woods photoelectric switch
- time:2025-07-25 02:22:56
- Click:0
Woods Photoelectric Switches: Rugged Sensing Solutions for Demanding Environments
Imagine an automated forestry operation. Timber moves swiftly along conveyors, logs are precisely positioned by robotic arms, and sorting gates snap open and shut with unwavering accuracy. Now, picture this intricate dance happening amidst sawdust clouds, relentless rain, freezing temperatures, and the constant threat of physical impacts. What unseen sentinel ensures reliability in such unforgiving conditions? The answer often lies in the robust heart of a woods photoelectric switch.
While the term “woods photoelectric switch” might initially evoke images of sensors literally made of wood, its true meaning is far more practical and powerful. It refers to photoelectric sensors specifically designed and ruggedized to perform flawlessly in environments reminiscent of the woods or forests – places characterized by dirt, dust, moisture, extreme temperatures, vibration, physical obstructions, and limited visibility. These are the workhorses of automation where standard sensors would falter.
Beyond the Forest Floor: The Core Principles
At their essence, all photoelectric switches operate on a simple, reliable premise: they emit a beam of light (typically infrared, visible red, or laser) and detect either its presence, absence, or reflection. This detection triggers an electrical output signal. The main types include:
- Through-Beam (Opposed Mode): Consists of a separate emitter and receiver unit facing each other. Detection occurs when an object interrupts the light beam traveling between them. Renowned for long sensing ranges and high reliability.
- Retroreflective: Uses a single housing containing both emitter and receiver, along with a reflector. The emitter’s light beam bounces off the reflector back to the receiver. An object breaks this return beam to signal detection. Offers easier alignment than through-beam for moderate ranges.
- Diffuse (Proximity Mode): Emitter and receiver are in one unit. The sensor detects light reflected directly off the target object itself. Simplest to install but generally has shorter ranges and is more susceptible to the target’s color, texture, and reflectivity.
Why the Woods Demand More
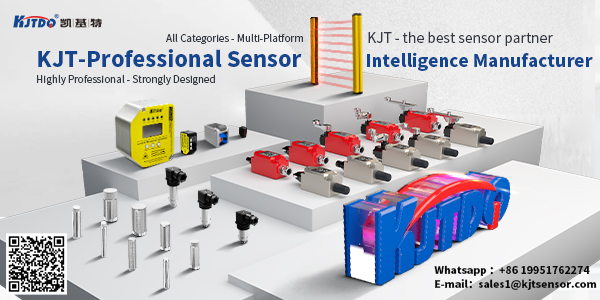
Standard warehouse photoelectric sensors would quickly succumb in “woods-like” industrial settings. Consider these challenges:
- Dust and Debris Avalanche: Sawmills generate clouds of fine sawdust; quarries produce mineral dust; agriculture kicks up soil and chaff. This particulate matter can coat lenses, obscuring the light beam.
- Moisture Onslaught: Rain, snow, sleet, humidity, even high-pressure washdowns are commonplace. Standard sensors aren’t waterproof.
- Temperature Extremes: From scorching summer heat in metal yards to sub-zero freezer warehouses, components must expand, contract, and function reliably.
- Physical Abuse: Vibrations from heavy machinery, impacts from falling debris or accidental bumps during operation, and caustic chemicals demand robust construction.
- Limited Visibility: Mist, steam, heavy dust clouds, or dense foliage (in literal outdoor applications) can scatter light beams, leading to false triggers or missed detections.
The Hallmarks of a True “Woods” Photoelectric Switch
To conquer these harsh realities, woods photoelectric switches incorporate several critical design features:
- Enhanced Environmental Sealing: Look for high IP (Ingress Protection) ratings. IP67 is often considered a baseline for demanding environments, meaning the sensor is dust-tight and can withstand temporary immersion in water (1 meter for 30 minutes). IP68 offers protection against prolonged immersion, while IP69K guarantees resilience against high-pressure, high-temperature washdowns – essential for food processing or areas needing stringent cleaning.
