proximity sensor for water level
- time:2025-06-24 02:48:43
- Click:0
Proximity Sensors: Revolutionizing Water Level Detection Without Contact
Getting water level monitoring right is critical. Whether it’s preventing overflows in industrial tanks, ensuring pumps don’t run dry in agricultural systems, or safeguarding against basement flooding, inaccurate or unreliable measurements can lead to costly downtime, damage, and wasted resources. Traditional methods like float switches or conductive probes, while functional, often suffer from mechanical wear, fouling, and limited adaptability. This is precisely where proximity sensors for water level detection step in, offering a robust, maintenance-light alternative that is transforming how we manage liquids.
The Contact Conundrum: Why Non-Contact Wins
The primary limitation of many traditional water level sensors is their need for direct physical contact with the liquid. Float mechanisms can jam or become encrusted. Conductivity probes corrode or collect mineral deposits, requiring frequent cleaning. Pressure sensors need submersion and can be sensitive to changes in liquid density or temperature. These factors directly impact reliability and increase maintenance overheads.
Proximity sensors solve this fundamental problem. They detect the presence or level of water without making direct contact. Instead, they interact with the physical properties of the liquid or its container through an intervening barrier – typically the wall of a tank, reservoir, or pipe. This non-invasive approach offers significant advantages:
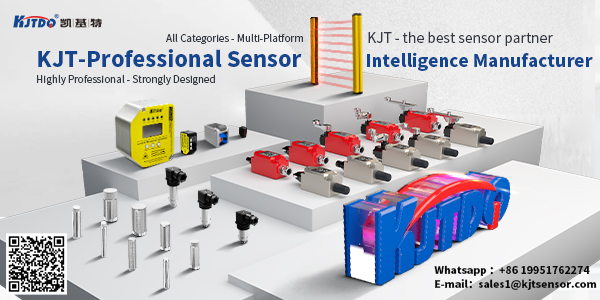
- Reduced Maintenance: With no moving parts submerged or exposed to potential contaminants or corrosive liquids, sensors last longer and require far less cleaning or replacement.
- Enhanced Reliability: Immunity to scale buildup, corrosion affecting sensing elements, and mechanical jamming leads to more consistent, dependable readings.
- Simplified Installation: Can often be mounted externally on non-metallic tanks (for specific types) or internally without complex seals, reducing installation complexity and risk of leaks.
- Versatility: Capable of working with various types of liquids, including corrosive, viscous, or contaminated water, where contact sensors would fail quickly.
How Proximity Sensors “See” the Water Through Walls
The magic lies in the underlying technology of proximity sensors adapted for liquid level sensing. Two main types dominate this application:
- Capacitive Proximity Sensors: These sensors function by detecting changes in capacitance. They essentially form one plate of a capacitor, with the tank wall and the water acting as the other plate and dielectric material. As the water level rises or falls near the active face of the sensor, it changes the capacitance value. The sensor’s electronics detect this change and trigger a switch output (on/off) or provide an analog signal proportional to the level. Crucially, capacitive sensors can detect water through non-metallic materials like plastic, glass, or ceramic tanks – a massive advantage for many applications. Their sensitivity allows detection even through thick walls, making them ideal for smaller reservoirs or where external mounting is mandatory. The key to their success lies in the significant difference between the dielectric constant of air (≈1) and water (≈80).
- Inductive Proximity Sensors: While primarily known for detecting metals, inductive sensors can be used for water level detection specifically within metallic tanks. They generate an electromagnetic field. When the water (a conductive medium) rises high enough to interact with this field, it induces eddy currents in the water. The sensor detects the resulting disturbance in its own electromagnetic field. This method provides highly reliable point-level detection (full/empty) inside steel or aluminum containers, offering a robust solution where tank material compatibility exists.
Unlocking Potential: Key Applications for Water Level Proximity Sensors
The unique benefits of non-contact detection make these sensors invaluable across numerous sectors:
- Industrial Process Control: Monitoring levels in chemical storage tanks, coolant reservoirs, wash tanks, and process vessels where liquids may be corrosive, abrasive, or require sterile conditions. Minimizing downtime is critical here.
- HVAC and Plumbing: Protecting boilers and chillers from low-water conditions, controlling sump pumps in basements, managing condensate collection tanks, and preventing overflows in water treatment systems.
- Agriculture and Irrigation: Ensuring water tanks or reservoirs for irrigation systems are adequately filled, protecting pumps from dry running, and monitoring nutrient solution levels in hydroponics.
- Appliance Manufacturing: Used internally in appliances like coffee makers, steam ovens, dishwashers, and washing machines to accurately detect fill levels safely and reliably within confined spaces.
- Water and Wastewater Management: Point-level detection in collection tanks, chemical dosing tanks, and filter backwash systems. Their resilience to fouling is particularly advantageous in wastewater settings.
- Automotive and Transportation: Monitoring washer fluid levels, coolant expansion tanks, and fuel in specific auxiliary systems.
Selecting the Right Proximity Sensor for Water Level
Choosing the optimal sensor involves considering several factors:
- Tank Material: Is the tank metal or non-metal? This directly dictates whether a capacitive (non-metal) or inductive (metal) sensor is suitable.
- Detection Type Needed: Is simple point-level detection (e.g., high-level alarm, low-level pump protection) sufficient, or is continuous level monitoring required? Capacitive sensors come in both discrete (switch) and analog output variants.
- Liquid Properties: While generally robust, extremely low-conductivity liquids (like some pure solvents) can be challenging for inductive sensors, and liquids with very high viscosity might influence capacitive field penetration. Understand the characteristics of the water-based liquid.
- Temperature and Pressure: Ensure the sensor’s specified operating range matches the environment inside the tank, including maximum temperature and pressure ratings at the mounting point.
- Mounting: Can the sensor be mounted externally (only capacitive on non-metal tanks), or must it be internally mounted? Internal mounting might require specific housing materials for chemical compatibility. Consider the necessary sensing range through the tank wall.
- Output Signal: Match the sensor’s output (PNP/NPN transistor, analog voltage/current) to the requirements of your control system (PLC, microcontroller, relay).
The Future is Clear (and Non-Contact)
The evolution of proximity sensors specifically tailored for water level detection represents a significant leap forward in liquid management technology. By eliminating the weaknesses inherent in contact-based methods, they deliver unparalleled reliability, reduced maintenance costs, and increased operational efficiency. Their ability to operate effectively through tank walls opens up possibilities for simpler retrofitting and safer monitoring in hazardous environments. As sensor technology continues to advance, offering even greater precision, integration with IoT platforms for remote monitoring, and expanded capabilities for challenging liquids, their adoption as the go-to solution for robust water level monitoring is set to accelerate. For engineers and system designers seeking a dependable, long-lasting solution, non-contact proximity sensors provide a powerful and elegant answer, ensuring water levels are always known, precisely controlled, and never a source of unwelcome surprises or operational disruption. The capability to detect levels externally on plastics tanks or internally in metal vessels without moving parts fundamentally changes maintenance schedules and system design for water-based applications across countless industries, from preventing minor appliance malfunctions to safeguarding large-scale industrial processes and critical infrastructure against potential water level-related failures, even in harsh or explosive environments.