industrial photoelectric sensor
- time:2025-07-23 16:28:33
- Click:0
The Invisible Workhorses: How Industrial Photoelectric Sensors Power Modern Automation
Ever wondered how a complex manufacturing line flawlessly detects the presence, absence, position, or even the color of thousands of items per minute, tirelessly, day and night? Look no further than the silent, ubiquitous heroes of automation: industrial photoelectric sensors. These remarkable devices form the fundamental eyes of countless automated systems, translating light into critical control signals with speed and precision unmatched by human operators. Understanding their function and capabilities is key to unlocking efficiency and reliability in modern industrial environments.
At its core, an industrial photoelectric sensor operates on a beautifully simple principle: it uses light, typically in the infrared, visible red, or laser spectrum, to detect objects. A light emitter sends out a beam. A receiver then monitors this light. When an object interrupts or alters this beam’s path, the sensor triggers an electrical signal. This basic interaction belies the sophisticated engineering that allows these sensors to perform reliably in harsh, demanding industrial settings, enduring vibration, temperature extremes, dust, moisture, and electromagnetic interference.
Their diversity stems primarily from three distinct operating modes, each tailored for specific application challenges:
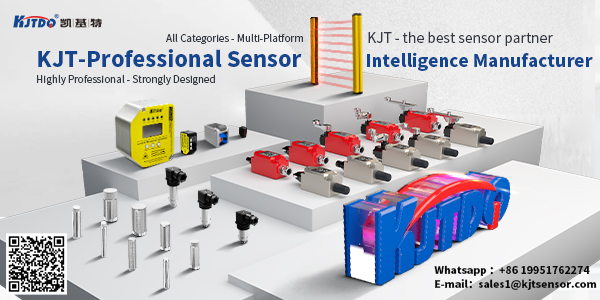
- Through-Beam Sensors (Sender/Receiver Pair): The most robust and longest-range option. The emitter and receiver are separate units installed opposite each other. Detection occurs when an object breaks the beam path between them. Ideal for long-distance detection (up to 60m or more), detecting small objects that partially block the beam, or in environments with heavy airborne contamination. Think of detecting small components on high-speed conveyors or verifying pallet presence at warehouse dock doors.
- Retroreflective Sensors: Combine the emitter and receiver in one housing. A special reflector, typically a prismatic type, bounces the emitted light beam back to the receiver. Detection happens when an object interrupts this reflected beam. Offers simpler installation than through-beam (only one device to mount and wire, plus the reflector) and good range (up to 10-15m). Widely used for presence detection on packaging lines, detecting vehicles at gates, or verifying flap openings on cartons. Care is needed with highly reflective target objects that might mimic the reflector.
- Diffuse (Proximity) Sensors: Emitter and receiver are also housed together, but they detect light reflected directly off the target object itself. Detection occurs when enough light bounces back from the object. Simplest installation as no separate reflector is needed, ideal for close-range detection where object access is limited. Used extensively for detecting objects on conveyors, counting bottles, or verifying part placement in assembly cells. Performance is heavily influenced by the object’s color, reflectivity, and surface texture – dark matte objects require specific sensors designed for “black object detection,” often leveraging red light or background suppression technology.
Within these modes, specialized technologies further enhance capability:
- Background Suppression (BGS): Critically important for diffuse sensors. This technology allows the sensor to detect objects only within a specific, limited distance range, ignoring the background. This makes detection reliable regardless of the object’s color or reflectivity against potentially interfering backgrounds. Essential for applications like detecting dark objects on a dark conveyor belt.
- Foreground Suppression (FGS): The opposite of BGS, ignoring close objects and focusing detection on objects farther away. Less common but useful in niche applications.
- Fixed-Field and Adjustable-Field Sensing: Determines how precisely the sensor defines its detection zone.
- Laser Sensors: Use a focused laser beam. Excels at detecting very small objects or achieving precise position detection at longer ranges compared to standard LED light sources. Common in electronics assembly or precision alignment tasks.
The advantages driving the widespread adoption of industrial photoelectric sensors are compelling:
- Non-Contact Detection: Eliminates mechanical wear and tear, ensuring long service life and reliable operation without physical impact on the target.
- High Speed: Capable of detecting objects moving at extremely high speeds, critical for modern high-throughput production lines. Response times are typically in microseconds.
- Extended Sensing Ranges: From a few millimeters up to 60+ meters, offering incredible flexibility for diverse spatial layouts.
- Versatility: Capable of detecting virtually any material – metal, plastic, wood, glass, liquid levels (transparent or opaque) – provided the appropriate sensor type and technology are selected.
- Robustness: Engineered to IP67, IP68, or IP69K ingress protection ratings, resistant to shock, vibration, washdowns, and harsh chemicals common in factories, food processing, and outdoor environments.
- Relatively Low Cost: Provide exceptional value and return on investment considering their critical role in automation uptime and efficiency.
Where do these sensors make their impact? Their applications span the entire industrial landscape:
- Object Detection & Positioning: Confirming parts are present and correctly positioned on conveyors, pallets, or in assembly fixtures. Fundamental for process verification.
- Counting & Sorting: Accurately tallying bottles, cans, packages, or components moving down a line. Sorting based on presence/absence or even color recognition capabilities.
- Level Control: Monitoring fill levels in bins, tanks, or bottles, crucial for preventing overfills or running dry.
- Web & Edge Guiding: Ensuring continuous materials like paper, plastic film, or textiles stay aligned during processing.
- Security & Access Control: Detecting personnel in restricted zones or vehicles at gates/barriers.
- Robotics: Providing precise feedback on object location for pick-and-place robots.
- Packaging: Verifying case flaps are closed, labels are present, or products are correctly oriented.
Selecting the right industrial photoelectric sensor requires careful consideration of several factors:
- Detection Task: What exactly needs detecting (presence, absence, position, distance, color)? What is the target size?
- Target Properties: Material, color, surface finish (shiny, matte), transparency?
- Operating Environment: Dust, moisture, temperature, vibration, potential for dirt buildup on the lens?
- Required Sensing Range: How far away is the target?
- Mounting Constraints: Available space? Access to both sides of the target?
- Output Requirements: What type of signal does the controller need (PNP, NPN, analog, IO-Link)?
- Special Features Needed: Background suppression? Resistance to ambient light? High-speed response?
By acting as the reliable, high-speed “eyes” of machinery, industrial photoelectric sensors are indispensable components driving the efficiency, safety, and quality inherent in modern automated manufacturing and logistics. Their evolution continues, with trends like integrated intelligence (IO-Link for parameterization and diagnostics), enhanced resistance to challenging environmental factors, and even more compact designs pushing the boundaries of what automation can achieve. Choosing and deploying the appropriate photoelectric sensing solution remains a fundamental step in building robust and productive automation systems.