analog proximity sensor 4 20ma
- time:2025-07-07 13:45:46
- Click:0
The Unbreakable Signal: Why Analog Proximity Sensors with 4-20mA Output Rule Industry
In the gritty heart of industrial automation – amidst flying metal chips, grinding gears, and electrical interference – sensing reliability isn’t just desirable; it’s non-negotiable. When milliseconds matter and machine survival depends on accurate detection, a fragile signal simply won’t cut it. This is where the analog proximity sensor 4-20mA shines, embodying decades of proven resilience. Far more than just an on/off switch, this sensor delivers continuous, robust distance information vital for process control, safety, and efficiency.
Understanding the Core: Analog Proximity Sensing
Unlike its digital cousin that merely signals “object present” or “object absent,” an analog inductive proximity sensor provides a continuous output signal proportional to the distance between its active face and the target metal object. As a conductive target approaches, it induces eddy currents within the sensor’s coil. These currents change the oscillation amplitude of the sensor’s internal circuit. Sophisticated electronics within the sensor convert this amplitude change into a smooth, linear electrical signal – the foundation of the 4-20mA output.
The 4-20mA Standard: Engineered for Resilience
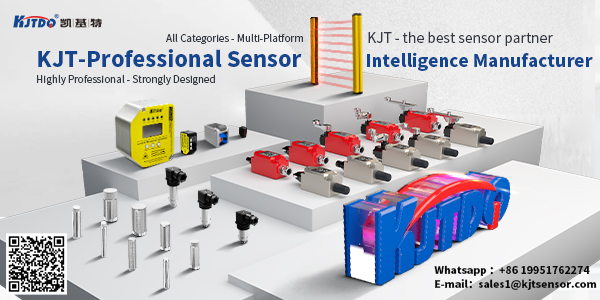
So, why 4-20mA specifically? This current loop standard, established decades ago, solves critical challenges inherent to industrial environments:
- Noise Immunity: Current signals are inherently less susceptible to electromagnetic interference (EMI) and voltage drops over long cable runs than voltage signals (like 0-10V). Electrical noise typically induces voltage fluctuations, which minimally affect a current-driven signal. This translates to superior signal integrity in electromagnetically hostile factories.
- Live-Zero Detection: The “live zero” at 4mA is revolutionary. A traditional 0-20mA system couldn’t distinguish between “zero signal” (0mA) and a broken wire or dead sensor (also 0mA). With 4-20mA:
4mA
typically represents the maximum sensing distance or the “no target” state.
20mA
represents the minimum sensing distance or “target very close”.
- Critically, a signal falling below 3.6mA or 3.9mA (often defined per NAMUR NE43) signals a critical fault – a broken wire, sensor failure, or loss of loop power. This “below range” detection (Broken Wire Detection) is crucial for safety and predictive maintenance. A 0mA reading now definitively means a catastrophic failure in the loop.
- Two-Wire Simplicity & Loop Power: 4-20mA sensors are predominantly two-wire devices. They receive their operating power and transmit the signal over the same two wires. This significantly simplifies installation, reduces wiring costs, and minimizes connection points prone to failure. The loop power supply (typically 15-30V DC) provides the necessary energy.
- Standardization: The 4-20mA standard is globally recognized and understood across PLCs (Programmable Logic Controllers), DCSs (Distributed Control Systems), and display instrumentation. This universal language simplifies integration and troubleshooting.
Where Analog Proximity Sensors 4-20mA Excel
The unique strengths of this combination make it indispensable in demanding applications:
- Position Monitoring & Control: Providing continuous feedback on cylinder rod position, valve stem travel, or roll gap settings for precise closed-loop control.
- Fill Level Detection (Bulk Solids & Liquids): Monitoring material levels in bins, tanks, or hoppers where continuous level indication is more valuable than a simple high/low switch.
- Thickness & Runout Measurement: Gauging material thickness variations or detecting shaft eccentricity based on precise distance changes.
- Vibration Monitoring: Detecting relative movement or vibration amplitude on rotating machinery components.
- Harsh Environments: Environments saturated with oil, coolant, dust, moisture, or strong EMI/RFI interference, where digital signals struggle. Their robust construction adds to this resilience.
- Intrinsically Safe (IS) Applications: The simple, low-energy nature of 4-20mA loops is fundamental for designing intrinsically safe systems required in hazardous areas (oil & gas, chemical plants, mining). Meeting IS standards (like ATEX, IECEx) is significantly more feasible.
Advantages Over Digital & Voltage Analog Sensors
While digital PNP/NPN sensors are perfect for discrete tasks, and 0-10V sensors have niche uses, the analog proximity sensor 4-20mA offers distinct benefits:
- Superior Noise Immunity: Beats 0-10V hands-down for long distances and noisy environments.
- Inherent Fault Detection: The live zero provides diagnostics unavailable to 0-10V sensors and basic digital sensors.
- Simpler Wiring: Two wires handle everything (power and signal), unlike three/four-wire digital sensors or three-wire 0-10V sensors. This reduces complexity and potential points of failure.
- Long-Distance Transmission: Signals can reliably travel hundreds or even thousands of meters without significant degradation or susceptibility to voltage drop.
- Wider Compatibility: Direct interface with nearly any industrial controller or chart recorder built in the last 40+ years.
Choosing and Implementing Effectively
Selecting the right analog proximity sensor 4-20mA requires attention to:
- Sensing Range: Ensure the specified range meets your application’s distance requirements.
- Target Material: Inductive sensors detect metals; factor in the target’s material type (steel, aluminum, brass) and size as they significantly affect the effective sensing range.
- Environment: Consider IP rating (dust/water ingress protection), temperature range, chemical resistance, and potential mechanical impacts.
- Output Characteristics: Ensure the sensor provides a linear 4-20mA output proportional to distance within its specified range. Check datasheet linearity graphs.
- Loop Power Supply: Verify compatibility with your supply voltage (e.g., 24V DC nominal) and that the supply can deliver sufficient current (at least 20mA per sensor, often more during startup). Always include the necessary load resistor at the controller input.
Conclusion: The Enduring Workhorse
Even in the age of digital communication and IIoT, the analog proximity sensor 4-20mA remains a cornerstone of industrial automation. Its unparalleled combination of ruggedness, simplicity, inherent diagnostics, noise immunity, and long-distance capability make it the go-to solution for critical, continuous distance measurement tasks in challenging environments. When unbreakable signal integrity is the mandate, the 4-20mA current loop delivered by a robust analog proximity sensor continues to be the gold standard.