inductive pick up sensor
- time:2025-07-10 01:17:20
- Click:0
Unlocking the Power of Non-Contact Sensing: A Deep Dive into Inductive Pickup Sensors
Inductive Pickup Sensors: The Invisible Workhorses of Precision Detection and Automation
Imagine a factory floor humming with activity. Robotic arms move with blinding speed, assembly lines glide seamlessly, and intricate components are positioned with micron-level accuracy. Amidst this orchestrated precision, one critical element often goes unseen: sensors ensuring everything is exactly where it needs to be. Among the most reliable and ubiquitous are inductive proximity sensors, also commonly referred to as inductive pick-up sensors. These unsung heroes provide robust, non-contact detection, forming the bedrock of countless automated processes. What makes them so vital, and how do they achieve such dependable performance?
The Core Principle: Electromagnetism in Action
At its heart, an inductive pickup sensor is a marvel of applied physics, leveraging the fundamental principles of electromagnetic induction discovered by Michael Faraday. The core component is a coil of wire wound around a ferrite core within the sensor’s active face. When energized, an oscillator circuit generates a high-frequency alternating current (AC) through this coil.
This oscillating current creates a dynamic, high-frequency electromagnetic field radiating outwards from the sensor’s face. Crucially, this field remains confined to a relatively small area directly in front of the sensor – its sensing range.
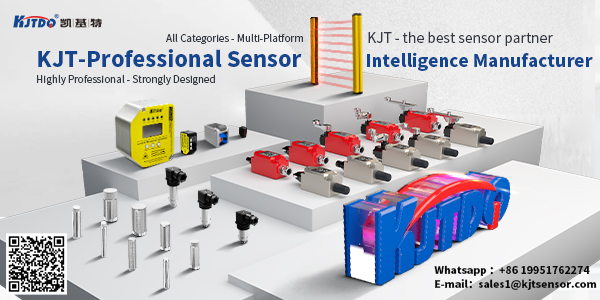
Here’s where the magic happens:
- Absence of Target: When no electrically conductive material is present within this electromagnetic field, the oscillator maintains a stable amplitude. The internal circuitry interprets this as “no target detected.”
- Presence of a Target: When a metal target (ferrous metals like iron and steel are most effective, but non-ferrous metals like aluminum, brass, or copper also work, albeit typically at shorter ranges) enters the electromagnetic field, eddy currents are induced on the surface of the target.
- Energy Absorption & Damping: These eddy currents consume energy from the sensor’s oscillating field, effectively damping the oscillation. This causes a measurable decrease in the amplitude of the AC signal within the coil.
- Signal Processing & Output: The sensor’s sophisticated internal electronics detect this change in amplitude. Once the damping exceeds a predefined threshold, the sensor triggers its output state – switching from “off” to “on” (or vice-versa, depending on its configuration – Normally Open/NO or Normally Closed/NC). This output signal is then used by controllers like PLCs to make logical decisions within the automated system.
Why Inductive Pickup Sensors Reign Supreme: Key Advantages
Their widespread adoption across demanding industrial environments isn’t accidental. Inductive sensors offer a compelling set of benefits:
- Non-Contact Operation: This is arguably their most significant advantage. Physical contact with the target is unnecessary. This eliminates mechanical wear and tear, drastically extending sensor lifespan and reducing maintenance costs. Targets can be detected through non-conductive materials like plastic, wood, or paint, offering design flexibility.
- Exceptional Reliability & Long Service Life: With no moving parts subject to friction and built with rugged housings (typically Nickel-plated brass or stainless steel), these sensors shrug off dust, dirt, oil, and coolant splashes. They are engineered for continuous operation in the harshest industrial settings.
- High Switching Frequency & Speed: Modern inductive sensors boast incredibly fast response times, often in the microsecond range. This allows them to reliably detect targets moving at very high speeds or vibrating rapidly, making them ideal for high-throughput production lines.
