photo eye sensor types
- time:2025-07-24 01:21:45
- Click:0
Unveiling the Spectrum: Exploring the Essential Photo Eye Sensor Types
In the intricate dance of modern automation, where machines communicate silently and processes unfold with uncanny precision, lies a critical yet often unseen player: the photo eye sensor. These sophisticated electronic eyes, fundamental to countless industries, detect the presence, absence, or position of objects using light. But what many don’t realize is the significant diversity within this category. Choosing the wrong type can lead to unreliable operation, costly downtime, or safety hazards. Understanding the distinct photo eye sensor types is therefore not just technical knowledge – it’s crucial for optimizing performance, enhancing safety, and driving efficiency across automated systems. Let’s illuminate the primary categories and their unique strengths.
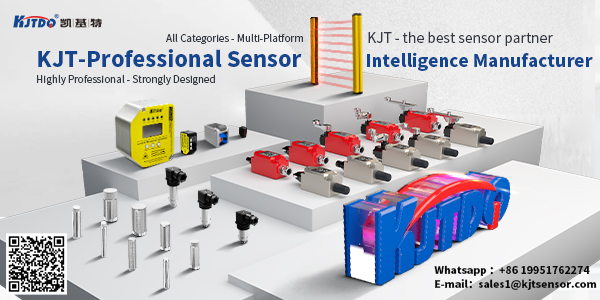
The world of photo eye sensors fundamentally revolves around the interaction between an emitted light beam and a target object. How that beam is generated, directed, and ultimately received determines the sensor’s type, capabilities, and ideal applications. The three dominant categories are through-beam, retro-reflective, and diffuse reflective sensors, each offering distinct solutions.
1. Through-Beam Sensors: The Long-Range Champions
- Principle: This setup involves two separate physical units: an emitter (light source) and a receiver. Positioned directly opposite each other, the emitter projects a focused beam of light towards the receiver. Detection occurs when an object physically interrupts this beam path, preventing the light from reaching the receiver.
- Advantages: Through-beam sensors reign supreme in long-distance detection. They offer the highest sensing ranges among photo eyes, often exceeding 30 meters or more. They provide excellent reliability and immunity to target object characteristics like color, surface finish, or reflectivity. Since detection relies purely on beam interruption, they are highly accurate and less prone to false triggers caused by challenging surfaces or ambient light fluctuations.
- Disadvantages: The main drawback is installation complexity. Requiring precise alignment of two separate units across the detection path can be cumbersome, especially in tight spaces or on moving machinery. Wiring both components also adds to the setup time and cost. Additionally, they require mounting points on both sides of the detection area, which isn’t always feasible.
- Typical Applications: Through-beam sensors excel in scenarios demanding high range and reliability. Examples include:
- Object counting on high-speed conveyor belts.
- Overhead door safety curtains preventing closure when obstructed.
- Pallet position verification in large warehouses.
- Detecting large objects or vehicles over extended distances.
2. Retro-Reflective Sensors: The Convenient Alternative
- Principle: Retro-reflective sensors combine the emitter and receiver into a single housing. They project a light beam towards a specialized reflector (retro-reflector or tape) strategically placed opposite the sensor. This reflector is designed to bounce the emitted light beam directly back along its original path to the receiver within the sensor housing. An object entering the detection zone interrupts this reflected beam, triggering detection.
- Advantages: The key benefit is simplified installation. Only one unit requires mounting and wiring on the machine side, with the reflector placed opposite. This significantly eases setup compared to through-beam sensors, especially where space or access is limited. They offer good sensing ranges, typically shorter than through-beam but longer than diffuse sensors. Alignment is generally easier as it primarily involves pointing the sensor at the reflector. Compared to through-beam, they are often more cost-effective for applications within their range limits.
- Disadvantages: Sensing range is inherently less than through-beam. Contamination is a critical vulnerability: dust, dirt, or grime on the reflector surface can significantly degrade performance or cause false non-detections. Certain materials, like highly reflective metals, might bounce light directly back without the reflector, potentially causing false triggers. Performance can also be affected by the angle or cleanliness of the target object itself if it reflects light back to the sensor.
- Typical Applications: Retro-reflective sensors are ideal where through-beam installation is impractical but longer range than diffuse is needed. Common uses include:
- Automatic doors (sensing approach).
- Box presence detection on conveyors.
- Label detection on packaging lines.
- Pallet height verification at dock doors.
- Machine guarding applications (using safety-rated variants).
3. Diffuse Reflective Sensors: Proximity Detection Experts
- Principle: Like retro-reflective sensors, diffuse sensors house the emitter and receiver together. However, they operate by detecting light reflected diffusely off the target object itself. The sensor emits a beam; when a target enters its field of view, light scatters off the object’s surface in many directions, and some portion returns to the sensor’s receiver.
- Advantages: The standout feature is single-sided operation. No reflector is needed; only the target object is required within the detection zone. This offers the simplest, most flexible installation of all photo eye types. They are well-suited for close-range proximity detection. Many modern diffuse sensors feature background suppression (BGS) or foreground suppression (FGS) technology, enhancing their ability to detect objects reliably at a specific distance while ignoring objects or surfaces beyond (or in front of) the set point. Compact designs are readily available.
- Disadvantages: Sensing range is typically the shortest among the three types. Performance is highly dependent on the target object’s properties. Factors like color (darker objects reflect less light), surface texture (matte vs. glossy), size, and even angle relative to the sensor significantly impact reliability. Environmental factors like ambient light or dusty conditions can also cause issues if not properly selected or shielded. Setting the detection threshold can sometimes require more fine-tuning.
- Typical Applications: Diffuse sensors thrive in close-range object detection where mounting reflectors is impossible or impractical. Examples include:
- Bottle/can presence detection on filling lines.
- Small part verification in assembly machinery.
- Stack height control.
- Detecting objects in bins or containers.
- Robot end-effector tooling detection.
Selecting the optimal photo eye sensor type hinges on a clear assessment of the application requirements. Ask critical questions: What is the required detection range? How reliable must detection be, and what environmental challenges exist (dust, light, vibration)? What are the target object characteristics (size, color, surface, material)? Are there space constraints or limitations on mounting points? Is background suppression needed for precise positioning? By weighing these factors against the inherent strengths and weaknesses of through-beam, retro-reflective, and diffuse reflective technologies, engineers and technicians can deploy the right electronic eyes to ensure seamless, safe, and efficient automation. Understanding this spectrum empowers smarter design choices and unlocks peak operational performance across diverse industrial landscapes.