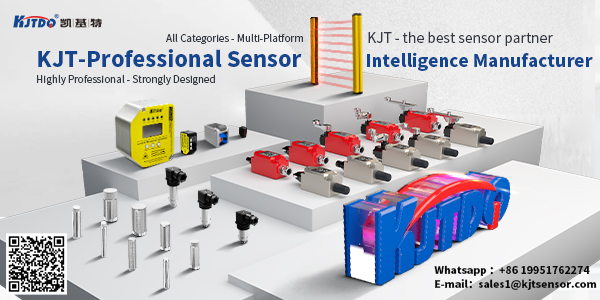
The Perfect Match: Photoelectric Sensors & ABB IRB Robots
The ABB IRB series, encompassing models from compact cobots to powerful industrial arms, is celebrated for its speed, precision, and reliability. Integrating photoelectric sensors enhances these attributes significantly:
- Enhanced Precision and Accuracy: Sensors provide real-time feedback on part position or orientation before the robot acts. This allows for micro-adjustments, ensuring perfect placement, insertion, or assembly. A tiny shift detected by a precision sensor prevents a costly misalignment.
- Optimized Cycle Times: By accurately detecting the arrival of parts on a feeder or conveyor, the robot can initiate its task immediately, eliminating waiting periods. Sensors also confirm task completion (e.g., part picked, hole drilled), allowing the robot to proceed instantly to the next step.
- Robust Process Reliability: Photoelectric sensors excel at error-proofing. They verify part presence before a machining operation, check for correct part orientation before assembly, and detect jams or misfeeds instantly. This reduces scrap, prevents damage to expensive tooling or the robot itself, and ensures consistent quality.
- Improved Flexibility: Sensors enable robots to handle variations. Detecting different part sizes, colors (using color sensors, a photoelectric subtype), or subtle positional differences allows a single robotic program to manage a wider range of products without physical re-tooling.
- Integrated Safety: While separate safety systems handle personnel protection, photoelectric sensors contribute to process safety. They can detect when a guarding door is open, verify safe clearances before robot movement, or sense unexpected intrusions into a work cell, triggering a controlled stop.
Key Considerations When Choosing Sensors for IRB Applications
Not all photoelectric sensors are created equal, especially in the demanding world of industrial robotics. Factors crucial for successful ABB IRB sensor integration include:
- Detection Method:
- Retro-reflective: Beam bounces off a reflector; ideal for longer ranges. Requires a reflector opposite the sensor.
- Diffuse-reflective (Proximity): Sensor emits light and detects reflection from the target itself. Simpler setup, but range and background interference can be challenges. Best for close-range presence detection.
- Through-beam: Separate emitter and receiver; beam interruption signals detection. Offers the longest range, highest accuracy, and immunity to target color/surface. Ideal for precise positioning or small object detection.
- Range and Precision: Match the sensor’s operating range to the robot’s work envelope and required detection distances. Sub-millimeter precision is often needed for positioning tasks. Laser sensors often excel here.
- Response Time: Robotics demand blistering speed. Sensor response time must be fast enough to keep pace with the robot’s movements and conveyor speeds without introducing lag. Look for microsecond response specs.
- Robustness (IP Rating): The industrial environment is harsh. Sensors must withstand dust, coolant, vibration, and electromagnetic interference. High IP67/IP68/IP69K ratings are typical requirements.
- Output Type & Connectivity: Compatibility with the robot controller (ABB’s IRC5 or OmniCore) or PLC is vital. Digital outputs (PNP/NPN) are standard, but IO-Link is increasingly valuable for advanced diagnostics and parameterization. Easy mounting solutions are also key.
- Environmental Factors: Target color, surface finish (shiny/dull), transparency, ambient light levels, and background objects can all impact sensor performance. Testing in the actual application is critical.
Real-World Applications: Where “IRB Mon Photoelectric Sensors” Shine
The synergy of ABB robots and photoelectric sensors drives countless processes:
- Material Handling & Palletizing: Detecting boxes/crates arriving on conveyors for pickup; verifying layer completion during pallet building; ensuring gripper engagement with the object.
- Assembly: Precise positioning of parts onto fixtures; verifying screw presence before driving; checking connector or pin alignment before mating.
- Machine Tending: Detecting when a CNC spindle door opens/closes for safe access; precisely positioning raw material in the chuck; verifying finished part removal.
- Packaging: Detecting filled bottles/cans entering the filling line; checking cap presence and orientation; verifying label application; sensing case flaps for sealing.
- Quality Inspection: Using specialized sensors (color, contrast, luminescence) to identify defects, color variations, or missing labels. Confirming the presence of seals or specific components.
Seamless Integration: Making it Work
Successfully implementing photoelectric sensors on an ABB IRB robot requires careful planning:
- Sensor Selection: Choose the right type, range, precision, and robustness based on the specific task and environment. Consult sensor manufacturer datasheets and application engineers.
- Optimal Placement: Position sensors to avoid occlusion by the robot arm, gripper, or other machinery. Ensure a clear line of sight and consider mounting stability under vibration. Strategic placement is critical.
- Wiring & Signal Handling: Route cables safely using cable carriers to prevent snagging or damage. Connect sensor outputs to the correct robot controller inputs or PLC modules. Implement necessary signal conditioning if required.
- Programming & Logic: Integrate the sensor signals into the robot program using RAPID or via the PLC program. Develop robust logic for handling detections, non-detections, and error conditions. Proper error handling routines are non-negotiable for reliability.
- Testing & Calibration: Rigorously test the sensor functionality under all expected operating conditions. Calibrate thresholds and sensitivity as needed to ensure reliable detection without false triggers.
Selecting the right photoelectric sensor for your ABB IRB application isn’t just an accessory choice; it’s a fundamental decision impacting precision, efficiency, and overall system reliability. By understanding the critical role these sensors play as the robot’s “eyes,” and carefully matching their capabilities to the demands of the task and the environment, engineers unlock the full, intelligent potential of their robotic automation, turning raw mechanical power into seamless, adaptable, and highly productive manufacturing solutions. The integration of