infrared photoelectric sensor
- time:2025-07-28 08:57:38
- Click:0
The Unseen Workforce: How Infrared Photoelectric Sensors Power Modern Automation
Imagine a world where machines perceive the presence, absence, or position of objects without physical touch, operating silently across countless industries. This is the fundamental reality enabled by infrared photoelectric sensors. These ubiquitous, versatile devices form the bedrock of modern automation, leveraging invisible light to create smarter, safer, and more efficient systems. While we rarely see them, their impact is felt everywhere – from the factory floor to your local supermarket door. This exploration delves into the working principles, diverse types, critical applications, and vital considerations surrounding these indispensable optoelectronic components.
The Core Principle: Light Interrupted
At its heart, an infrared photoelectric sensor operates on a straightforward concept involving a light emitter and a light receiver. The emitter directs a focused beam of infrared light – light just beyond the visible spectrum’s red end. This beam travels towards the receiver unit. The fundamental detection mechanism hinges on how this beam interacts with the target object:
- Beam Intact: The IR light reaches the receiver unobstructed. The sensor interprets this state (e.g., “No Object Present” in a retro-reflective or through-beam setup).
- Beam Interrupted: When an object enters the beam path, it blocks or significantly scatters the IR light, preventing it (or reducing its intensity) from reaching the receiver. The sensor detects this change and triggers its output (e.g., “Object Detected”).
The photoelectric effect underpins the receiver’s function. When photons of IR light strike the receiver’s photodiode or phototransistor, they generate an electrical current proportional to the light intensity received. Changes in this current signal the sensor’s internal circuitry to switch its output state.
Three Pillars of Detection: Types of IR Photoelectric Sensors
Not all applications are the same, leading to distinct sensor configurations:
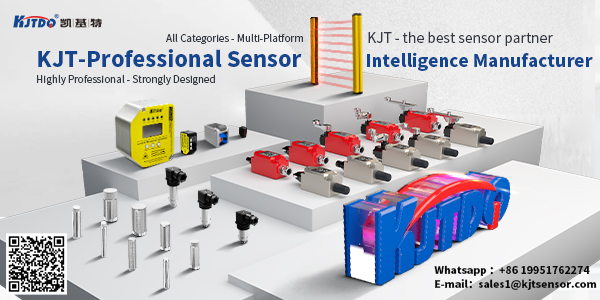
Through-Beam Sensors (Opposed Mode): These feature physically separate emitter and receiver units, positioned directly opposite each other. The emitter constantly sends an IR beam to the receiver. An object is detected when it physically blocks the beam. This design offers exceptional sensing range and reliability as it relies on the complete absence of light at the receiver. They excel in demanding environments requiring long-distance detection or handling transparent objects. Keywords: long-range detection, high reliability, opposed mode sensor.
Retroreflective Sensors: Here, the emitter and receiver are housed together. They rely on a corner-cube reflector placed opposite the sensor unit. The emitter sends an IR beam towards the reflector, which bounces the light directly back to the receiver. An object is detected when it interrupts the beam path between the sensor and the reflector, preventing the beam from returning. These sensors simplify wiring compared to through-beam types but require precise reflector alignment. Keywords: single unit, reflector target, easy installation, retroreflective photoelectric sensor.
Diffuse Reflective Sensors (Proximity Mode): Also combining emitter and receiver, diffuse sensors detect objects based on light reflected directly off the target itself. The emitter sends out IR light which strikes the target object. A portion of this light diffusely reflects back towards the receiver unit. Detection occurs based on the presence of reflected light above a threshold. Their effectiveness heavily depends on the target’s reflectivity, color, and surface texture. They offer the advantage of needing only a single mounting point but generally have shorter ranges than the other types and can be sensitive to environmental reflectors. Keywords: proximity sensing, object reflectivity, simple mounting, diffuse sensor.
