heavy equipment proximity sensors
- time:2025-07-02 02:24:54
- Click:0
Heavy Equipment Proximity Sensors: Preventing Collisions and Enhancing Safety on Busy Job Sites
Imagine a bustling construction site: massive excavators swing, loaders shuttle tons of material, and dump trucks navigate tight spaces. Amidst this orchestrated chaos, visibility is often limited, blind spots are vast, and the margin for error is frighteningly small. A momentary lapse in attention or a misjudged distance can lead to catastrophic collisions, endangering personnel, damaging expensive machinery, and halting critical projects. This high-stakes environment is precisely where heavy equipment proximity sensor systems become indispensable lifesavers and productivity guardians.
Heavy equipment proximity sensors are sophisticated electronic detection systems designed specifically to monitor the environment around large machinery. Their core function is to identify objects, personnel, or other equipment entering preset danger zones and alert the operator immediately, providing crucial reaction time to prevent accidents. These systems are no longer optional luxuries; they are fundamental components of modern safety protocols in industries like construction, mining, quarrying, material handling, and logistics, where heavy machinery operates in close quarters.
How Do Heavy Equipment Proximity Sensors Work?
Unlike a single device, these systems typically employ a network of sensors strategically mounted around the equipment – on the front, rear, sides, and sometimes even on the boom or bucket. The principle involves emitting a signal (energy wave) and analyzing the reflection from nearby objects. Different sensor technologies achieve this in distinct ways:
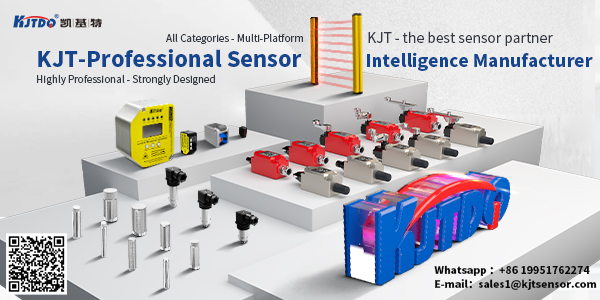
- Ultrasonic Sensors: Emit high-frequency sound waves. Measure the time taken for the echo to return to calculate distance. Effective in various weather conditions and relatively inexpensive, but can have limited range and be affected by certain surface materials.
- Radar Sensors (mmWave Radar): Transmit radio waves. Excellent at measuring distance and relative speed, even in challenging conditions like dust, fog, smoke, or total darkness. Highly reliable for detecting both stationary and moving objects. This technology is increasingly favored for its robustness on demanding job sites.
- RFID Systems: Utilize tags worn by personnel or placed on assets. Sensors on the equipment detect these tags when they enter a predefined zone. Primarily focused on personnel detection and ensuring exclusion zones are respected.
- Camera-Based Systems: Use visual cameras, sometimes combined with AI, to identify objects and people. Can provide valuable visual context to the operator but may be hampered by poor lighting, obstructions, or weather.
- Lidar (Light Detection and Ranging): Uses laser pulses to create precise 3D maps of the surroundings. Offers high accuracy but can be more expensive and potentially affected by heavy dust or rain.
The Power of Integration: Collision Avoidance Systems
Modern solutions often integrate multiple sensor types (like radar and camera) and fuse their data using intelligent algorithms. This Sensor Fusion significantly enhances reliability, reducing false alarms and ensuring robust detection across diverse scenarios. These integrated packages are commonly referred to as Collision Avoidance Systems (CAS) or Object Detection Systems (ODS).
Critical Benefits Driving Adoption
The implementation of heavy equipment proximity detection systems delivers multifaceted advantages:
- Dramatically Improved Safety: This is the paramount benefit. By providing timely audio and visual alerts (often escalating alarms based on proximity), systems give operators the critical seconds needed to stop or maneuver safely. This directly prevents accidents involving pedestrians, spotters, ground personnel, and other equipment.
- Reduced Risk of Property Damage: Accidental collisions between equipment, or with structures, materials, or parked vehicles, incur substantial repair or replacement costs. Proximity sensors act as a vital electronic buffer, protecting valuable assets.
- Enhanced Operator Situational Awareness: Even the most experienced operators have significant blind spots. Proximity sensor systems act as an extra set of eyes, continuously monitoring areas impossible to see directly from the cab, especially around the rear and sides of large machines. This significantly reduces operator stress and fatigue.
- Increased Productivity & Reduced Downtime: Preventing accidents inherently avoids costly project delays associated with investigations, repairs, and potential site shutdowns. Operators can also work more confidently and efficiently in congested areas.
- Regulatory Compliance & Lower Insurance Premiums: Safety regulations worldwide are increasingly mandating or strongly recommending proximity detection technology. Adopting these systems demonstrates a proactive safety culture, aiding compliance and often leading to favorable insurance terms.
- Data Logging & Incident Analysis: Many advanced systems record detection events and operator responses. This data is invaluable for investigating near-misses, improving training protocols, and refining operational procedures.
Key Considerations for Implementation
Selecting and installing the right proximity sensing system requires careful thought:
- Site Environment: Dust, mud, vibration, extreme temperatures, and electromagnetic interference are common. Robustness and environmental sealing (IP ratings) are non-negotiable features. Radar often excels in harsh conditions.
- Equipment Type & Blind Spots: Different machines (excavators, haul trucks, loaders, cranes) have unique blind spot profiles. The sensor configuration must be tailored accordingly.
- Detection Range & Zones: Define critical warning and danger zones accurately. Systems should allow customizable range settings and zone shaping to suit specific operational needs.
- Alert Types: Effective systems use clear, attention-grabbing visual (flashing LEDs, in-cab displays) and audible alerts located both inside the cab and externally to warn nearby personnel. Escalating alarms based on proximity level are essential.
- False Alarm Management: Excessive false alarms lead to “alarm fatigue,” where operators start ignoring warnings. Advanced filtering algorithms and sensor fusion are key to minimizing false positives without compromising safety.
- Training & Maintenance: Operators must be thoroughly trained on system capabilities, limitations, and how to respond to alerts. Regular system checks and maintenance are crucial to ensure continuous, reliable operation. Proper cleaning of sensor lenses/faces is vital.
The Future is Smart and Connected
Proximity sensor technology continues to evolve rapidly. Integration with telematics platforms allows fleet managers to monitor system health and safety events remotely. AI-powered object classification is enhancing the ability to distinguish between people, machinery, and benign obstacles. Zone-based speed limiting (automatically reducing machine speed when entering high-risk areas) is an emerging frontier. V2X (Vehicle-to-Everything) communication, where machines share their position and intention data, promises even greater situational awareness across entire sites.
In an industry where danger is inherent but preventable accidents are unacceptable, heavy equipment proximity sensors represent a fundamental shift towards a safer, more efficient future. By acting as an electronic safety net, constantly vigilant where human senses fall short, these systems are not just protecting investments in machinery—they are safeguarding the irreplaceable lives of the people who build our world. Investing in robust collision avoidance technology is an investment in zero-harm objectives and sustainable operational excellence.