opposed photoelectric sensor
- time:2025-07-24 00:35:50
- Click:0
Opposed Photoelectric Sensors: The Unbeatable Solution for Reliable Beam-Break Detection
Imagine a high-speed packaging line. Cartons zip down a conveyor, needing precise counting and positioning before sealing. One missed box means a costly jam or an empty package. What ensures this flawless operation, even in dusty, vibrating environments? The workhorse behind such critical detection tasks is often the robust opposed photoelectric sensor, also widely known as the through-beam sensor. This unsung hero of industrial automation delivers unmatched reliability where precision detection is non-negotiable.
Unlike its reflective cousins, an opposed photoelectric sensor fundamentally consists of two physically separate units: a dedicated light emitter and a dedicated light receiver. These units are mounted directly opposite each other, creating a distinct detection zone defined by the beam path between them. The emitter constantly projects a focused beam of light – typically infrared (IR) for its invisibility and resistance to ambient light interference, though sometimes visible red for easier alignment. This beam travels directly across the space to the receiver unit.
The core operating principle is beautifully simple and incredibly effective: detection occurs when an object physically interrupts this transmitted light beam. As long as the beam reaches the receiver unobstructed, the sensor’s output signal (often a transistor switching state) indicates “clear.” The moment an object enters the gap and blocks the beam, the receiver loses the signal, triggering an “object present” output.
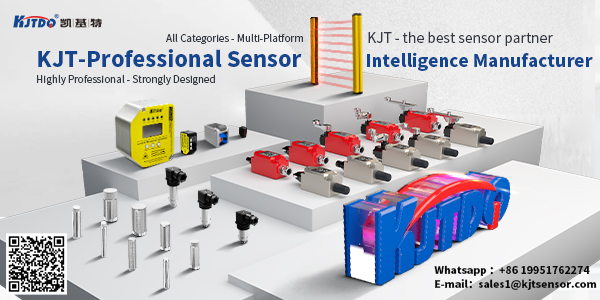
This method offers several compelling advantages that solidify its position as a go-to solution:
- Unrivaled Detection Range: Opposed sensors boast the longest sensing distances among photoelectric types. Because the light travels directly from emitter to receiver without relying on reflection, the achievable range is significantly greater, easily reaching tens of meters. This makes them ideal for monitoring large gaps, wide conveyors, or entry/exit points.
- Exceptional Reliability & Immunity: The direct beam path provides remarkable immunity to common industrial challenges:
- Target Surface: The sensor detects any opaque object, regardless of its surface color, texture, reflectivity, or material. Shiny, matte, black, white, metal, plastic – if it blocks the beam, it’s detected consistently.
- Environmental Factors: They are generally less susceptible to dust, dirt, steam, or condensation accumulating on the optical surfaces than reflective sensors (especially diffuse types). While heavy contamination can eventually block the beam, the robust signal strength provides a larger operational margin before failure compared to reflective modes.
- Ambient Light: High-quality opposed photoelectric sensors utilize modulated IR light and sophisticated receivers tuned to the specific emission frequency. This allows them to reliably reject interference from ambient plant lighting, sunlight, or other stray light sources.
- High Speed & Precision: The sharp on/off transition of the direct beam enables extremely fast response times, capable of detecting very small or rapidly moving objects passing through the beam. The detection point is also highly predictable and consistent.
- Simplicity & Ruggedness: The fundamental design is simple and mechanically robust. Units are typically housed in durable metal or high-impact plastic casings designed for demanding industrial settings, offering excellent resistance to vibration and impacts.
Key Applications Leveraging Opposed Photoelectric Strengths
Their unique strengths make through-beam sensors indispensable in numerous demanding scenarios:
- Object Presence/Absence: Verifying parts on assembly lines, detecting bottles/cans on fillers, confirming cartons on conveyors, and monitoring pallet positioning. Consistency is paramount here.
- Counting: High-speed counting of discrete items like bottles, pills, or components. High speed and reliability prevent miscounts.
- Position Verification: Ensuring machinery guards are closed before operation (safety interlocking), confirming elevator car position, or verifying gate/door closure. Failure-proof detection is critical.
- Break Detection: Monitoring webs or filaments (paper, plastic, textile, wire) for breaks. The beam break instantly signals a production fault.
- Large Area Monitoring: Securing perimeter gates, detecting vehicles at automated gate entrances, or monitoring long material transfer paths. Long range capability shines here.
Considering the Opposed Photoelectric Sensor: Factors and Variations
While exceptionally robust, deployment requires consideration:
- Wiring: Requires running cables and installing two separate units (emitter and receiver), which can be slightly more complex than single-unit sensors. Conduit or cable management is often needed.
- Alignment: Precise alignment of the emitter and receiver is crucial for reliable operation. Misalignment causes unreliable detection. Many models feature visual indicators (LEDs) or audible signals to aid alignment. Self-aligning brackets are also available.
- Object Size: Requires an opaque object large enough to completely interrupt the beam. Very small or transparent objects might not break the beam sufficiently. Selecting the right beam type matters.
- Beam Options: Beyond standard IR, variations include:
- Visible Red Beam: Easier alignment in specific situations.
- Laser Beam: For extremely precise detection of very small objects or longer ranges with a tightly focused spot.
- Fiber Optic: Uses separate emitter/receiver units connected via fiber optic cables for detection in tight spaces or extreme temperatures.
Comparison: Opposed vs. Other Photoelectric Modes
Feature |
Opposed (Through-Beam) |
Retroreflective |
Diffuse (Proximity) |
Principle |
Beam Break (Emitter + Receiver) |
Beam Break (Reflector Target) |
Light Reflection (Target itself) |
Max Range |
Very Long (10m+ easily) |
Long (up to 10m+) |
Short to Medium (cm to meters) |
Immune To: |
Target Color/Finish |
Target Color/Finish (mostly) |
Some ambient light |
Affected By: |
Alignment, Heavy Contamination |
Reflector Alignment/Dirt |
Target Color/Finish/Texture |
Complexity |
Medium (Two Units) |
Low (One Unit + Reflector) |
Low (One Unit) |
Best Suited |
Long range, Reliability, Speed |
Good range, single point mount |
Close-range, variable targets |
Environmental Resilience: Built for Industry
Modern opposed photoelectric sensors are engineered for harsh realities. Look for key ratings like IP67 or IP69K, signifying protection against dust ingress and powerful water jets. Robust housings withstand vibration and impacts common in factories and warehouses. Operating temperature ranges are wide, catering to both freezer applications and foundries.
For applications demanding the utmost in reliability, long-range capability, and immunity to challenging target surfaces and environments, the opposed photoelectric sensor remains an often unbeatable choice. Its fundamental beam-break principle, honed by decades of engineering refinement, delivers consistent, high-performance object detection that keeps automated processes running smoothly, safely, and efficiently. When downtime is not an option and reliability is paramount, the through-beam sensor stands ready.