laser photoelectric switch
- time:2025-07-24 00:10:15
- Click:0
Laser Photoelectric Switches: Precision Sensing for Demanding Automation
Imagine a beam of focused light, invisible to the naked eye, acting as an infallible sentinel on a high-speed production line. It detects the finest wires, verifies the presence of minuscule components, or ensures packaging flaps are perfectly sealed, all within milliseconds. This isn’t science fiction; it’s the everyday reality enabled by the laser photoelectric switch – a cornerstone of modern industrial automation and beyond. These sensors harness the unique properties of laser light to deliver unparalleled precision and reliability where traditional sensors falter, solving complex detection challenges with elegant simplicity.
The Core Principle: Light Interrupted, Signal Sent
At its most fundamental, a laser photoelectric switch operates on the principle of light beam interruption. It comprises two core components: an emitter and a receiver. The emitter projects a highly focused, coherent beam of laser light. The receiver sits opposite (in through-beam mode) or adjacent (in retroreflective mode), constantly monitoring the intensity of this incoming beam. When an object passes through the beam’s path, it blocks or significantly reduces the light reaching the receiver. This change triggers the switch’s output circuitry – typically changing the state of a solid-state relay (PNP/NPN) or an electromechanical relay – sending a clear electrical signal to the control system (PLC, robot, counter, etc.), indicating the object’s presence or absence.
Why Laser? The Critical Advantages Over Standard Sensors
While standard infrared (IR) photoelectric sensors are workhorses in many applications, laser photoelectric switches offer distinct advantages critical for advanced automation:
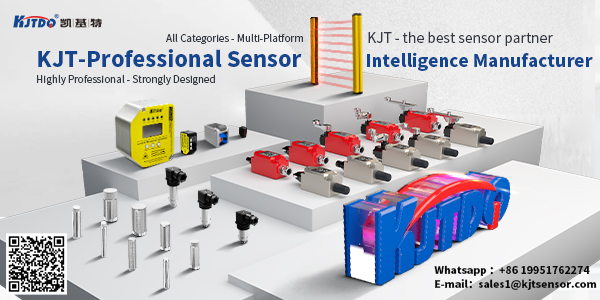
- Unmatched Precision and Small Spot Size: The inherent collimation and coherence of laser light allow it to be focused into an extremely small, intense spot. This enables the reliable detection of very small objects, thin wires, fine features on PCBs, or precise edges that diffuse IR light simply cannot resolve accurately. Imagine detecting a human hair versus a rope – the laser excels at the finer task.
- Exceptional Long-Range Sensing: Laser beams diverge very little over distance. This characteristic grants laser photoelectric sensors significantly longer effective sensing ranges compared to their IR counterparts. They can reliably detect objects tens of meters away, enabling installations where sensor positioning flexibility is limited.
- Superior Resistance to Ambient Light: The monochromatic and highly focused nature of laser light makes these switches significantly more immune to interference from ambient light sources, such as sunlight or bright factory lighting. This stability translates to fewer false triggers and more reliable operation in challenging environments.
- Enhanced Accuracy for Positional Tasks: The sharply defined beam allows for very precise positioning detection or edge finding. This is invaluable in applications like registration mark detection on printing presses, exact part placement verification, or high-accuracy cutting and alignment systems.
- Visible Spot for Alignment (Often): Many laser photoelectric switches feature a visible red laser beam. This simplifies installation and alignment dramatically compared to invisible IR beams, reducing setup time and minimizing commissioning errors. Simply align the visible dot on the target or reflector.
Key Configurations: Tailoring the Solution
Laser photoelectric switches come primarily in three main configurations to suit diverse application needs:
- Through-Beam (Emitter/Receiver Pair): The gold standard for reliability and long range. The emitter and receiver are separate units facing each other. Detection occurs when the object breaks the beam between them. Offers the highest immunity to environmental factors and the longest possible sensing distances.
- Retroreflective (Single Unit with Reflector): The emitter and receiver are housed together. A specialized reflector bounces the beam directly back to the receiver. Detection occurs when an object blocks the beam’s path to the reflector. This simplifies wiring (only one device needs connection to power/controller) but requires installing a reflector opposite the sensor. Sensing range is typically less than through-beam.
- Diffuse (Reflective) Mode: Both emitter and receiver are in one housing, detecting objects based on the reflection of the laser light off the target surface itself. No reflector is needed. While offering the simplest installation, sensing range is shorter, and performance is heavily dependent on the target object’s color, surface texture, and reflectivity.
Diverse Applications: Where Laser Precision Shines
The unique capabilities of laser sensors make them indispensable across numerous industries:
- Electronics Manufacturing: Detecting microscopic components on PCBs, verifying wire bonding, checking IC pin presence, ensuring precise placement of SMDs.
- Packaging & Labeling: Verifying package flap closure, detecting transparent films or labels, precise registration mark sensing for printing/cutting, counting small items on high-speed lines, bottle cap presence detection.
- Material Handling: Precision object counting (even small items), detecting thin carton flaps, verifying stack height, pallet presence confirmation, guiding AGVs (Automated Guided Vehicles).
- Automotive: Checking part alignment on assembly lines, verifying weld nut presence, detecting small clips or fasteners, robotic guidance and part positioning.
- Pharmaceutical & Medical Device: Ensuring precise fill levels in vials/syringes, verifying stopper presence, detecting micro-components in devices.
- Textile & Paper: Edge guiding for webs/fabrics, detecting broken threads or filaments, precise slit or cut positioning.
Selecting the Right Laser Photoelectric Switch: Key Considerations
Choosing the optimal sensor involves evaluating several factors:
- Detection Requirements: What is the smallest object? Required sensing range? Required precision (spot size)?
- Operating Environment: Dust, fog, steam, vibration, temperature extremes? Some models feature specific IP ratings (e.g., IP67, IP69K) for dust/water ingress protection.
- Target Characteristics: Color, surface finish (matte, glossy, transparent), reflectivity? This is crucial for diffuse mode sensors.
- Required Output Type: PNP, NPN, relay, analog? Voltage level compatibility with your controller?
- Electrical Connection: Cable type (PVC/PUR), connector style (M8, M12), required cable length?
- Mounting Constraints: Space limitations? Need for adjustable brackets?
- Beam Visibility Requirement: Does the application benefit from a visible spot for alignment or diagnostics?
Ensuring Optimal Performance and Longevity
Once installed, proper maintenance ensures consistent operation:
- Regular Cleaning: Keep the emitter and receiver lenses clean. Dust, dirt, or oil film can attenuate the beam. Use appropriate cleaning materials (e.g., lens wipes).
- Secure Mounting: Ensure sensors and reflectors are firmly mounted and protected from vibration or accidental impact. Recheck alignment periodically, especially after maintenance in the area.
- Environmental Protection: Verify seals are intact. Use protective housings if exposed to significant washdown or abrasive dust.
- Visual Inspection: Periodically check the visible beam (if applicable) for alignment and intensity.
The Future is Focused
As automation demands ever-greater precision, speed, and reliability, the laser photoelectric switch remains a vital tool. Its ability to deliver micrometer-level accuracy over substantial distances, coupled with robust performance in diverse environments, makes it irreplaceable for countless critical detection and positioning tasks. From safeguarding delicate electronics assembly to ensuring the perfect seal on a food package, the focused power of laser light continues to drive efficiency and quality in the modern industrial landscape. Understanding their capabilities and selecting the right configuration empowers engineers to unlock new levels of performance and solve detection challenges that were once considered impossible.