schneider inductive sensor
- time:2025-07-07 13:52:50
- Click:0
Schneider Inductive Sensors: The Unseen Pillars of Reliable Industrial Automation
Imagine a complex assembly line humming with activity – robots welding car frames, conveyor belts shuttling packages, machinery stamping out components. Amidst this controlled chaos, countless critical decisions happen in the blink of an eye, decisions that rely on knowing the precise position, presence, or absence of a metal object. This vital, often unnoticed, role is frequently filled by the unsung heroes of automation: Schneider Electric inductive sensors. More than just simple switches, these robust devices form the bedrock of reliable object detection in demanding industrial environments.
But first, what exactly is an inductive sensor? At its core, it’s a non-contact proximity sensor specifically designed to detect the presence of metallic objects. It works on the principle of electromagnetic induction. The sensor generates an oscillating electromagnetic field from a coil. When a metal target enters this field, it induces eddy currents within the metal, causing a measurable change in the sensor’s own oscillation. This change is detected by the sensor’s circuitry, which then triggers an output signal – essentially acting as a switch without physical contact. This non-contact nature is key to their durability and longevity, avoiding wear and tear associated with mechanical limit switches.
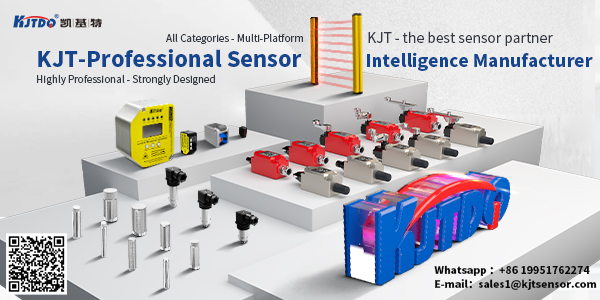
So, why choose Schneider Electric for such a fundamental component? Schneider doesn’t just manufacture sensors; they engineer solutions tailored for the realities of industrial life. Schneider inductive proximity sensors stand out due to several critical design philosophies:
- Ruggedness Built to Last: Industrial environments are tough. Dust, moisture, oil, vibration, and even high-pressure washdowns are everyday hazards. Schneider sensors are renowned for their exceptional robust construction. Featuring high-grade materials like stainless steel or nickel-plated brass housings and often boasting impressive IP67, IP68, and even IP69K protection ratings, they shrug off harsh conditions that would cripple lesser components. This inherent toughness translates directly into reduced downtime and lower maintenance costs.
- Unwavering Reliability & Repeat Accuracy: In automation, consistency is king. Schneider sensors deliver highly repeatable switching points, ensuring that a target is detected at precisely the same distance every single cycle, critical for precision applications. Combined with their inherent resistance to environmental factors like dirt and grime (which can blind optical sensors), this delivers unparalleled operational reliability. You can depend on them to perform, shift after shift.
- Advanced Sensing Technology: Schneider integrates sophisticated electronics within these compact devices. Features like embedded diagnostics (often signaled by a status LED), short-circuit and overload protection, and resistance to electromagnetic interference (EMI) ensure stable performance even in electrically noisy plant environments. Models are available with various sensing ranges, enabling selection based on specific application needs.
- Seamless Integration & Versatility: Schneider understands that sensors need to fit within complex control architectures. Their extensive range of inductive sensors comes with various electrical outputs (like NPN, PNP, Normally Open (NO), Normally Closed (NC), Analog) and connection methods (cable, M8, M12 connectors), ensuring compatibility with virtually any PLC (Programmable Logic Controller) or control system. This simplifies design and installation significantly.
- Form Factors for Every Need: From the ultra-compact XS series designed for space-constrained applications to the robust XU series for demanding environments, and specialized variants like the XS M18 or cylindrical sensors, Schneider offers a diverse portfolio. This ensures the right sensor size, shape, and sensing characteristics can be found for specific mounting challenges or detection requirements.
Key Applications Where Schneider Inductive Sensors Excel:
- Position Verification: Confirming a part is correctly located in a fixture before a machining operation begins. (Reliable position feedback is critical).
- Object Counting: Accurately tallying products moving along a conveyor. (High repeat accuracy ensures accurate counts).
- End-of-Travel Detection: Safely signaling when a cylinder, slide, or door has reached its limit position. (Ruggedness withstands mechanical stress).
- Speed Monitoring: Detecting the teeth of a gear or the passing of metal flags to calculate rotational speed. (Fast response times capture rapid movement).
- Level Detection: Monitoring the position of a metal float in tanks or silos. (Immunity to liquids and debris is vital).
- Machine Safety: Used as part of safety interlocks to confirm guards are closed before machine start. (Reliability underpins safety functions).
Choosing the Right Sensor: Selecting the optimal Schneider inductive sensor involves considering:
- Target Material: Different metals (steel, stainless steel, aluminum, brass) have different sensing characteristics. Schneider provides specific data.
- Required Sensing Distance: The nominal operating distance needed between sensor face and target.
- Mounting Constraints: Size, shape (barrel, rectangular block), and mounting method (flush, non-flush).
- Environmental Conditions: Temperature range, presence of chemicals, water, dust, potential for impact. (Refer to IP rating requirements).
- Electrical Requirements: Operating voltage (commonly 10-30V DC), output type (NPN/PNP, NO/NC, analog), and connection type.
The Schneider Advantage: Beyond Just Detection
While the core function is object detection, choosing Schneider inductive sensors brings tangible benefits:
- Minimized Downtime: Their robust design and high reliability drastically reduce unexpected failures and maintenance interventions.
- Enhanced Process Quality: Consistent and accurate detection ensures processes run correctly, reducing scrap and rework.
- Simplified Engineering: Standardized connections, extensive documentation, and integration within Schneider’s wider automation ecosystem (TeSys, Modicon, etc.) streamline system design and troubleshooting.
- Long-Term Value: Durability translates into a longer service life, offering a better total cost of ownership compared to cheaper, less reliable alternatives. (Investment in quality yields returns over time).
In the intricate dance of industrial automation, where precision, speed, and reliability are paramount, Schneider inductive sensors act as the dependable, unwavering eyes. They operate silently in the background, unaffected by grime or vibration, consistently providing the critical feedback that keeps complex machinery synchronized and production lines flowing efficiently. For engineers seeking to build resilient, high-performing automation solutions, specifying Schneider Electric inductive proximity sensors isn’t just a component choice – it’s a strategic investment in operational excellence and long-term system reliability. Explore the extensive Schneider portfolio to find the precise sensor engineered to thrive in your specific application environment.