retro reflective type sensor
- time:2025-07-24 04:35:44
- Click:0
Retro Reflective Sensors: The Unsung Heroes of Reliable Object Detection
Imagine a technology so elegantly simple, yet remarkably dependable, that it quietly orchestrates countless everyday interactions. It knows when your garage door is clear to close, tracks products racing down a high-speed production line, and even counts vehicles zipping past on a highway. This isn’t sci-fi; it’s the work of the retro-reflective sensor, a cornerstone of modern automation and safety systems. Its unique design offers a compelling blend of performance and practicality, making it a preferred solution in diverse industrial and commercial settings.
Unlike its counterparts – diffuse sensors that detect objects reflecting their own emitted light, or thru-beam sensors requiring separate emitter and receiver units – the retro-reflective sensor operates on a brilliantly efficient principle. It houses both the infrared (IR) or visible light emitter and the receiver (photodetector) within a single, compact housing. The magic lies opposite this housing: a specialized retro-reflector, often called a reflector target.
Here’s how it delivers consistent performance:
- Emission: The sensor emits a focused beam of light (usually IR for immunity to ambient light) towards the retro-reflector.
- Reflection Magic: The retro-reflector isn’t just a mirror. Its unique structure, typically composed of hundreds of tiny glass beads or prismatic elements, is designed to reflect incoming light directly back towards its source, regardless of the angle of incidence. This ensures a strong, predictable beam returns precisely to the sensor’s receiver.
- Detection State: When the path is clear, the receiver detects this strong reflected beam, indicating a “no object present” state for the sensor’s logic.
- Interruption & Detection: When an object breaks the beam path between the sensor head and the reflector, the light beam is blocked. The receiver no longer detects the strong reflected signal. This change triggers the sensor’s output, signaling an “object detected” state.
The Compelling Advantages of Retro-Reflective Design
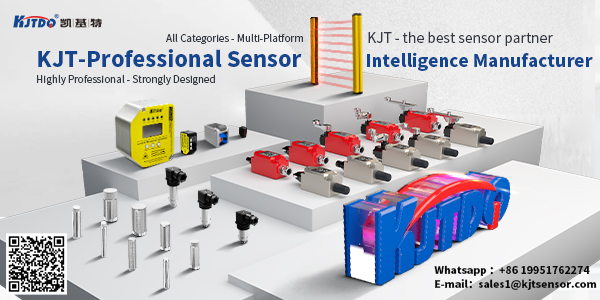
Why choose a retro-reflective type sensor over other options? Its unique configuration offers several distinct benefits that contribute to its widespread adoption:
- Simplified Installation: This is arguably the biggest advantage. Only one device needs wiring and mounting – the sensor itself. The reflector is a passive unit requiring only alignment. This drastically reduces installation time, complexity, and cost compared to thru-beam sensors, which require separate power, wiring, and precise positioning for two units (emitter and receiver).
- Cost-Effectiveness: While the reflector adds cost, the overall system cost is often lower than a thru-beam setup due to reduced cabling, mounting hardware, and installation labor. It strikes a favorable balance between diffuse sensors (low cost, shorter range) and thru-beam sensors (long range, higher cost/complexity).
- Long Sensing Ranges: Capable of reliable detection over surprisingly long distances. While not always matching the absolute maximums of the longest-throw thru-beam sensors, they offer significantly longer ranges than diffuse sensors – often reaching several meters or more – all from a single mounted point. This makes them ideal for larger machinery or conveyor setups.
- High Reliability & Signal Stability: The strong, focused return beam from the retro-reflector provides a robust signal-to-noise ratio. This makes them inherently less susceptible to interference from minor misalignment, background objects, or moderate levels of ambient light compared to diffuse sensors. They offer reliable detection even in challenging industrial environments.
- Detection of Transparent & Shiny Objects: This is a key strength. Because the sensor relies on the absence of its own beam’s reflection (rather than detecting the reflection off the object itself like a diffuse sensor), it can reliably detect clear bottles, glass panes, transparent films, or highly reflective surfaces like polished metal that often frustrate diffuse sensors. It simply sees the object blocking the path to its reflector.
- Compact Design: Integrating emitter and receiver allows for a relatively compact sensor head, often comparable in size to a robust diffuse sensor.
Where Retro-Reflective Sensors Shine: Key Applications
The blend of long range, reliability, simplified installation, and transparent object detection capability makes retro-reflective sensors indispensable across numerous sectors:
- Packaging & Material Handling: Counting bottles/cans on conveyors (especially transparent ones), palletizing/depalletizing position sensing, verifying box flap closure, web break detection on films and papers.
- Automotive Manufacturing: Position verification of components on assembly lines, robot guidance for safety curtains, end-of-line quality checks.
- Access Control & Safety: Elevator door safety beams, automated gate/door obstruction detection (garage doors, security gates), emergency stop light curtains on machinery (utilizing arrays of sensors).
- Traffic Management & Logistics: Vehicle counting and presence detection in toll booths, parking garages, or logistics hubs; container positioning on docks.
- Printing & Converting: Registration mark detection on continuous webs (paper, film), splice detection.
- Machine Tooling: Tool presence detection, workpiece positioning within machines.
Selecting and Optimizing Retro-Reflective Sensors
While remarkably versatile, ensuring optimal performance requires consideration:
- Reflector Choice: Standard reflectors are common, but specialized types exist (e.g., polarized reflectors with special filters) to combat false triggering from highly reflective surfaces behind the intended path. Selecting the right reflector for the environment is crucial. Consider size and adhesive strength for mounting.
- Sensing Range & Beam Size: Ensure the sensor’s specified range comfortably exceeds your application’s distance. Consider the minimum detectable object size relative to the beam diameter at the detection point.
- Environmental Factors: While robust, extreme conditions might necessitate specific models. Consider operating temperature, IP rating (for dust/water resistance), potential for heavy splash/spray, or intense ambient light (sunlight, welding arcs). Some sensors offer auto-teach functions to adapt to minor background changes.
- Output Configuration: Choose between digital outputs (PNP/NPN transistor) or analog outputs based on controller requirements. Light-On/Dark-On operation mode must be configured correctly.
The Enduring Value Proposition
In a world demanding ever-increasing efficiency and reliability in automation, the retro-reflective sensor continues to prove its enduring value. Its elegant solution – leveraging a dedicated reflector to bounce light efficiently back to a combined emitter/receiver unit – delivers a potent combination of long-range capability, resilience against false triggers (especially from tricky transparent or shiny objects), and significantly simplified installation logistics. While newer sensing technologies emerge, the fundamental advantages of retro-reflective sensing ensure it remains a vital and trusted workhorse on factory floors, in logistics centers, and within countless systems where reliable object detection is non-negotiable. Its quiet effectiveness underpins the smooth, safe, and automated world we increasingly rely upon.