24 volt proximity sensor
- time:2025-07-07 13:38:46
- Click:0
The Unsung Hero of the Factory Floor: Your Guide to 24 Volt Proximity Sensors
In the rhythmic heartbeat of modern manufacturing, automation reigns supreme. Machines move with precision, assembly lines flow seamlessly, and processes hum with efficiency. But beneath this orchestrated symphony lies a network of silent sentinels – sensors. Among these, the 24 Volt DC proximity sensor stands as a cornerstone, a workhorse so ubiquitous it often goes unnoticed, yet it’s absolutely critical for countless operations. Understanding its function, why 24V DC is the industrial standard, and how to leverage its capabilities is key to unlocking reliable and safe automation.
So, what exactly is a proximity sensor? In simple terms, it’s a device that detects the presence or absence of an object without physical contact. Think of it as an electronic eye or feeler that “senses” something nearby. 24 volt proximity sensors specifically operate on a 24 Volt Direct Current power supply, making them the dominant choice in industrial control systems worldwide.
Why 24 Volts DC? The Industrial Sweet Spot
The prevalence of 24V DC sensors isn’t accidental; it’s the result of deliberate engineering choices prioritizing safety, compatibility, and reliability:
- Enhanced Safety: Compared to higher voltage AC systems (like 120V or 240V AC), 24V DC presents a significantly lower risk of severe electrical shock. This intrinsic safety is paramount in environments where personnel interact with machinery, maintenance is routine, and potential contact with wiring exists. It minimizes hazards and simplifies safety protocols.
- Compatibility with PLCs and Controls: Modern Programmable Logic Controllers (PLCs), the brains of automation systems, overwhelmingly use 24V DC for their input and output (I/O) circuits. A 24 volt proximity sensor integrates seamlessly, providing the signal level PLCs expect without the need for cumbersome voltage converters or relays (though relays are still often used for load handling).
- Reduced Electrical Noise Susceptibility: DC signals are generally less susceptible to interference from electromagnetic noise (EMI) generated by motors, welders, and other industrial equipment than AC signals. This translates to more reliable switching and fewer false triggers, crucial for maintaining process integrity.
- Wiring Simplicity and Cost: Lower voltage systems often allow for lighter gauge wiring and simpler installation compared to higher voltage AC systems, offering potential cost savings on materials and labor. Standardization around 24V DC also streamlines component sourcing and system design.
How Does a 24V Proximity Sensor Work? Unpacking the Magic (Mostly Inductive)
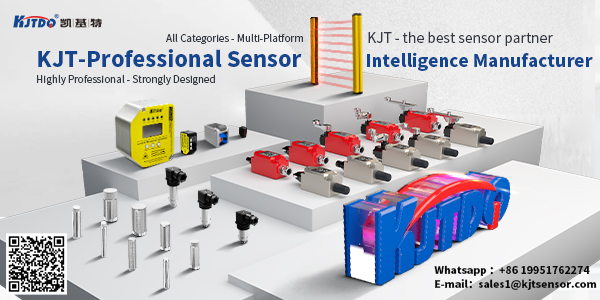
While several technologies fall under the “proximity” umbrella (capacitive, ultrasonic, photoelectric), the term “24 volt proximity sensor” most commonly refers to the inductive proximity sensor. Let’s focus on that workhorse:
- The Core Principle: An inductive proximity sensor generates an oscillating electromagnetic field from its sensing face using a coil.
- Detection: When a metal object (the “target”) enters this field, it induces eddy currents within the metal.
- Signal Change: These eddy currents draw energy from the sensor’s oscillator circuit, causing a detectable change in its oscillation amplitude.
- Output Switching: The sensor’s internal circuitry detects this change and triggers its solid-state output switch. For a 24 volt proximity sensor, this output will either connect (“switch on”) or disconnect (“switch off”) the 24V DC circuit it’s wired into, signaling the PLC or controller that an object is present.
Key Types Within the 24V Family: Beyond Inductive
While inductive dominates, it’s important to recognize other types powered by 24V DC that solve different detection challenges:
- Inductive Proximity Sensors: As described, detect metal objects (ferrous metals like iron/steel generally at greater distances than non-ferrous like aluminum or brass). Highly robust, immune to dust, oil, and moisture.
- Capacitive Proximity Sensors: Detect the presence of any material (metal, plastic, wood, liquid, granules) by sensing changes in capacitance. Ideal for detecting fill levels in non-metallic containers, presence of powders, or objects through thin barriers.
- Photoelectric Sensors: Use light (visible, infrared, laser) to detect objects. While technically “contactless,” they are often categorized separately, but many run on 24V DC. Excellent for longer ranges and detecting non-metals.
- Magnetic Proximity Sensors (Reed Switches): Detect the presence of a magnetic field, typically from a magnet attached to a moving part. Simple, reliable, and also commonly 24V DC.
The Compelling Advantages of Using 24V Proximity Sensors
Choosing a 24 volt proximity sensor offers a compelling list of benefits perfectly suited for the industrial environment:
- Non-Contact Sensing: Eliminates wear and tear on both the sensor and the target, leading to long operational life and reduced maintenance costs. No physical impact!
- High Reliability & Speed: Solid-state electronics mean fast switching speeds (often kHz range) and millions of cycles with no mechanical degradation. Perfect for high-speed counting or positioning.
- Robustness: Sealed housings (IP67, IP68 ratings are common) make them resistant to dust, dirt, oils, coolants, and vibrations – essential in harsh factory conditions.
- Output Flexibility: Available in various output configurations:
- NPN (Sinking): Switches the negative (0V) line.
- PNP (Sourcing): Switches the positive (24V) line. Crucial to match sensor output type with PLC input requirements.
- NO (Normally Open) / NC (Normally Closed): Defines the “resting state” logic. NO closes on detection; NC opens on detection.
- Simple Integration: The standardized 24V DC supply and output logic make them easy to wire and interface with control systems like PLCs.
Selecting the Right 24 Volt Sensor: Key Considerations
Choosing the best 24 volt proximity sensor requires attention to several factors:
- Target Material: Metal? Inductive is king. Plastic, liquid, wood, etc.? Capacitive is needed. If using Inductive, is the target ferrous or non-ferrous? (Affects sensing distance).
- Required Sensing Distance: How far away should the sensor detect the object? Inductive sensors have a rated operating distance (Sn) – choose one that provides sufficient clearance and mounting flexibility for your application. Never mount flush at the maximum Sn distance; allow margin.
- Output Type (NPN vs. PNP & NO vs. NC): This is critical. Match the output type (NPN sinking or PNP sourcing) to your controller’s input card specifications. Choose NO/NC based on the desired logic (e.g., NO = signal when object present).
- Housing Size and Shape: Cylindrical (threaded barrel) or rectangular block? Size constraints in the mounting location dictate this.
- Environmental Factors: What is the ambient temperature? Exposure to chemicals, oils, or high-pressure washdown? Look for appropriate IP ratings (Ingress Protection) and material construction (e.g., stainless steel).
- Switching Speed: For very high-speed applications, ensure the sensor’s response frequency meets or exceeds the requirements.
The Indispensable Component
The 24 volt proximity sensor is far