- Immunity to Environmental Factors: Unlike optical sensors, they are completely unaffected by ambient light conditions, smoke, steam, or opaque fluids (provided they aren’t conductive liquids encroaching on the sensor face). This makes them incredibly versatile and robust.
- Maintenance-Free Operation: Once installed and correctly configured, inductive sensors typically require zero maintenance throughout their operational life. Their sealed construction protects the internal electronics.
- Cost-Effectiveness: Offering a powerful combination of reliability, longevity, and performance, they provide excellent value for money, especially considering their minimal maintenance requirements.
Ubiquitous Applications: Where You’ll Find Them Working
The unique strengths of inductive proximity sensors make them indispensable in countless scenarios:
- Position Detection: Verifying the presence/absence or end position of machine parts, cylinders (piston position), clamps, slides, and doors.
- Object Counting: Counting metallic objects on conveyors (cans, machined parts, bottles with metal caps).
- Speed Monitoring: Detecting rotating shafts, gears, or sprockets for simple tachometry or overspeed/underspeed detection.
- Material Handling: Confirming part presence in fixtures, grippers, pallets, or assembly stations. Detecting metal slugs or jams.
- Machine Safety: Acting as part of interlock systems on guards and doors.
- Automotive Manufacturing: Used extensively on assembly lines for engine block positioning, door panel welding, wheel hub detection, and fluid level sensing (using metal floats).
- Packaging Machinery: Detecting foil seals, metal lids, capping machines, and conveyor synchronization.
- Metalworking: Tool breakage detection on CNC machines, monitoring spindle position, and part-in-place verification.
Selecting the Right Inductive Sensor: Key Considerations
Choosing the optimal sensor requires attention to several factors:
- Sensing Distance: Specified by the sensor manufacturer as the “nominal sensing distance” (
Sn
). Factors affecting the actual working distance include target size, shape, material type (ferrous vs. non-ferrous), and mounting conditions. Always ensure the target meets the sensor’s requirements – a smaller target requires a proportionally smaller sensor for reliable detection. Maintain an installation gap between sensors to prevent mutual interference.
- Target Material: Ferrous metals (iron, steel) offer the longest sensing ranges. Non-ferrous metals (aluminum, copper, brass) significantly reduce the range (often 30-60% of
Sn
). Always refer to the sensor datasheet for specific reduction factors.
- Sensor Housing & Form Factor: Choices range from tubular threaded barrels (M8, M12, M18, M30) to block or rectangular styles. Selection depends on available space and mounting requirements.
- Output Configuration: Standard options are NPN (sinking) or PNP (sourcing) transistor outputs, typically 3-wire DC sensors. Also, consider voltage levels (10-30V DC is common) and whether you need Normally Open (NO) or Normally Closed (NC) logic. Heavy-duty AC sensors and specialized analog versions (providing continuous distance measurement) are also available.
- IP Rating (Ingress Protection): Critical for the environment. IP67 & IP68 ratings are common for wash-down areas or outdoor use, ensuring protection against dust and water immersion. IP69K offers high-pressure, high-temperature wash-down resistance.
- High-Temperature Options: Standard sensors typically operate up to 70-80°C. Specialized high-temperature sensors are available for environments like foundries or ovens.
The Future is Sensing: Innovation Continues
While the core electromagnetic principle remains constant, inductive sensor technology continues to evolve. Manufacturers are constantly pushing boundaries:
- Miniaturization: Smaller sensors (M3, M4, M5 threads) enabling detection in incredibly compact spaces.
- Increased Sensing Distances: Offering greater flexibility in mounting.
- Enhanced Immunity: Improved resistance to electromagnetic interference (EMI) and welding fields.
- IO-Link Integration: Smart sensors transmitting configuration data, process values, and diagnostic information over a standard communication line, paving the way for predictive maintenance and seamless integration into Industry 4.0 and smart factory ecosystems. Analog variants provide proportional distance feedback