lidar laser power
- time:2025-03-20 01:26:20
- Click:0
Title: Optimizing LiDAR Performance: The Critical Role of Laser Power in Sensing Technology
In an era where autonomous vehicles map city streets, drones survey disaster zones, and robots navigate warehouses, LiDAR (Light Detection and Ranging) has emerged as the eyes of modern technology. At the heart of this revolutionary system lies a deceptively simple component: the laser. But not just any laser—its power output directly determines whether a LiDAR system succeeds or stumbles. Understanding lidar laser power isn’t just technical jargon; it’s the key to unlocking precision, safety, and efficiency in applications that shape our future.
What Is LiDAR Laser Power, and Why Does It Matter?
LiDAR systems work by emitting laser pulses and measuring the time it takes for reflected light to return. The laser’s power—measured in watts (W) or milliwatts (mW)—dictates the energy of each pulse. Higher power means stronger signals, enabling longer detection ranges and better performance in challenging conditions like fog or rain. However, there’s a catch: too much power risks eye safety violations, while too little compromises accuracy. Striking this balance is what makes laser power optimization a cornerstone of LiDAR design.
For instance, automotive LiDAR systems operating at 905 nm wavelengths often use lasers with powers between 10–40 W. In contrast, 1550 nm LiDAR, favored for its eye-safe properties, can deploy higher-power lasers (up to 1.5 kW pulsed) without endangering human vision. This distinction highlights how laser power isn’t a one-size-fits-all metric—it’s a variable finely tuned to the application’s demands.
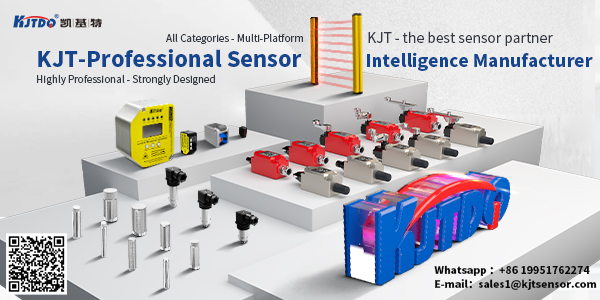
The Science Behind Laser Power and LiDAR Performance
The relationship between laser power and LiDAR effectiveness hinges on three factors: range, resolution, and energy efficiency.
- Range: A higher-power laser can travel farther before its signal dissipates. For example, geospatial mapping drones require lasers with >8 W power to scan terrain from altitudes exceeding 1,000 meters. Conversely, indoor robots might use sub-1 W lasers for short-range navigation.
- Resolution: More powerful lasers improve signal-to-noise ratios, allowing LiDAR to detect smaller objects. This is critical for autonomous vehicles identifying pedestrians or debris at 200+ meters.
- Energy Efficiency: High-power lasers drain batteries faster. Engineers often balance power with pulse frequency—shorter, intense pulses reduce energy waste while maintaining performance.
A 2022 study by the Journal of Optical Engineering found that optimizing laser power could boost LiDAR detection accuracy by up to 30% in low-visibility environments. Yet, pushing power limits also raises thermal management challenges. Overheated lasers degrade over time, underscoring the need for advanced cooling solutions in high-performance systems.
Choosing the Right Laser Power: Industry Applications
Different sectors prioritize laser power differently, reflecting their unique operational needs:
- Autonomous Vehicles: Safety regulations cap laser power at Class 1 (eye-safe) levels. Companies like Velodyne and Luminar use 1550 nm lasers with higher permissible power to achieve ranges of 250+ meters while complying with standards.
- Environmental Monitoring: Airborne LiDAR for forest mapping employs high-power lasers (20–30 W) to penetrate dense canopies. NASA’s G-LiHT system, for example, uses 1064 nm lasers to measure carbon storage in rainforests.
- Robotics: Warehouse robots prioritize efficiency over range, often using low-power (1–5 W) lasers to navigate confined spaces without overheating.
Interestingly, the rise of solid-state LiDAR—which uses semiconductor lasers—has enabled smaller, more power-efficient designs. A report by Yole Développement predicts that solid-state systems will dominate 60% of the automotive LiDAR market by 2027, thanks to their ability to deliver balanced power and compact form factors.
Safety vs. Performance: Navigating Regulatory Limits
Laser safety standards, such as the IEC 60825-1, impose strict limits on permissible exposure levels. For 905 nm LiDAR, this often restricts lasers to 75–100 W peak power in short pulses. Meanwhile, 1550 nm systems exploit the eye’s reduced sensitivity to infrared light, allowing powers up to 1,500 W without violating Class 1 limits.
However, regulatory compliance isn’t just about power—it’s about how that power is delivered. Pulsed lasers spread energy over time, reducing risk compared to continuous-wave beams. Innovators like Aeva are pioneering frequency-modulated continuous-wave (FMCW) LiDAR, which combines coherent detection with lower peak power for safer, longer-range sensing.
Future Trends: Pushing the Boundaries of Laser Power
Emerging technologies are redefining what’s possible with LiDAR laser power:
- Quantum Dot Lasers: These nanoscale devices promise higher efficiency and tunable wavelengths, enabling customizable power profiles for diverse applications.
- SWIR (Short-Wave Infrared) LiDAR: Operating at 1350–1600 nm, SWIR systems leverage atmospheric transmission windows to achieve longer ranges with moderate power.
- AI-Driven Power Modulation: Machine learning algorithms now adjust laser power in real time based on environmental conditions—a breakthrough highlighted in Waymo’s 5th-gen LiDAR.
As the demand for LiDAR grows—projected to reach $8.4 billion by 2030 (Global Market Insights)—the race to optimize laser power will intensify. Whether it’s enabling safer self-driving cars or more precise climate models, the pulse of progress lies in mastering this delicate balance.
From the lab to the real world, lidar laser power remains a linchpin of modern sensing technology. Its optimization isn’t just an engineering challenge—it’s a gateway to smarter, safer, and more sustainable innovations. And as industries continue to push the envelope, one thing is clear: the future of LiDAR shines brighter than ever.