Ubiquitous Impact: Where Infrared Photoelectric Sensors Shine
The versatility and non-contact nature of IR photoelectric sensors make them indispensable across a vast spectrum:
- Industrial Automation: The backbone of production lines for object counting, position verification (is the bottle cap on?), web break detection (paper/plastic sheets), level control (bin filling), robot guidance, and conveyor jam prevention. They ensure precision and continuous operation.
- Packaging Machinery: Preventing misfeeds, counting items moving into cartons, verifying label presence, detecting filled containers – all rely heavily on these sensors for packaging integrity and efficiency.
- Material Handling: Pallet detection, stack height measurement, positioning automated guided vehicles (AGVs) at stops or within lanes, and door monitoring on elevators and trucks are common applications, enhancing logistics flow.
- Consumer Applications: Powering the automatic sliding doors in retail stores and public buildings, detecting hands under faucets or paper towels in hygiene dispensers, and enabling toll booth vehicle detection.
- Security Systems: Acting as invisible beams in perimeter protection systems (security light curtains), detecting motion in restricted areas, and signaling when safes or cabinets are opened.
- Automotive: Used for functions like rain sensing (activating wipers) and anti-pinch detection on closing windows and sunroofs, contributing to safety and convenience.
The Compelling Advantages: Why Choose IR?
The widespread adoption of infrared photoelectric sensors is driven by significant benefits:
- Non-Contact Detection: Eliminates wear and tear associated with mechanical sensors, ensuring long operational life and avoiding damage to delicate targets.
- High Speed & Response: Capable of detecting objects moving at very high speeds with fast response times, essential for modern high-throughput automation.
- Versatility in Targets: Can detect a wide range of objects – metal, plastic, wood, glass, liquids – depending on the specific sensor type and configuration.
- Reliable Operation: Modern sensors are designed for robust performance in challenging industrial environments, with resistance to dust, moisture (IP ratings), vibrations, and even limited exposure to welding light (models with special filters).
- Long Sensing Ranges: Particularly through-beam and retro-reflective types can detect objects reliably over distances of several meters or more.
- Cost-Effectiveness: Offering high functionality and reliability at a competitive price point, delivering excellent value.
Navigating Limitations: Important Considerations
While powerful, optimal performance requires awareness of potential limitations:
- Environmental Factors: Ambient light interference (strong sunlight, arc welding) can disrupt operation unless sensors are shielded or use modulated IR light. Highly reflective backgrounds or steam/dust/fog can cause false triggering, especially for diffuse sensors. Choosing sensors with background suppression (BGS) diffuse technology mitigates background reflection issues.
- Target Characteristics: Transparent targets (clear glass, plastic sheets) are difficult for diffuse sensors to detect reliably and can even pass IR light, making them challenging for through-beam/retroreflective types unless specific variants are used (focusing on surface effects). Low-reflectivity targets (black rubber, matte black objects) absorb IR light, making detection difficult for diffuse sensors. Surface properties like gloss and texture significantly influence diffuse sensor performance.
- Optical Alignment: Through-beam and retroreflective sensors require precise alignment between emitter/receiver or sensor/reflector. Misalignment leads to unreliable detection.
- Limited Contour Detection: Primarily detect presence/absence. While advanced variations exist (e.g., laser distance sensors), standard photoelectrics offer minimal profile or shape recognition capabilities.
Selecting the Right Infrared Photoelectric Sensor: Key Factors
Choosing the optimal sensor demands careful analysis of the application:
- Detection Task: Presence/Absence? Counting? Position? Distance?
- Target Characteristics: Material? Size? Surface finish (color, reflectivity)? Transparency?
- Required Sensing Distance: How far does the object need to be detected from?
- Environment: Lighting conditions? Presence of dust, moisture, steam, smoke? Temperature extremes? Vibration? Potential for optical obstructions?
- Mounting Constraints: Space available? Ability to mount emitter and receiver separately?
- Output Requirements: Digital (NPN/PNP)? Analog? Relay? What voltage/current?
7.