photoelectric strain gauge
- time:2025-07-24 03:19:05
- Click:0
The Light Touch: How Photoelectric Strain Gauges Measure Deformation with Precision
Forget wires and resistance changes for a moment; imagine measuring the subtle flex of a bridge or the twist of a turbine blade not with electrical current, but with beams of light. That’s the remarkable capability offered by photoelectric strain gauges, a sophisticated technology transforming how engineers capture critical stress and strain data in demanding environments.
Strain gauges are the unsung heroes of engineering, providing vital information about how materials deform under load. While traditional foil strain gauges have served faithfully for decades, relying on changes in electrical resistance to infer strain, they face limitations. Susceptibility to electromagnetic interference (EMI), challenges in harsh environments (high temperatures, moisture, corrosive atmospheres), and the need for physical wiring can be significant drawbacks.
Photoelectric strain gauges offer a fundamentally different and often superior approach. These devices exploit the interaction between light and a sensing element whose optical properties change in response to applied mechanical strain. They represent a cutting-edge branch of optical strain measurement.
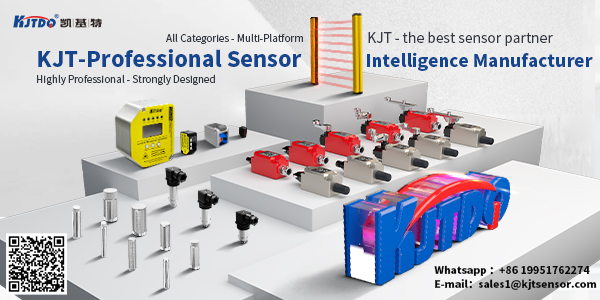
Here’s how these sophisticated sensors typically function:
- Light Source: A coherent light source, often a laser diode or LED, generates the probing light beam.
- Sensing Element: This is the core. It can be a specially prepared optical fiber (the basis of Fiber Bragg Grating (FBG) sensors) or a miniature optical cavity. Crucially, its physical characteristics change when strain is applied – its length might alter, or the spacing of internal reflective structures might shift.
- Light Modulation by Strain: As the structure under test deforms, it deforms the attached or embedded sensing element. This deformation alters how the light propagates through or reflects off the sensing element. Key parameters affected include:
- Wavelength: In FBGs, applied strain directly shifts the wavelength of light reflected by the grating structure. This is a direct optical measurement of strain.
- Phase: In interferometric types (like Fabry-Pérot interferometers), strain alters the optical path length within a cavity, causing a measurable phase shift in the interfering light waves.
- Intensity: Some simpler designs might modulate the intensity of transmitted or reflected light based on strain-induced misalignment or bending losses (though wavelength and phase shifts offer higher precision and stability).
- Optical Signal Transmission: The modulated light signal travels back from the sensing element, typically via an optical fiber. This provides inherent electrical isolation and immunity to EMI.
- Signal Processing & Interrogation: A sophisticated electronic unit, the interrogator, receives the optically encoded strain data. It precisely measures the changes in wavelength, phase, or intensity and converts this information into an accurate digital strain reading, often in microstrain (µε) units.
Why choose photoelectric strain gauges? Their advantages are compelling in specific applications:
- Immunity to Electromagnetic Interference (EMI): This is perhaps their most significant benefit. Using light and non-conductive optical fibers means they operate flawlessly near high-voltage equipment, powerful motors, welding operations, or strong radio frequencies where traditional gauges fail or provide noisy data.
- Intrinsic Safety: The absence of electrical currents at the measurement point makes them ideal for use in hazardous environments like oil and gas facilities, mines, or anywhere explosive atmospheres are a risk. The optical signal carries no ignition risk.
- High Temperature Performance: Certain types, particularly FBG sensors written into specialized high-temperature optical fibers, can reliably operate at temperatures exceeding 600°C or even 1000°C – far beyond the capability of standard foil gauges.
- Long-Distance Signal Transmission: Optical fibers experience minimal signal degradation over kilometers, allowing monitoring points to be located far from the interrogation unit. This is crucial for large-scale infrastructure like dams, bridges, pipelines, and power transmission towers.
- Multiplexing Capability: A single optical fiber can often carry multiple sensing elements (e.g., numerous FBGs at different wavelengths). This enables distributed strain sensing or dense arrays of measurement points along a structure with minimal cabling complexity, known as quasi-distributed sensing.
- High Sensitivity and Accuracy: Advanced photoelectric systems can detect minute strain changes with excellent resolution and stability, rivaling or exceeding the best electrical strain gauges.
- Corrosion and Moisture Resistance: Optical fibers are inherently resistant to many corrosive agents and unaffected by moisture, enhancing durability in challenging field conditions.
Naturally, no technology is universally perfect. Considerations include:
- Cost: The initial investment for the interrogation unit and specialized sensors is typically higher than a basic foil gauge setup. However, the total cost of ownership can be favorable for large or complex installations due to multiplexing and reduced cabling.
- Complexity: Installation and system setup often requires more specialized expertise compared to bonding a simple foil gauge. Precise alignment and handling of optical components are critical.
- Fragility: Optical fibers, while strong when cabled, require careful handling during installation to avoid breakage or excessive bending losses. The sensing points themselves can be robust if properly packaged.
- Surface Preparation & Bonding: Like traditional gauges, proper surface preparation and adhesive selection are crucial for accurate strain transfer, especially for externally mounted sensors.
Where does this technology truly shine? Photoelectric strain gauges excel in demanding scenarios:
- Structural Health Monitoring (SHM) of Critical Infrastructure: Continuously monitoring bridges, dams, wind turbine blades, pipelines, aircraft wings, and historical buildings for signs of fatigue, overload, or damage.
- High-Voltage & Power Generation: Monitoring strain on power transformers, generators, switchgear, and transmission lines where EMI is pervasive.
- Aerospace & Defense: Testing and monitoring airframes, rocket components, and propulsion systems exposed to extreme temperatures, vibrations, and EMI.
- Composite Material Testing: Ideal for embedding within composite structures during manufacturing and testing to understand internal strain distributions without adding electrical paths.
- Geotechnical & Civil Engineering: Monitoring strain in tunnels, retaining walls, foundations, and slopes, often over long distances in corrosive soil conditions.
- Harsh Industrial Environments: Chemical plants, refineries, mines, and nuclear facilities where traditional sensors struggle.
Photoelectric strain gauges represent a powerful evolution in deformation measurement. By harnessing light instead of electricity, they overcome fundamental limitations of their traditional counterparts, opening doors to monitoring in previously inaccessible or challenging environments. As the technology matures and costs become more accessible, their role in ensuring the safety, reliability, and longevity of our critical infrastructure and advanced machinery is set to grow exponentially. They are not just sensors; they are light-powered sentinels watching over the integrity of our engineered world.