m12 inductive sensor
- time:2025-07-02 02:12:51
- Click:0
The Mighty M12 Inductive Sensor: Precision Detection for Demanding Automation
Imagine a robotic arm seamlessly placing components on a circuit board, a conveyor belt humming as it transports metal parts with perfect timing, or a high-speed packaging line filling containers without missing a beat. At the heart of countless such industrial motions, often unseen but critically important, lies a workhorse of automation: the M12 inductive sensor. These compact, rugged devices are fundamental to modern manufacturing, providing reliable, non-contact detection of metal objects. Understanding their operation, strengths, and applications unlocks their potential to enhance efficiency and reliability in diverse industrial settings.
What Exactly is an M12 Inductive Sensor?
An M12 inductive sensor, sometimes simply called an M12 proximity switch, is a specific form of non-contact electronic sensor. Its name derives from its standardized threaded cylindrical housing with a 12mm diameter. This compact size makes it incredibly versatile for installation in tight spaces common on machinery and production lines.
Like all inductive sensors, its operation is based on the principle of electromagnetic induction. Inside the sensor face resides a coil through which a high-frequency oscillating current flows. This generates a high-frequency electromagnetic field around the active sensing area. When a ferrous metal target (like steel or iron) or sometimes even non-ferrous metals (depending on sensor design and material) enters this field, eddy currents are induced within the target. These eddy currents draw energy from the sensor’s oscillating circuit, causing a detectable change – typically a reduction in amplitude. Sophisticated electronics within the sensor monitor this change and trigger a solid-state output switch (PNP or NPN, NO or NC configurations are common), signaling the presence or absence of the target. This entire process happens without any physical contact, eliminating wear and tear on both the sensor and the target object.
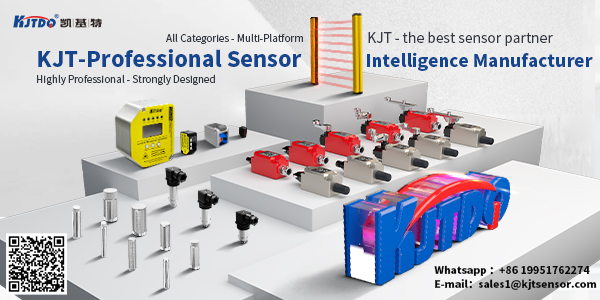
Why Choose the M12 Form Factor? Key Advantages
The M12 standard isn’t arbitrary; it delivers significant practical benefits crucial for industrial environments:
- Compact Size & High Density Installation: The small diameter allows mounting in locations inaccessible to larger sensors. Multiple sensors can be placed close together for complex detection tasks on intricate machinery.
- Robust Construction & Environmental Resistance: Engineered for harsh conditions, M12 inductive sensors typically feature rugged metal or high-grade plastic housings. They boast impressive ingress protection ratings (commonly IP67, IP68, or IP69K), meaning they are highly resistant to dust and water intrusion, even surviving washdowns in food processing or exposure to oils and coolants in metalworking.
- High-Speed Detection & Switching Frequency: These sensors react incredibly quickly to the presence of a target. With typical switching frequencies ranging from 0.5 kHz to 5 kHz or higher, they can reliably detect objects moving at very high speeds on conveyors or rotating machinery.
- Exceptional Reliability & Long Service Life: The non-contact sensing principle inherently means no moving parts to wear out, leading to extremely long operational lifespans and minimal maintenance requirements compared to mechanical switches. They are also inherently less susceptible to vibration.
- High Resistance to Environmental Interference: Well-designed M12 inductive sensors exhibit excellent immunity to common industrial nuisances like dirt, dust, moisture, smoke, and even many types of electromagnetic interference (EMI). Their focused sensing field also reduces the chance of false triggers from nearby objects.
- Standardization & Easy Integration: The M12 threaded barrel and standard connector interfaces enable quick, secure mounting and connection. The widespread adoption across automation components ensures easy sourcing and compatibility with existing control systems and cabling infrastructure (M12 connectors are ubiquitous).
Shielding Matters: Flush Mounting vs. Non-Flush Mounting
A critical design choice for M12 inductive sensors is the shielded (flush-mountable) vs. non-shielded (non-flush mountable) type:
- Shielded / Flush Mountable Sensors: These have a metal ring surrounding the sensing face. This effectively focuses the electromagnetic field axially forward from the sensor face. The key benefit is that they can be mounted flush within metal brackets or panels without the surrounding metal interfering with their operation or triggering false detections. However, this shielding typically results in a slightly shorter sensing range compared to non-shielded versions of the same size.
- Non-Shielded / Non-Flush Mountable Sensors: These lack the front shielding ring, allowing their electromagnetic field to extend radially sideways as well as forward. This grants them a longer nominal sensing range for a given size. However, they MUST be mounted with sufficient clearance from any surrounding metal (as specified in the datasheet, often 1-2 times the sensor diameter or more). Installing them too close to metal mounting surfaces will cause false triggering or reduced sensing range.
M12 Sensor Shielding Feature |
Mounting Capability |
Sensing Range |
Typical Use Case |
Shielded / Flush Mountable |
Can be mounted flush in metal panels |
Shorter range |
Tight spaces, embedded installations |
Non-Shielded |
Requires clearance from metal |
Longer range |
General applications with space for mounting |
Where the M12 Inductive Sensor Shines: Core Applications
The combination of compactness, robustness, and reliable non-contact detection makes M12 inductive sensors indispensable across a vast spectrum of industries:
- Factory Automation & Robotics: Position detection of arms, grippers, and end effectors; verifying part presence or absence on fixtures and pallets; counting parts on conveyors; end-of-travel limit sensing.
- Material Handling & Packaging: Detecting metal components, cans, or foil lids on conveyors; verifying position in filling machines, capping machines, and labeling systems; controlling sorting gates.
- Automotive Manufacturing: Monitoring component positioning during assembly (engines, transmissions); robotic welding seam tracking; parts presence verification in aggressive environments with oils and sparks.
- Food & Beverage Processing: Detecting metal cans, caps, or machinery components in washdown areas (requiring high IP69K ratings and often stainless steel housings); verifying positions in filling/packaging lines.
- Machine Tool & Metalworking: Tool breakage detection (monitoring drill bits); confirming chuck jaw position; monitoring spindle orientation; detecting metal workpieces for process initiation.
- Assembly Line Control: Ensuring components are correctly seated before fastening; detecting passing pistons or cams on machinery; providing position feedback for actuators.
Selecting the Right M12 Inductive Sensor
Choosing the optimal sensor involves carefully considering several factors:
- Target Material: Ferrous steel offers the longest sensing ranges. Non-ferrous metals like aluminum, copper, or brass significantly reduce the effective sensing distance (often around 50-60% less than steel).
- Required Sensing Distance (Sn): Determine the maximum distance at which the target needs to be reliably detected. Always choose a sensor with a nominal sensing range (Sn) slightly larger than your actual required gap to account for installation tolerances and environmental factors. Remember: The Sn rating is usually given for mild steel targets.
- Shielding Type (Flush vs. Non-Flush): Decide based on your mounting constraints. Can it be