photoelectric sensor reflector
- time:2025-07-28 08:47:30
- Click:0
Photoelectric Sensor Reflectors: The Unsung Heroes of Precision Detection
Imagine a high-speed packaging line humming along. Cartons zip down the conveyor, each needing precise positioning before sealing. Suddenly, boxes start jamming. The culprit? A photoelectric sensor failed to detect an empty slot because its emitted light beam simply vanished into thin air, unnoticed. Enter the photoelectric sensor reflector – the often-overlooked but absolutely critical partner ensuring reliable detection in countless industrial applications. Far from just a “mirror,” this component is the enabling technology that makes retroreflective sensing possible and efficient.
At its core, a photoelectric sensor reflector is a specialized optical device designed to accurately reflect light emitted by a photoelectric sensor back towards its receiver. Unlike a standard mirror, which reflects light at an angle equal to the incident angle, the most common and effective type – the corner cube reflector – utilizes the principle of total internal reflection. Constructed typically from precision optical plastic or glass featuring three mutually perpendicular reflecting surfaces, this ingenious design ensures that incoming light rays are reflected directly back along their original path, regardless of minor misalignments. This phenomenon is known as retroreflection.
This retroreflective capability is what distinguishes reflector-based systems. Retroreflective photoelectric sensors, often called “retroreflective” or “reflector” sensors, combine the emitter and receiver within a single housing. The beam travels to the reflector and bounces back. When an object interrupts this beam path, the sensor detects the loss of the reflected light. This configuration offers distinct advantages:
- Simplified Wiring and Installation: Only the sensor unit needs cabling and mounting. The passive reflector requires no power or connections, significantly reducing installation complexity, especially over longer distances.
- Cost-Effectiveness: Compared to through-beam sensors (requiring a separate emitter and receiver unit) of equivalent range, retroreflective setups are often more economical.
- Extended Range Capabilities: High-quality corner cube reflectors enable detection ranges far exceeding what diffuse sensors can achieve, often rivalling or exceeding shorter-range through-beam setups.
- Robust Detection: Retroreflection provides a strong return signal compared to the diffuse reflection utilized in proximity (diffuse) mode sensors.
Choosing the Right Reflector: Beyond the Cube
While the corner cube reflector reigns supreme for its superior performance in retroreflective sensing, other types exist, each suited for specific needs:
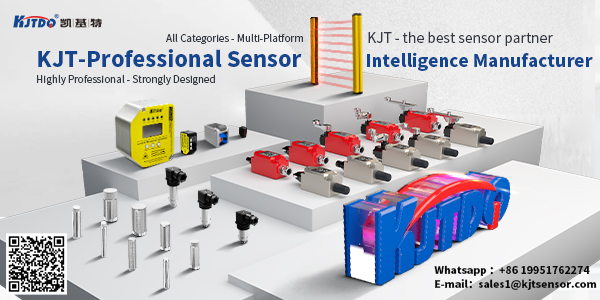
- Flat Reflectors (Mirrors): Simpler and cheaper, but significantly less efficient. They reflect light only if perfectly perpendicular to the beam. Even slight angular misalignment drastically reduces signal strength, making them highly susceptible to alignment drift and generally unsuitable for demanding industrial tasks.
- Corner Cube Arrays: Larger panels composed of multiple small corner cube elements. Ideal for creating large, reliable detection zones or when targeting moving objects of varying sizes.
- Structured Surface Reflectors: Engineered surfaces designed for specific reflection patterns, sometimes used in specialized applications.
Material and Design Matter
The effectiveness of a photoelectric sensor reflector hinges on its construction:
- Material: High-grade optical plastics (like acrylic or polycarbonate) or glass are used for their excellent light transmission properties and durability. Materials must resist yellowing, chemical exposure, and physical impacts.
- Surface Precision: The reflecting surfaces within a corner cube must be manufactured to exacting tolerances to ensure accurate retroreflection and minimal signal scattering. Imperfections directly degrade performance.
- Protective Coatings: Many reflectors feature hard coatings to resist scratches, abrasions, and environmental contaminants like dust, oil, or moisture.
- Mounting Options: Reflectors come with various mounting fixtures (brackets, adhesive pads, magnetic bases) for secure and flexible installation in diverse environments.
Installation Considerations: Maximizing Reliability
Proper installation is paramount for reflector-based sensors to function optimally:
- Alignment: While corner cubes offer forgiveness compared to flat mirrors, initial precise alignment is still crucial. Ensuring the reflector is centered and perpendicular to the sensor’s beam axis maximizes the return signal strength. Use alignment aids provided by sensor manufacturers.
- Minimizing Environmental Interference: Position the reflector to avoid background surfaces that could cause diffuse reflection back to the sensor (potentially creating a false “present” signal). Keep the optical path clear of dust, steam, or heavy vibration sources if possible.
- Secure Mounting: Ensure the reflector is firmly mounted to prevent vibration-induced misalignment over time. Even robust corner cubes have limits to their angular tolerance.
- Cleaning: Regularly inspect and clean the reflector surface. Dust, grime, or scratches can dramatically reduce signal intensity. Use appropriate cleaning methods (soft cloths, suitable cleaners) to avoid damaging optical surfaces.
Ubiquitous Applications: Where Reflectors Shine
The synergy between retroreflective photoelectric sensors and their dedicated reflectors finds application across virtually every sector:
- Manufacturing & Packaging: Object presence/absence on conveyors, counting items, detecting labels or tabs, verifying package fill level, monitorng robotic arm positions.
- Material Handling: Pallet detection, gate control, elevator positioning, detecting jams on sortation systems.
- Automotive: Monitoring assembly line components, verifying door/window closure, detecting vehicle presence in car washes or assembly stations.
- Food & Beverage: Bottle/cap presence detection, case counting, conveyor speed monitoring.
- Access Control: Safety light curtains often use reflector strips to create protected zones around machinery, detecting personnel intrusion.
- Logistics: Detecting the presence of packages on chutes, carts at loading docks, or monitoring belt movement.
Beyond the Basics: Advanced Considerations
Modern photoelectric sensor reflectors also play roles in more sophisticated setups:
- Polarized Retroreflective Sensors: These sensors use a polarizing filter over the emitter and an orthogonally oriented filter over the receiver. The retroreflector itself often incorporates a special quarter-wave filter. This combination rejects specular reflections from shiny objects nearby (like metal surfaces or plastic wrapping) that could otherwise cause false triggers. The reflector modulates the light polarization correctly for detection.
- Long-Range Detection: High-precision glass corner cube reflectors paired with powerful sensors enable reliable detection over distances of tens or even hundreds of meters, used in applications like level monitoring in large silos or vehicle detection in tolling systems.
- Harsh Environments: Reflectors constructed with robust materials and sealed designs withstand extreme temperatures, washdown conditions, UV exposure, or exposure to chemicals.
Conclusion
The photoelectric sensor reflector is far more than a simple accessory. It is the fundamental enabler of the efficient, cost-effective, and reliable retroreflective sensing mode. Its ingenious design, particularly the corner cube principle, provides unparalleled beam return stability and tolerance to misalignment compared to alternatives. Understanding its function, types, critical installation factors, and diverse applications empowers engineers and technicians to design robust sensing solutions that keep automated processes running smoothly, efficiently, and safely. In the intricate dance of light and detection within modern automation, the reflector is an indispensable partner.