caster photoelectric switch
- time:2025-07-23 15:42:38
- Click:0
Unlocking Industrial Mobility: The Power of the Caster Photoelectric Switch
Imagine a bustling factory floor. Automated guided vehicles (AGVs) glide silently between workstations, conveyor lines hum, and material handling carts dart to and fro. At the heart of this dynamic movement lie countless casters – the unsung heroes enabling smooth, multidirectional transport of heavy loads. But ensuring these mobile systems operate safely and efficiently requires precise sensing. Enter the Caster Photoelectric Switch, a specialized sensor engineered to monitor and control motion where wheels meet the ground, adding an indispensable layer of intelligence to industrial mobility.
Casters, whether rigid for straight-line travel or swiveling for maneuverability, are fundamental components in material handling equipment, carts, dollies, and AGVs. Their primary function is to facilitate movement. However, knowing when that movement happens, if something is obstructing it, or precisely where a caster-equipped unit is positioned is critical for automation, safety protocols, and operational flow.
This is where the photoelectric switch component becomes pivotal. A photoelectric switch, often called a photo eye, operates on the principle of light transmission. It typically consists of an emitter (light source, commonly infrared LED) and a receiver (light-sensitive component). When the emitted light beam is either interrupted by an object (in the case of “through-beam” mode) or reflected back to the receiver (in “retroreflective” or “diffuse” modes), the switch triggers an electrical signal. This signal can then be used to count objects, detect presence or absence, control machinery, or activate safety stops.
The term Caster Photoelectric Switch specifically denotes a photoelectric sensor designed with the unique challenges of caster monitoring in mind:
- Compact Design: Casters are often confined spaces. These sensors are engineered to be small and low-profile, fitting seamlessly into or near the caster assembly without impeding rotation or movement. Mounting flexibility is key.
- Robust Construction: Industrial environments are tough. Caster switches must withstand vibration from rolling over uneven surfaces, shocks from impacts, exposure to dust, dirt, oil, and moisture (often rated IP67 or higher), and potentially significant temperature fluctuations. Stainless steel housings or rugged polymers are common.
- Reliable Detection: Casters move constantly, and the sensing target (often the ground surface, a wheel spoke, or a physical flag attached to the caster) can be inconsistent. These switches employ sophisticated optics and electronics to provide consistent, reliable detection despite harsh operating conditions and variable backgrounds.
- Sensing Modes: Depending on the application:
- Detection of Caster Rotation: Mounting a sensor to detect a flag on a wheel hub can confirm the caster is actually rotating and hasn’t seized, preventing equipment damage or drag.
- Load Presence: Verifying if a cart or dolly is physically present at a docking station or conveyor interface.
- Position Verification: Ensuring a mobile unit or AGV with casters is correctly aligned or positioned before initiating another process.
- Obstacle Detection Near Wheels: Sensing objects immediately adjacent to the caster path to prevent collisions or jams.
Why Choose Photoelectric for Casters?
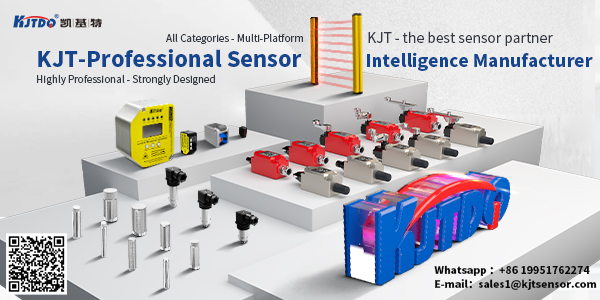
Compared to mechanical limit switches, the caster photoelectric switch offers distinct advantages crucial for modern, automated environments:
- Non-Contact Sensing: There’s no physical force applied to the target. This eliminates wear and tear on the sensor and the object being detected, leading to vastly superior longevity and maintenance-free operation in continuous use scenarios. Mechanical switches wear out quickly under the constant movement and vibration inherent to casters.
- High Speed & Accuracy: Light travels fast! Photoelectric switches can detect incredibly rapid movements and minute objects with exceptional precision, far exceeding the capabilities of mechanical contacts. This is vital for high-speed AGVs or precise positioning.
- Versatility: Easily adaptable to different targets (metal, plastic, wood, even liquid levels) and backgrounds by selecting the appropriate sensing mode (through-beam, retroreflective, diffuse).
- Consistency: Provides stable, repeatable signals without the “bounce” or signal degradation common in mechanical switches after wear.
Key Applications Lighting Up Industry
The integration of caster photoelectric switches unlocks efficiency and safety across numerous sectors:
- Automated Guided Vehicles (AGVs/AMRs): Essential for confirming wheel rotation on each drive/steer caster, preventing motor burnout if a wheel jams. Also used for precise docking control and obstacle detection near ground level.
- Conveyor Systems: Monitoring the presence and position of carts or dollies at transfer points, initiating/stopping conveyor segments based on caster position.
- Material Handling Carts & Dollies: Automating charging station engagement when a cart docks, inventory tracking via position detection, or ensuring carts are properly seated on lifts or turntables.
- Assembly Lines: Verifying that mobile workstations or kitting carts are in the correct position before commencing assembly operations.
- Packaging & Logistics: Controlling the flow of wheeled totes or bins on sortation systems and ensuring safe loading/unloading sequences.
- Automotive Manufacturing: Precise positioning of large, caster-mounted jigs or fixtures within assembly cells.
Selecting the Right Caster Photoelectric Switch: What Matters
Choosing the optimal sensor requires careful consideration:
- Sensing Mode: What needs detection? (Rotation, position, presence, obstacle?) What’s the target? (Ground, flag, wheel spoke?).
- Detection Range: Distance between sensor and target.
- Environmental Factors: IP rating for dust/water resistance, temperature range, exposure to chemicals or oils.
- Electrical Output: Required signal type (NPN/PNP, NO/NC) and voltage compatibility with your control system.
- Housing & Mounting: Size constraints, material (metal vs. plastic), required mounting configuration (bracket, threaded barrel).
- Special Features: Built-in timers, sensitivity adjustment, synchronization options (to avoid crosstalk if multiple sensors are nearby).
Maximizing Reliability: Installation Insights
For a caster photoelectric switch to perform optimally, installation is critical:
- Secure Mounting: Ensure the sensor is rigidly fixed to prevent vibration-induced misalignment. Use appropriate brackets.
- Precise Alignment: Especially crucial for through-beam or retroreflective modes. Even slight misalignment dramatically reduces sensing range and reliability. Take the time to align carefully.
- Clean Optics: Protect sensors from excessive splashing if possible, and periodically clean the lens cover to prevent false signals caused by dust or grime buildup. Routine inspection is wise.
- Avoid Obstructive Cabling: Ensure sensor cables are routed away from moving parts like the caster wheel itself to prevent snagging or damage. Strain relief is important.
The Future Rolls On
As industrial automation deepens its reliance on mobile platforms and flexible material handling, the role of precise sensing at the point of movement becomes ever more critical. The caster photoelectric switch represents a sophisticated solution, merging the fundamental mechanics of wheels with the precision, reliability, and intelligence of modern optical sensing. By providing non-contact confirmation of rotation, position, and presence right where mobility begins, these compact, rugged sensors are indispensable components in building smarter, safer, and more efficient automated environments. They are the silent sentinels ensuring that wheels don’t just turn, but turn