low voltage photoelectric switch
- time:2025-07-24 00:25:37
- Click:0
The Safety & Efficiency Advantage: Unlocking Potential with Low Voltage Photoelectric Switches
Imagine a busy manufacturing line where robots and humans work in close proximity. Conveyors zip components past assembly stations, intricate machines perform precise tasks, and technicians perform vital checks. In this dynamic environment, safety isn’t just a box to tick; it’s the absolute bedrock of smooth, reliable operation. One critical component ensuring both safety and seamless function in countless automated processes is the often-overlooked low voltage photoelectric sensor. These versatile workhorses offer a compelling blend of security, efficiency, and adaptability, making them indispensable in modern industrial and commercial settings.
Understanding the Core: What is a Low Voltage Photoelectric Switch?
At its heart, a photoelectric sensor, or photoelectric switch, uses light to detect the presence or absence of an object, its distance, or surface characteristics. It consists typically of an emitter (producing a light beam, often infrared, red LED, or laser) and a receiver. When this emitted light beam is interrupted, reflected, or refracted by a target object, the receiver detects this change and triggers an output signal – essentially acting as an electronic switch.
The defining characteristic of a low voltage photoelectric switch is its operating voltage range. While standard industrial sensors often run on 10-30V DC or 24-240V AC/DC ranges, low voltage variants are specifically designed to operate at voltages typically below 30V DC, with many common models optimized for 10-30V DC or even lower ranges like 5V DC or 12V DC. This isn’t just a minor specification; it unlocks significant advantages.
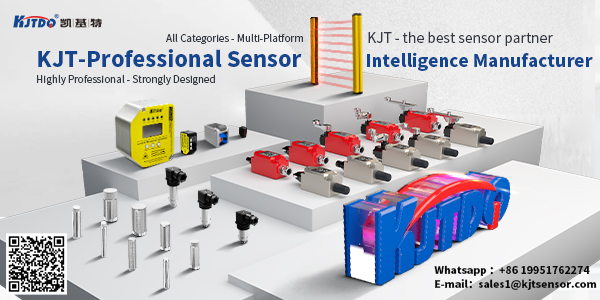
Why Choose Low Voltage? The Compelling Benefits
- Enhanced Personnel Safety: This is the paramount advantage. Lower operating voltages significantly reduce the risk of severe electrical shock to personnel during installation, routine maintenance, or accidental contact. This is crucial in environments where sensors are frequently accessed, cleaned, or adjusted, or where conductive dusts or liquids might be present. They contribute immensely to creating intrinsically safer workspaces, particularly relevant in industries with strict safety regulations.
- Reduced Wiring Costs & Complexity: Lower voltages often allow for the use of smaller gauge wiring. This translates to lower material costs for conductors and simplified installation, especially in large-scale deployments where long cable runs are common. The potential for using less expensive, lighter, or more flexible cabling is a practical benefit.
- Energy Efficiency: Operating at lower voltages inherently implies potentially lower power consumption, especially when compared to higher voltage counterparts. While the savings per sensor might seem small, across hundreds or thousands of devices in a facility, the cumulative energy-saving impact can be substantial, aligning with sustainability goals.
- Compatibility with Modern Low-Voltage Systems: The rise of battery-powered devices, embedded systems, mobile robotics, IoT platforms, and PLC systems utilizing lower DC control voltages (like 5V, 12V, or 24V) demands compatible sensors. Low voltage photoelectric switches integrate seamlessly into these ecosystems without requiring bulky or costly step-down power supplies, simplifying design and reducing points of failure.
- Mitigation of Electromagnetic Interference (EMI): Lower voltage circuits can be less susceptible to generating problematic electrical noise and are sometimes easier to shield from interference. This contributes to cleaner signal transmission and more reliable operation in electrically noisy industrial environments.
- Ideal for Retrofits & Sensitive Environments: When upgrading older machinery or integrating sensors into environments where higher voltages pose unacceptable risks (e.g., laboratories, food processing near washdown areas, potentially explosive atmospheres requiring specific certifications), low voltage options provide a safe and compliant solution.
How They Work: Sensing Modes Explained
Low voltage photoelectric switches employ the same fundamental operating principles as their standard voltage counterparts:
- Through-Beam (Opposed Mode): Features separate emitter and receiver units facing each other. Detection occurs when the target object interrupts the light beam traveling from the emitter to the receiver. This mode offers the longest sensing ranges and highest reliability for object detection.
- Retroreflective: Uses a single unit housing both emitter and receiver, plus a reflector placed opposite. The emitter’s light beam is bounced off the reflector back to the receiver. Detection occurs when the target object blocks the beam’s path to the reflector. Offers good range and easier alignment than through-beam, needing only one wiring point.
- Diffuse (Proximity Mode): Combines emitter and receiver in one unit. The switch detects the target when it comes close enough that light reflected diffusely off the target surface reaches the receiver. The sensing range is shorter and depends heavily on the target’s color, size, and surface reflectivity. Ideal for applications requiring close detection without a separate reflector.
Selecting the Right Low Voltage Sensor: Key Considerations
Choosing the optimal low voltage photoelectric switch involves careful evaluation of your application:
- Operating Voltage Range: Precisely match the sensor to your system’s available DC voltage (e.g., 5V, 12V, 24V DC). Ensure compatibility with voltage tolerances.
- Sensing Range & Mode: Determine the required detection distance and select the appropriate mode (Through-Beam for long range/high reliability, Retroreflective for medium range/convenience, Diffuse for close proximity). Consider target characteristics.
- Output Type & Signal: Common outputs include NPN, PNP, or Push-Pull transistor types, and analog (e.g., 0-10V, 4-20mA). Ensure compatibility with the receiving device (PLC, controller).
- Environmental Factors: Evaluate ambient temperature, potential exposure to dust, water (IP Rating), chemicals, vibration, or mechanical impact. Choose sensors with suitable housing materials, ingress protection (IP67/IP69K for harsh environments), and ratings.
- Response Time & Switching Frequency: Critical for high-speed applications. Ensure the sensor’s response time meets the required cycle speed.
- Light Source: Infrared (common, invisible), Red LED (visible beam for easier alignment), or Laser (highly precise for small objects/long range). Infrared offers good resistance to ambient light interference.
- Special Features: Look for capabilities like Background Suppression (diffuse sensors ignoring objects beyond a set distance), Foreground Suppression (ignoring close objects), Precision Focusing, IO-Link connectivity for smart diagnostics and parameter setting, or sunlight immunity.
Versatile Applications Across Industries
The safety and compatibility advantages of low voltage photoelectric sensors make them ubiquitous:
- Packaging & Material Handling: Detecting cartons, bottles, cans on conveyors; monitoring fill levels; controlling diverters/gates; verifying label presence. Their reliability is key for high-speed production lines.
- Automotive Manufacturing: Part presence verification throughout assembly; robot safety guarding; end-of-arm tooling sensing; detecting components in paint shops or clean rooms.
- Food & Beverage Processing: Monitoring product flow on conveyors; detecting lids, labels, or caps; controlling filling valves; presence detection in washdown areas (requires appropriate IP69K ratings).
- Electronics Assembly: Verifying component insertion on PCBs; detecting tiny electronic parts; ensuring precise positioning during delicate assembly processes.
- Pharmaceutical Production: Object detection in sterile environments; ensuring proper vial/carton positioning; controlling feed mechanisms