ring proximity sensor
- time:2025-07-02 02:30:55
- Click:0
Ring Proximity Sensors: Precision Non-Contact Detection for Demanding Applications
Imagine needing to know exactly when a metal component is in position on a high-speed assembly line, or precisely monitoring the movement of robotic arms without physical interference. In the intricate dance of modern automation and machinery, traditional contact-based sensors often fall short. This is where ring proximity sensors step in, offering unparalleled reliability and precision for non-contact object detection. Their unique design and robust operation make them indispensable components across countless industries, optimizing processes and ensuring safety with silent efficiency.
Understanding the Ring Proximity Sensor
A ring proximity sensor, as the name suggests, is typically a donut-shaped (annular) device designed to detect the presence or absence of a metallic target object passing through its central aperture without any physical contact. Unlike traditional contact switches or optical sensors, they leverage electromagnetic principles to sense objects passing through their core, creating a highly reliable and non-intrusive detection zone.
How Does a Ring Proximity Sensor Work?
The core operating principle is fundamentally inductive. Inside the sensor’s housing, an oscillating electromagnetic field is generated by a coil wound around the central opening. This field radiates outwards, primarily focused within the bore of the ring. When a conductive metal target enters this active sensing field, it induces eddy currents within the metal.
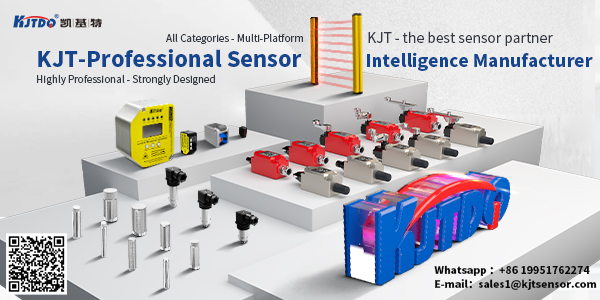
These eddy currents draw energy from the sensor’s oscillating circuit. This energy loss causes a measurable change in the circuit’s amplitude or frequency. Sophisticated electronics within the sensor detect this specific change, triggering a switching action in its output signal (typically changing from OFF to ON, or vice versa). Crucially, this detection happens without the sensor needing to touch the target. The target simply needs to pass through the ring.
Key Types and Variations
While adhering to the ring form factor, inductive ring sensors can have variations:
- Shielded vs. Unshielded: Shielded sensors have their magnetic field concentrated towards the front (bore), offering precise axial detection and reduced susceptibility to nearby metal objects. Unshielded types have a larger lateral sensing field but might be more affected by surrounding metal.
- DC 3-Wire (NPN/PNP): The most common industrial standard, providing a digital ON/OFF signal compatible with PLCs and control systems.
- Analog Output: Some advanced models provide an analog signal (e.g., 4-20mA, 0-10V) proportional to the distance of the target within the sensing range, enabling position monitoring.
- Size and Material: Available in a vast range of bore diameters to accommodate different target sizes and mounting requirements. Housings are typically robust materials like nickel-plated brass or stainless steel for durability in harsh environments.
The Compelling Advantages: Why Choose Ring Proximity Sensors?
- Non-Contact Operation: The defining benefit. Eliminates wear and tear on both the sensor and the target object, leading to significantly longer operational life and reduced maintenance costs compared to mechanical switches.
- Immunity to Surface Conditions: Unaffected by dirt, dust, oil, grease, moisture, or vibrations that plague optical sensors or mechanical contacts. Their performance remains consistent in challenging industrial settings.
- High Speed & Precision: Capable of detecting targets moving at extremely high speeds with remarkable repeatability and accuracy. Ideal for high-throughput automation and precise positioning tasks.
- Robustness: Designed to withstand shock, vibration, temperature extremes, and harsh chemicals common in factories, foundries, and processing plants.
- Simple Installation & Setup: Typically mounted by securing them around the path of the target object. No complex calibration is usually required beyond setting the sensing range and connecting the output.
- Long Sensing Ranges: Certain models offer surprisingly long detection ranges relative to their bore size, providing flexibility in application design.
Where Ring Proximity Sensors Shine: Applications Galore
The unique capabilities of ring proximity sensors make them vital in numerous scenarios:
- Position Verification: Confirming if a piston rod is fully extended/retracted, verifying the presence of a part at a specific station on an assembly line, or checking valve stem position.
- Speed Monitoring: Counting rotations or detecting the presence of gear teeth, sprockets, or fasteners on rotating shafts for RPM calculation or part counting.
- End-of-Travel Detection: Safely signalling the limit of travel for moving components like slides, carriages, or elevator cars (non-safety-critical).
- Machine Safety: Used as part of interlock systems to ensure guards are closed or tools are retracted before machine cycle start. (Note: For functional safety, specific safety-rated sensors are required).
- Robotics: Detecting the position of robotic arms, end effectors, or grippers for precise movement control.
- Conveyor Systems: Detecting metal components or pallets passing specific points for sorting, tracking, or process initiation.
- Metalworking & CNC: Tool presence/absence detection, spindle orientation verification, and workpiece positioning on lathes or mills.
- Packaging Machinery: Verifying the presence and position of metal lids, caps, or cans for filling, capping, or labeling operations.
- Fluid Power Systems: Monitoring position of hydraulic or pneumatic cylinders.
Selecting the Right Ring Sensor: Key Considerations
Choosing the optimal ring proximity sensor requires careful assessment:
- Target Material: Ferrous metals (steel, iron) are easiest to detect with standard inductive sensors. Non-ferrous metals (aluminum, brass, copper) require sensors specifically designed for them or offer reduced sensing ranges. Non-metallic targets cannot be detected by standard inductive sensors.
- Target Size & Shape: The sensor’s bore size must be large enough to allow the target to pass through freely. The target face presented to the sensor field should be sufficient to reliably trigger detection.
- Required Sensing Range: Define the necessary distance at which the sensor must detect the target as it passes through the ring. Choose a sensor with a sensing distance (Sn) that comfortably exceeds the application’s requirements to account for installation tolerances.
- Mounting Requirements: Consider available space, mounting method (threaded barrel, flanged), and orientation relative to the target path. Ensure adequate clearance around the sensor body.
- Environmental Conditions: Temperature extremes, chemical exposure, IP rating (dust/water ingress protection), and potential for mechanical shock or vibration dictate housing material and sensor specifications.
- Electrical Requirements: Match the supply voltage (e.g., 10-30V DC) and output type (NPN sinking, PNP sourcing, analog) to your control system.
Ring proximity sensors offer a uniquely effective solution for non-contact detection of metallic objects moving through their aperture. Their combination of reliability, durability, non-contact operation, and resistance to harsh conditions ensures they remain a cornerstone technology in modern industrial automation and machinery control. Understanding their principles, strengths, and ideal applications empowers engineers and technicians to implement robust and efficient sensing solutions.