ift200 proximity sensor
- time:2025-07-12 01:45:40
- Click:0
Decoding IFT200 Proximity Sensors: Precision Detection for Demanding Automation
Imagine a high-speed bottling line screeching to a sudden halt. Thousands of dollars in lost production per minute. Often, the culprit is deceptively simple: a failed sensor. In the relentless world of industrial automation, where milliseconds and microns matter, reliability is non-negotiable. This is precisely where components like the IFT200 proximity sensor series step into the spotlight. Designed for robustness and unwavering accuracy, these sensors are fundamental building blocks in countless machines, ensuring seamless operation by reliably detecting the presence or absence of metallic objects without physical contact.
What Are IFT200 Proximity Sensors?
Belonging to the broad category of inductive proximity sensors, the IFT200 series operates on a fundamental electromagnetic principle. They generate a high-frequency oscillating electromagnetic field from their active sensing face. When a metallic target (like steel, aluminum, brass, etc.) enters this field, it induces tiny eddy currents within the metal. These currents absorb energy from the sensor’s oscillating field, causing a detectable change – typically a reduction in the oscillation amplitude. The sensor’s integrated electronics detect this change and consequently switch its output signal. This solid-state switching, devoid of any moving parts contacting the target, is the essence of their remarkable durability and long service life.
Why the IFT200 Series Stands Out in Automation
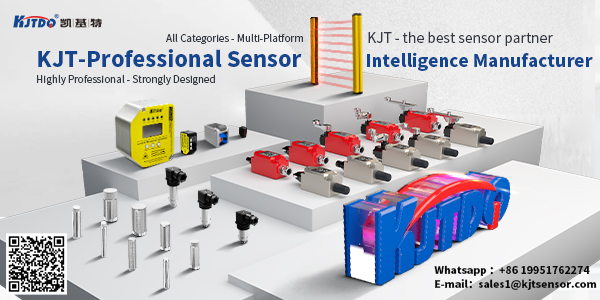
The IFT200 designation typically signifies a specific range of inductive sensors known for their standardized cylindrical form factor (often M12, M18, or M30 threading) and consistent performance characteristics vital for industrial settings:
- Reliable Detection Range: Engineered for specific sensing distances (e.g., 2mm, 4mm, 8mm depending on model and size), IFT200 sensors offer dependable performance within their rated specifications. Think of it as their guaranteed zone for consistent target detection. Fluctuations due to temperature or voltage are minimized.
- Exceptional Durability: Built to endure the harsh realities of factories and plants, IFT200 sensors commonly boast high ingress protection ratings (like IP67 or IP69K). This means they are highly resistant to dust intrusion and powerful water jets, making them suitable for washdown environments or dusty workshops. Their housings are typically crafted from robust materials like nickel-plated brass or stainless steel, offering excellent resistance to impacts, vibration, and many chemicals.
- Output Flexibility: To interface seamlessly with various control systems (PLCs, relays, etc.), IFT200 sensors are available with different output configurations. Common options include:
- NPN (Sinking): The output switches the negative (0V) line.
- PNP (Sourcing): The output switches the positive (+V) line.
- NO (Normally Open) / NC (Normally Closed): Defines the output state without a target present.
- Electrical Robustness: These sensors incorporate vital protection features like short-circuit protection, reverse polarity protection, and surge suppression. This safeguards the sensor and connected equipment from common wiring errors or electrical noise spikes prevalent on industrial power lines, significantly reducing downtime.
- Harsh Environment Resilience: Beyond physical protection, IFT200 sensors are designed to perform reliably across a wide operating temperature range (often -25°C to +70°C or wider) and withstand electromagnetic interference (EMC) common in electrically noisy industrial environments.
- Easy Installation & Integration: The standardized cylindrical M-series threaded barrel design allows for quick and simple mounting using standard locknuts. Models are frequently available in flush-mountable or non-flush (shielded) variants, providing flexibility depending on mounting constraints and required sensing range. Features like an integrated LED status indicator provide immediate visual feedback on the sensor’s operational state (power, target detection), simplifying setup and troubleshooting.
Key Applications: Where IFT200 Sensors Shine
The combination of non-contact operation, resilience, and precision makes the IFT200 proximity sensor incredibly versatile across countless industrial segments:
- Position Verification: Confirming cylinders are extended/retracted, detecting pallet presence on conveyors, verifying parts are correctly seated in fixtures or nests. Critical for process sequencing.
- Object Counting: Accurately tallying bottles, cans, packages, or components moving past a point on a conveyor line.
- Speed Monitoring: Detecting the teeth of a gear or marks on a rotating shaft to calculate rotational speed.
- End-of-Travel Detection: Safely signaling when a moving part (like a robotic arm or machine guard) has reached its limit position.
- Level Control: Detecting the presence/absence of metal parts in bins or hoppers (often used in conjunction with other technologies for non-metallic materials).
- Machine Safety: Contributing to simple safety interlocks (e.g., confirming a guard door is securely closed before machine start-up).
OPTICAL Models: Expanding Capabilities
It’s crucial to note that the designation “IFT200” can sometimes encompass related sensor types within a manufacturer’s catalog. Particularly common are IFT200 OPTICAL sensors. These are fundamentally different from the inductive IFT200s:
- Operating Principle: IFT200 Optical sensors utilize light (usually infrared - IR) instead of an electromagnetic field. They work by emitting a light beam and detecting either its reflection from a target (diffuse reflective), the interruption of a beam sent to a separate receiver (through-beam), or the reflection off a specific reflector (retro-reflective).
- Target Material: Unlike inductive sensors, optical sensors can detect virtually any object regardless of material – plastic, wood, glass, liquid, cardboard, as well as metal. This makes the IFT200 OPTICAL variant indispensable for applications where non-metallic objects need detection.
- Range: Optical sensors generally offer significantly longer sensing ranges compared to inductive sensors of similar size.
Choosing the Right Tool: Inductive vs. Optical IFT200
Selecting between an inductive IFT200 and an IFT200 OPTICAL sensor boils down to the application:
- Use Inductive (Standard IFT200): When your primary target is metal and you need a sensor highly resilient to environmental contaminants like dust, dirt, or splashing liquids/oils. Ideal for heavy industrial metal detection.
- Use Optical (IFT200 OPTICAL): When you need to detect non-metallic objects (plastic, bottles, labels, people, etc.), require longer detection ranges, or need precision detection regardless of surface color (though some diffuse sensors can be color-sensitive). Essential for packaging, material handling, and diverse object detection.
Conclusion: The Unsung Heroes of Automation Precision
Whether it’s the core electromagnetic reliability of the standard inductive IFT200 sensor or the versatile object detection capability of the IFT200 OPTICAL, this family represents a cornerstone of modern industrial sensing. Their robustness, ease of integration, and dependable performance in challenging environments make them a go-to solution for engineers designing machinery that demands precision and uptime. By mastering the detection of metal or diverse materials, these compact devices silently orchestrate complex automated processes, ensuring efficiency, safety, and productivity across a vast spectrum of industries—from the relentless pace of automotive assembly to the meticulous demands of pharmaceutical packaging. When you need a sensor that consistently delivers under pressure, the IFT200 series provides a proven, industry-standard answer. A robotic arm seamlessly places components onto a rapidly moving conveyor; milliseconds later, an IFT200 inductive sensor confirms the part is present and correctly oriented, signaling the next station to begin its precision welding operation.