inductive proximity sensor detects
- time:2025-07-10 01:24:16
- Click:0
How Inductive Proximity Sensors Detect Metallic Objects Without Contact
In the precise world of industrial automation and machinery, reliably “knowing” where things are is fundamental. Whether it’s counting components on a high-speed assembly line, confirming a robotic arm’s position, or ensuring a safety door is closed, detection is key. Among the most robust and widely trusted solutions for sensing metal objects precisely and without touching them is the inductive proximity sensor. This article delves into exactly how an inductive proximity sensor detects its target, exploring its core principles, capabilities, and critical advantages.
The Core Principle: Harnessing Electromagnetic Fields
At the heart of an inductive proximity sensor lies a fascinating application of physics. It operates on the principle of electromagnetic induction, specifically Faraday’s Law of Induction. Here’s the breakdown:
- Generating the Field: Inside the sensor’s active face (sensing surface), a copper coil wound around a ferrite core generates a high-frequency alternating electromagnetic field when energized.
- Field Interaction: This oscillating magnetic field extends a short distance from the sensor face into the surrounding space. It’s invisible and requires no physical medium to propagate.
- Target Presence: When a conductive metal target (steel, aluminum, brass, copper, etc.) enters this field, it disrupts it.
- Eddy Current Magic: The changing magnetic field induces swirling electrical currents within the conductive metal target. These are called eddy currents.
- Energy Absorption: The creation of these eddy currents consumes energy from the sensor’s oscillating circuit. This energy loss is directly proportional to the distance of the target from the sensor face.
- Sensing the Change: The sensor’s internal electronics continuously monitor the energy level in its oscillator circuit. The reduction in energy caused by the eddy currents (when a target is present) triggers a state change in the sensor’s output circuit.
- Output Signal: This state change results in the sensor detecting the target and sending an electrical signal (typically switching ON or OFF a load, like a PLC input, relay, or light).
Key Capabilities: What Does It Detect?
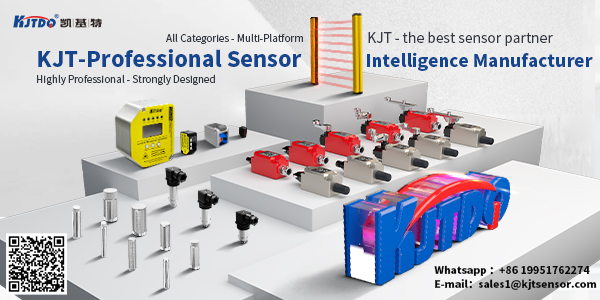
Understanding the detection mechanism clarifies the core capabilities and inherent limitations:
- Non-Contact: Detection occurs without any physical touch. This eliminates wear and tear on both the sensor and the target, crucial for high-cycle applications.
- Metallic Targets: Inductive sensors are specifically designed to detect ferrous metals (containing iron, like steel) and non-ferrous metals (like aluminum, copper, brass). The sensor’s sensitivity and effective sensing distance (Point of Operation/Repeatability - PoR) vary depending on the target material.
- Material Sensitivity: Targets significantly impact performance.
- Ferrous Targets (Steel): Generally offer the longest sensing distances because they are both conductive and magnetic (enhancing the field interaction).
- Non-Ferrous Targets (Aluminum, Brass, Copper): Provide shorter sensing distances compared to steel due to lower magnetic permeability, though they are still readily detectable. Sensor specifications often list a “rated operating distance” (Sn) for a standard steel target (e.g., Fe360). Sensing distance for other materials is usually a percentage of Sn (e.g., aluminum might be ~40% of Sn).
- Insensitivity to Non-Metals: Crucially, inductive proximity sensors do not detect non-metallic materials like plastic, wood, liquids, glass, or paper. This makes them ideal for environments where only the presence of metal needs to be confirmed, ignoring other substances. They effectively “see” only metal.
- Proximity, Not Distance: While some specialized types exist, the vast majority of standard inductive sensors are binary proximity switches. They reliably indicate the presence or absence of a metallic target within their specified sensing range (e.g., 2mm, 5mm, 8mm, 15mm), but do not provide a continuous analog distance measurement.
Why Detection Without Contact Matters: The Advantages
The non-contact nature of inductive detection delivers compelling benefits that make them indispensable in demanding environments:
- Exceptional Reliability & Longevity: Without moving parts making physical contact, there’s minimal mechanical wear. Sensors can endure millions of operating cycles, ensuring stable, long-term operation and reduced maintenance costs.
- High-Speed Operation: Detection and switching happen incredibly fast – typically in microseconds. This makes them perfect for high-speed counting, positioning verification, and capturing rapid events on production lines.
- Resilience in Harsh Environments: Robust construction techniques include:
- Potting: Encapsulating internal electronics in resin protects against shock and vibration.
- High IP Ratings: Sealed housings (e.g., IP67, IP68, IP69K) guard against dust ingress and high-pressure water jets.
- Chemical Resistance: Stainless steel or specialized plastic housings withstand oils, coolants, and cleaning agents.
- Avoidance of Misalignment: Unlike mechanical switches, slight target position shifts within the field generally don’t cause false triggers or failures.
- Simplified Installation & Operation: Available in diverse shapes (cylindrical, block), sizes, and connection types, they are relatively easy to integrate. Output signals (PNP, NPN, NO, NC) are standardized for compatibility with control systems like PLCs.
Broad Applications: Where Detection Drives Efficiency
The reliable detection capability of inductive sensors makes them ubiquitous across countless industries:
- Factory Automation: Position sensing of cylinders, end-of-stroke detection, part presence/absence confirmation on conveyors, machine guarding, robotic arm positioning, and high-speed part counting.
- Automotive Manufacturing: Detecting metal components during assembly, verifying fixture positions, monitoring robotic welders, and controlling paint line processes.
- Packaging & Material Handling: Confirming the presence of metal lids, cans, or foil seals; detecting metal parts in bins (level control); verifying the position of metal guides or gates.
- Food & Beverage Processing: Position control in stainless steel machinery, detecting metal cans or foil lids on filling lines (using hygienic stainless steel sensors with high IP ratings).
- Machine Tools: Tool position sensing, chuck clamping confirmation, workpiece presence detection in lathes or mills, and coolant level monitoring (using specialized sensors).
- Conveyor Systems: Object counting, jam detection (if metal components are involved), position verification of diverters or stoppers.
Optimizing Detection: Factors to Consider
To ensure an inductive proximity sensor detects reliably in your application, consider these points:
- Target Material & Size: Determine the target metal. Remember, sensing distance varies significantly between ferrous and non-ferrous metals. The target size must also be large enough to adequately interact with the sensor’s field. Small targets require sensors designed for narrower fields or shorter ranges.
- Required Sensing Distance (Sn): Choose a sensor with a rated operating distance slightly greater than your actual mounting distance, providing a buffer zone for reliable triggering.
- Mounting & Environment: Ensure correct installation (flush or non-flush mounting options exist) and account for nearby metal structures (“install metal”) which can reduce the effective sensing range. Select the appropriate housing material and sealing (IP rating) for the ambient conditions (temperature, chemicals, washdowns).
- Output Type & Wiring: Match the sensor’s output configuration (PNP/NPN, Normally Open/Normally Closed) and voltage requirements to your control system input.
Troubleshooting Detection Issues
If an inductive sensor fails to detect properly, common causes include:
- Incorrect Mounting Distance: Target is outside the sensor’s effective range.
- Unsuitable Target: Attempting to detect a non-met