inductive proximity switch sensor
- time:2025-07-12 01:52:41
- Click:0
The Essential Guide to Inductive Proximity Sensors: Principles and Applications
Imagine a device that can “see” metal objects through solid barriers without ever touching them. That’s the core magic of the inductive proximity switch sensor. These ubiquitous workhorses of industrial automation silently perform countless detection tasks, ensuring efficiency, safety, and precision in machines and processes worldwide. Far more than just simple switches, they offer a robust, non-contact solution for object detection in demanding environments.
Unveiling the Working Principle: Electromagnetism in Action
At the heart of every inductive proximity sensor lies a fundamental principle of physics: electromagnetic induction. Here’s a breakdown of how it operates:
- The Oscillator: Inside the sensor face, an oscillator circuit generates a constantly fluctuating high-frequency electromagnetic field. This field radiates outwards from the sensor’s active surface.
- Target Interaction: When a metallic object (the “target”) enters this electromagnetic field, tiny electrical currents called eddy currents are induced on the surface of the metal. This phenomenon occurs specifically with conductive materials, primarily metals.
- Field Disturbance: The formation of these eddy currents absorbs energy from the sensor’s oscillating electromagnetic field. This leads to a measurable reduction (damping) in the amplitude of the oscillation.
- Detection Circuit: The sensor’s internal circuitry continuously monitors the oscillator’s amplitude. When the damping effect (caused by the target) exceeds a predefined threshold, the detection circuit is triggered.
- Output Signal: Upon detection, the sensor switches its state. Most commonly, this means changing a solid-state output transistor (PNP, NPN, or Push-Pull) from “OFF” to “ON,” or vice-versa. This provides a clean, bounce-free electrical signal usable by PLCs (Programmable Logic Controllers), counters, or other control systems. Crucially, no physical contact occurs between the sensor and the target.
Why Choose Inductive Proximity Sensors? Key Advantages
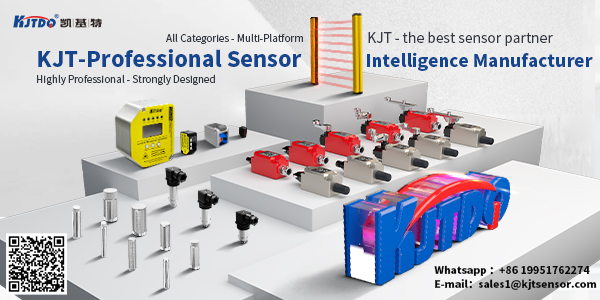
Their operating principle translates into several compelling benefits that make them indispensable:
- Non-Contact Sensing: The fundamental advantage. No moving parts touch the target, eliminating mechanical wear and tear. This translates to extremely long operational lifetimes and virtually maintenance-free operation.
- High Reliability & Speed: Solid-state electronics enable very fast response times (often microseconds), allowing detection of high-speed moving objects. They consistently deliver millions of switching cycles reliably.
- Robust Construction: Designed for harsh industrial settings. They feature sealed housings (with IP67, IP68, or IP69K ratings common), offering excellent resistance to dust, moisture, oils, coolants, and vibrations. Their resistance to electrical noise is also significant.
- Insensitive to Surface Conditions: Unlike optical sensors, they work reliably regardless of target surface dirt, grime, or color (as long as it’s conductive metal). Oil or dust buildup on the sensor face itself usually doesn’t impede function significantly.
- Simple Integration: Standardized cylindrical or block shapes, mounting threads, and connection methods (cable or connector) simplify installation. Output signals are typically compatible with industrial control voltages (10-30V DC).
Where They Shine: Industrial Applications Galore
The inductive proximity switch sensor finds application in virtually every sector involving machinery and automation:
- Position Sensing: Verifying the presence or absence of parts on conveyors, in fixtures, at end stops (end-of-stroke detection for cylinders), or within assemblies. Critical for sequencing operations.
- Object Counting: Counting metallic parts (bottlecaps, cans, machined components) as they pass by on a production line.
- Speed Monitoring: Detecting teeth on gears or sprockets to measure rotational or linear speed.
- Level Detection: Monitoring fill levels of metallic powders, pellets, or liquids within metal tanks (using sensors mounted externally to the tank wall).
- Machine Safety: Employed within safety circuits for gate/door monitoring (confirming a guard is closed) or detecting unsafe machine positions.
- Endless Automation Tasks: Tool breakage detection, sorting systems, robot end-effector position confirmation, packaging machinery part presence, and metal detection in non-metal processes.
Selecting the Right Sensor: Factors to Consider
Choosing the optimal inductive proximity sensor involves several parameters:
- Sensing Range (Sn): The nominal distance at which a standard target will reliably trigger the sensor. Always consult manufacturer datasheets. Remember, actual sensing distance (Sa) can vary slightly based on target material, size, and shape.
- Target Material: Standard sensors are optimized for mild steel. Different metals (stainless steel, aluminum, brass, copper) induce eddy currents differently. For non-ferrous metals, factor-of-reduction must be applied to the stated Sn (e.g., aluminum might have a factor of ~0.4, meaning effective range is 40% of Sn for steel). Specialized versions exist for detecting specific metals.
- Target Size: The target must generally be larger than or equal to the sensor face diameter to achieve the stated Sn. Smaller targets reduce the effective sensing distance.
- Housing Style & Size: Common options include threaded barrels (M5, M8, M12, M18, M30), block sensors, and rectangular formats. Choose based on mounting constraints and required sensing range.
- Output Configuration: PNP (sourcing), NPN (sinking), NO (Normally Open), NC (Normally Closed), Push-Pull (compatible with both). Must match the input requirements of the connected controller (PLC input card).
- Connection Type: Pre-wired cable (fixed or flexible), or quick-disconnect connectors (like M8 or M12).
- Environmental Rating: Verify the Ingress Protection (IP) rating (e.g., IP67, IP68, IP69K) is suitable for the environment (washdown, outdoor, dusty).
- Special Requirements: Consider flush-mount vs. non-flush mount capabilities (non-flush offer longer ranges but need lateral space), high-temperature versions, or models with advanced diagnostics (IO-Link).
The Future: Integration and Intelligence
While the core inductive principle remains constant, innovation continues. Integration of IO-Link communication is a major trend. This transforms the basic proximity sensor into a smart device capable of transmitting detailed diagnostic data (operating health, temperature, switching frequency), enabling remote parameter configuration, and providing more granular process information – all while maintaining the standard switching signal for backward compatibility. This enhances predictive maintenance and overall system intelligence.
Conclusion
From ensuring a robot arm grips its component to guaranteeing a safety door is latched, the inductive proximity switch sensor is a deceptively simple component performing essential, reliable detection tasks day in and day out. Its non-contact operation, rugged construction, and inherent reliability make it an irreplaceable element in the landscape of industrial automation. Understanding its principles and selection criteria empowers engineers and technicians to deploy these sensors effectively, building more robust, efficient, and safer automated systems. As connectivity advances, these fundamental sensors continue to evolve, offering even greater value on the factory floor.