- Ruggedized Housing: Constructed from durable materials like stainless steel (V4A / 316L) or heavy-duty, chemical-resistant plastics (PBT, PVDF). These housings protect delicate internal electronics from impacts, crushing forces, and corrosion.
- Sealed Optics and Connections: Lenses are sealed to prevent dust and water ingress. Cable exits and connection points (M12 connectors are common) are robustly sealed. Potting compounds may be used internally to protect circuitry from vibration, moisture, and thermal shock.
- Advanced Optics & Powerful Emitters: Utilize bright LEDs or lasers capable of penetrating light obstructions like dust, mist, or steam to a greater degree than standard sensors. Sophisticated optics focus the beam for better performance in adverse conditions. Features like background suppression in diffuse sensors become crucial for reliable object detection amidst varying background surfaces or debris.
- Temperature Resilience: Engineered with components and designs that operate reliably across wide temperature spectrums, often -25°C to +70°C (-13°F to +158°F) or broader. This ensures functionality in unheated sheds or outdoor installations year-round.
- Vibration and Shock Resistance: Designed to withstand the constant tremors of heavy machinery without losing calibration or failing.
Where Woods Photoelectric Switches Prove Indispensable
The applications extend far beyond literal forests, encompassing any harsh industrial sector:
- Forestry & Sawmills: Log positioning on infeed decks, log counting, saw blade protection, board sorting, lumber stack height control, detecting logs on conveyors through heavy sawdust.
- Material Handling (Aggregates, Mining, Recycling): Monitoring conveyor belt load levels, detecting oversized rocks or metal, counting items on fast-moving lines, bin level detection in dusty silos, controlling sorting gates.
- Agriculture & Grain Handling: Grain bin level monitoring, detecting product flow in augers and elevators, controlling seed or feed dispensing, monitoring machinery positions in dusty barns or fields.
- Food & Beverage Processing: Package counting on high-speed lines, bottle/can presence detection on wet, steamy, or cold fillers, cap placement verification, washdown area machine guarding (IP69K essential).
- Waste Management & Recycling: Detecting material on conveyors, controlling sorting arms, monitoring compactor positions, bale counting.
- Heavy Machinery & Construction: Position sensing on excavators or loaders, safety interlocks on access doors/hoods, monitoring component movement in dirty environments.
- Outdoor Automation: Gate control systems, vehicle detection in parking lots or toll booths exposed to weather, monitoring storage areas.
Selecting the Right Woods Photoelectric Sensor
Choosing the optimal sensor requires careful consideration:
- Environment: Precisely define the threats: dust type, water exposure level (splash vs. immersion vs. steam/high-pressure wash), temperature extremes, vibration levels, potential for impacts, presence of chemicals? This dictates the required IP rating and housing material.
- Application: What needs detection? Target size, material, color? Required sensing distance? Speed of the target? This determines the best sensing mode (Through-beam, Retroreflective, or Diffuse) and any special features needed (e.g., background suppression for dark targets).
- Output & Connectivity: Does the control system need a simple PNP/NPN signal, a relay output, or an IO-Link connection for diagnostics? M8 or M12 connector type?
- Range & Beam Characteristics: Ensure the sensor’s specified range accommodates the installation distance. Consider beam spot size – a narrower laser beam might be needed for small object detection.
Conclusion: The Unseen Guardians of Harsh Automation
Woods photoelectric switches are not mere components; they are engineered fortresses, purpose-built to deliver unwavering reliability where delicate electronics fear to tread. By integrating advanced optics within robust, sealed enclosures capable of shrugging off dust, water, impacts, and temperature swings, they enable automation to thrive in the industrial equivalent of the deep woods – sawmills, quarries, farms, processing plants, and beyond. Investing in the right ruggedized photoelectric sensor isn’t just about detection; it’s about ensuring uptime, minimizing