24vdc proximity sensor
- time:2025-07-02 02:36:57
- Click:0
The Essential Role of 24VDC Proximity Sensors in Industrial Automation
Ever wondered what silently ensures precise positioning, counts products at lightning speed, or prevents costly collisions on a factory floor? The unsung hero is often the humble 24VDC proximity sensor. These ubiquitous workhorses form the sensory backbone of countless automated systems, offering reliable, non-contact detection critical for efficiency, safety, and process control. Understanding why 24VDC has become the de facto standard and how these sensors function is key for engineers, technicians, and anyone involved in modern manufacturing, packaging, or machinery.
What Exactly is a Proximity Sensor (Prox)?
At its core, a proximity sensor detects the presence or absence of an object within its sensing range without needing physical contact. Unlike mechanical limit switches that require a direct bump, proximity sensors operate electromagnetically (inductive types) or electrostatically (capacitive types), making them incredibly durable, fast, and suitable for harsh environments involving dirt, dust, oil, or vibration. Inductive sensors are the most common type used exclusively for detecting metallic targets (steel, aluminum, brass, etc.). Capacitive sensors, conversely, can detect a much wider range of materials, including liquids, powders, plastics, and wood, by sensing changes in an electrostatic field.
Why 24VDC? The Industrial Sweet Spot
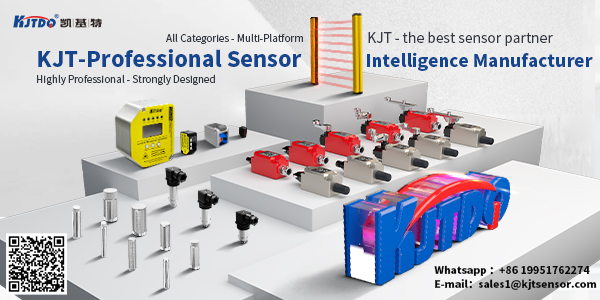
The “24VDC” designation specifies the operating voltage. This nominal DC voltage has emerged as the dominant standard in industrial control systems for compelling reasons:
- Safety: Compared to higher AC voltages traditionally used (e.g., 120VAC or 240VAC), 24VDC is considered a low voltage, significantly reducing the risk of severe electrical shock during installation, maintenance, or accidental contact. This enhances personnel safety substantially.
- Noise Immunity: DC power systems are inherently less susceptible to electrical noise and interference compared to AC systems. In noisy industrial environments filled with variable frequency drives (VFDs), large motors, and switching relays, 24VDC proximity sensors offer superior reliability and signal stability. False triggering is minimized.
- Compatibility: Modern Programmable Logic Controllers (PLCs), the brains of automation, predominantly use 24VDC for their input circuits. Using 24VDC sensors ensures seamless plug-and-play compatibility without requiring additional signal conditioning or voltage converters. This simplifies design, installation, and troubleshooting.
- Efficiency: 24VDC control systems, including wiring and power supplies (SMPS - Switch Mode Power Supplies), are often more energy-efficient than their higher-voltage AC counterparts, contributing to lower operating costs.
- Standardization: The widespread adoption creates economies of scale. Components (sensors, PLCs, power supplies, cabling, connectors) are readily available globally and are generally more cost-effective due to high-volume manufacturing.
Key Functions and Advantages of 24VDC Proximity Sensors
These sensors provide critical functionality:
- Non-Contact Detection: The biggest advantage. No physical wear occurs during detection, leading to exceptionally long service life compared to mechanical switches. This translates to lower maintenance costs and less downtime.
- High Switching Speed: Capable of detecting targets and providing an output signal in milliseconds. This high-speed response is essential for tracking fast-moving objects on conveyors, high-speed counting applications, or precision positioning.
- Robustness: Typically housed in rugged materials like nickel-plated brass or stainless steel, they withstand demanding conditions – impacts, cutting fluids, coolants, metal chips, and significant temperature variations. Their IP (Ingress Protection) ratings (e.g., IP67, IP68) signify resistance to dust and water ingress.
- Output Configurations: Primarily provide a digital output (ON/OFF signal). Two main wiring types exist:
- PNP (Sourcing): Outputs positive voltage (+24V) when active. Common in Europe/Asia.
- NPN (Sinking): Outputs ground (0V) when active. Common in the Americas. Understanding the sinking vs sourcing requirement of your PLC input is crucial for correct sensor selection.
- Simple Integration: Typically feature standard M8, M12, or M18 threaded barrels for easy mounting, along with pre-manufactured cables or quick-disconnect connectors, making installation fast and straightforward.
Selecting the Right 24VDC Proximity Sensor
Choosing the optimal sensor involves several key considerations:
- Sensing Principle: Inductive for metals, Capacitive for non-metals/liquids.
- Target Material & Size: Affects the effective sensing distance. Smaller targets or specific materials (like non-ferrous metals for inductive sensors) require closer proximity or specialized sensors. Always refer to the sensor’s rated operating distance (Sn) and safe mounting distances.
- Required Sensing Distance: Choose a sensor whose nominal sensing range comfortably exceeds the actual gap needed in the application to account for tolerances. Factor in mounting flush or non-flush for inductive types.
- Output Type (PNP/NPN): Must match the requirements of the connected control device (e.g., PLC input).
- Electrical Specifications: Ensure compatibility with the supply voltage (typically 10-30VDC), check current consumption, and consider short-circuit/overload protection.
- Environmental Factors: Temperature extremes, chemical exposure (requiring stainless steel housings), washdown conditions (high IP rating), or high-pressure levels necessitate specific sensor builds. EMC (Electromagnetic Compatibility) performance may also be critical in high-noise areas.
- Housing Style & Size: Barrel shape (cylindrical), block shape, or specialty designs must fit the available mounting space. Thread size (M8, M12, M18) is standard.
- Connection Method: Integrated cable, connector (like M12 connectors), or quick-disconnect versions.
Installation Tips for Optimal Performance
Proper installation maximizes reliability:
- Mounting: Ensure secure mounting to prevent vibration from altering the sensing gap.
- Wiring: Follow manufacturer diagrams meticulously for PNP or NPN wiring. Use shielded cable in electrically noisy environments and ground the shield properly at the controller end (not at the sensor). Twisted pair cables can also improve noise immunity.
- Sensing Field: Be aware of the sensor’s active sensing field shape. Avoid mounting near other metal objects (for inductive sensors) or materials (for capacitive sensors) that could inadvertently trigger the device. Maintain the manufacturer’s recommended clearance distances.
- Multiple Sensors: Space sensors sufficiently apart to prevent mutual interference. Some sensors offer synchronization options to mitigate this.
Ubiquitous Applications: Where Reliability Counts
24VDC proximity sensors are truly omnipresent in automation:
- Position Verification: Detecting the presence of a part on a fixture, pallet, or conveyor.
- End-of-Travel Detection: Signaling when a cylinder is fully extended or retracted.
- Object Counting: Tallying products on a high-speed line.
- Speed Monitoring: Measuring RPM via detection of gear teeth or shaft targets.
- Level Sensing: Using capacitive sensors to detect liquid levels in tanks or bin levels of bulk materials (grains, powders, pellets).
- Machine Safety: Confirming guard doors are closed before machine start-up or monitoring safety perimeters.