explosion proof proximity sensor
- time:2025-07-02 02:18:52
- Click:0
Safe Detection in Hazardous Zones: The Critical Role of Explosion Proof Proximity Sensors
Imagine the intense environment of an oil refinery, a chemical processing plant, or a dusty grain silo. Sparks fly, volatile gases linger, and combustible dust particles hang invisibly in the air. In such intrinsically hazardous locations, standard electrical equipment is not just unreliable; it’s a potential ignition source capable of triggering catastrophic explosions. This is where the specialized engineering of explosion proof proximity sensors becomes not merely useful, but utterly essential for operational safety and continuity. These rugged devices provide reliable, non-contact object detection precisely where the risk of explosion demands the highest levels of protection.
Understanding the “Explosion Proof” Imperative
An explosion proof proximity sensor is fundamentally designed with one overriding goal: to prevent an electrical device from igniting the surrounding atmosphere, even under fault conditions. The term “explosion proof” doesn’t mean the device is immune to explosions. Instead, it signifies that the sensor’s enclosure is engineered to:
- Contain Any Internal Explosion: Should an internal electrical fault (like a spark or arc) occur within the sensor’s housing, the robust enclosure is strong enough to contain the resulting blast without rupturing.
- Prevent Flame Propagation: Any hot gases or flames generated by an internal explosion are cooled sufficiently as they escape through specially designed flame paths (flanges or threads) before reaching the hazardous external atmosphere. This cooling prevents ignition of the surrounding gases or dust.
- Limit Surface Temperature: The sensor’s external surface temperature, even during operation or fault conditions, remains below the auto-ignition temperature of the specific gases or dusts present in the environment. This is known as the Temperature Class (T-rating).
How Proximity Sensing Works in High-Risk Environments
At their core, explosion proof proximity sensors operate on the same fundamental principles as their standard counterparts – typically inductive (for detecting metallic targets) or capacitive (for detecting metallic and non-metallic targets). They generate an electromagnetic field and detect changes in that field caused by the approach of a target object. The critical difference lies in the integration of these sensing technologies within the explosion-proof housing and the incorporation of intrinsic safety barriers or other protection methods at the electrical interface.
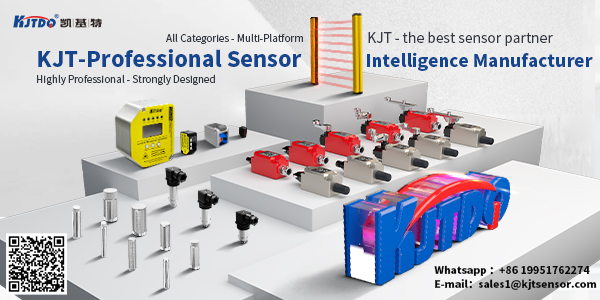
Key components that enable their safe operation include:
- Robust Enclosures: Constructed from heavy-duty materials like stainless steel, brass, or specially certified plastics/aluminum alloys, capable of withstanding high internal pressures.
- Certified Flame Paths: Precisely machined flanges or threaded joints that provide controlled pathways for escaping gases, ensuring sufficient cooling.
- Hermetic Sealing: Effective sealing prevents the ingress of dust, moisture, or flammable atmospheres into the internal circuitry.
- Certified Cable Glands: Ensure secure and explosion-proof entry for the power and signal cables.
The Backbone of Safety: Certifications and Standards
The design and manufacturing of explosion proof proximity sensors are governed by stringent international and regional standards. Compliance isn’t optional; it’s mandatory for legal operation in hazardous areas. Key certification bodies and standards include:
- ATEX (Europe): Directive 2014/34/EU, categorizing equipment into Equipment Groups (I for mining, II for surface industries) and Protection Levels (e.g., 1G, 2G for gases; 1D, 2D for dust).
- IECEx (International): The IEC System for Certification to Standards Relating to Equipment for Use in Explosive Atmospheres, facilitating global acceptance.
- NEC / CEC (North America): The National Electrical Code (NFPA 70) and Canadian Electrical Code define Hazardous Locations (Classes, Divisions, Zones) and acceptable protection methods (e.g., Explosionproof, Type X, Y, Z; Intrinsically Safe).
Choosing a sensor with the correct certification (ATEX, IECEx, or specific national approvals like UL, CSA for Class/Division) for the specific zone (Zone 0/1/2 for gases; Zone 20/21/22 for dust) and gas group/temperature class is absolutely critical. Failure to match the sensor’s rating to the actual hazard can have devastating consequences.
Where Explosion Proof Proximity Sensors Are Non-Negotiable
These specialized sensors are indispensable across a vast spectrum of industries where flammable atmospheres are a constant or potential threat:
- Oil & Gas: Upstream (drilling rigs, wellheads), Midstream (pipelines, pumping stations), Downstream (refineries, storage tanks). Monitoring valve positions, tank levels, machine guard positions, and equipment presence.
- Chemical & Pharmaceutical: Processing plants handling volatile solvents, gases, or fine powders. Detecting fill levels, conveyor belt jams, or component presence in reactors and mixers.
- Mining (Coal & Hard Rock): Detecting methane gas zones, monitoring conveyor systems, and signalling machine positions where combustible coal dust or flammable gases are present.
- Grain Handling & Milling: Silos, elevators, and processing facilities where explosive grain dust permeates the air. Ensuring safe operation of conveyors, chutes, and hatches.
- Paints & Coatings: Spray booths and production areas laden with flammable solvent vapors. Position detection on automated painting lines or solvent handling equipment.
- Wastewater Treatment: Monitoring equipment in areas where hazardous vapors like methane or hydrogen sulfide can accumulate.
Selecting the Right Sensor: Key Considerations
When specifying an explosion proof proximity sensor, several vital factors go beyond simple detection range:
- Hazardous Area Classification: Precisely know the Zone (0, 1, 2, 20, 21, 22), Gas Group (e.g., IIC for hydrogen, IIB for ethylene), Dust Group, and required Temperature Class (T-rating) for the installation point.
- Required Certification: Mandatory certifications (ATEX, IECEx, UL, CSA) for the operating region and specific hazard class.
- Sensing Technology: Inductive for metals, Capacitive for materials like plastic, wood, or liquids. Shielded or unshielded mounting options.
- Environmental Durability: Beyond explosion protection, consider IP rating against dust and water ingress, resistance to chemicals, oils, and physical shock/vibration. High-grade stainless steel housings are often preferred for harsh chemical or washdown environments.
- Electrical Characteristics: Operating voltage, output type (PNP/NPN, NO/NC, analog), switching current, and connection type (cable or connector).
- Performance Specifications: Sensing range, repeat accuracy, response time, and operating temperature range.
Enabling Safety, Reliability, and Productivity
Explosion proof proximity sensors are far more than just components; they are fundamental safety guardians within high-risk industries. By providing reliable non-contact detection without generating sparks or unsafe surface temperatures, they play a critical role in preventing catastrophic events. Their robust design ensures longevity and minimizes maintenance needs in challenging environments. Investing in the correctly certified, high-quality sensor for the specific hazard is an investment in protecting personnel, safeguarding expensive equipment, preventing environmental damage, and ensuring the uninterrupted, safe operation of vital industrial processes. In environments where danger is ever-present, these sensors provide the essential layer of detection safety demanded by the most stringent global standards.