m12 photoelectric sensor
- time:2025-07-23 14:56:51
- Click:0
M12 Photoelectric Sensors: The Compact Powerhouses Driving Industrial Automation
Imagine a bustling automotive assembly line where sensors blink like vigilant sentinels, ensuring robots place components perfectly and vehicles glide seamlessly from station to station. At the heart of this orchestrated precision often lies a humble yet critical component: the M12 photoelectric sensor. More than just a component, this compact device embodies the relentless drive towards efficiency and reliability in modern manufacturing. Its standardized size belies its vast capabilities, forming the sensory backbone of countless automated processes where accuracy isn’t just desired – it’s demanded.
Why M12? The Standard That Powers Precision
The designation “M12” isn’t merely a model number; it refers to an international standard for the sensor’s cylindrical threaded housing, measuring precisely 12 millimeters in diameter. This standardization is revolutionary. It guarantees interchangeability across a vast ecosystem of sensors and mounting accessories from numerous manufacturers. For engineers and maintenance technicians, this means simplified installation, effortless replacement, and streamlined inventory management. The robust all-metal or high-grade plastic housings typical of M12 sensors provide excellent resistance to vibration and shock, common adversaries in industrial settings. Critically, the secure M12 threaded connection, often complemented by industry-standard M12 connectors, ensures reliable electrical contact even in demanding environments, preventing costly signal interruptions.
Seeing the Light: Core Functionality Simplified
At its essence, a photoelectric sensor detects the presence, absence, or distance of an object using light. An emitter projects a light beam (typically infrared, visible red, or laser), while a receiver detects changes in this beam. The magic happens when an object interferes:
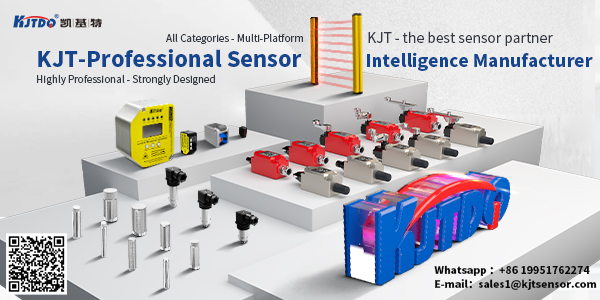
- Blocks the Beam: Used for object detection (e.g., counting bottles on a conveyor).
- Reflects the Beam Back: Detects objects based on their reflectivity (e.g., sensing labels on packaging).
- Enters a Defined Detection Zone: Triggers based on proximity (common in diffuse models).
This fundamental principle enables non-contact detection, eliminating wear and tear associated with mechanical switches and providing incredibly fast response times – often measured in microseconds.
Navigating the Types: Choosing the Right M12 Sensor
Selecting the optimal M12 photoelectric sensor hinges on the specific application challenge. The three primary variants offer distinct advantages:
- Through-Beam Sensors (Sender/Receiver Pair): Considered the most reliable and longest-range option. The emitter and receiver are separate units facing each other. Detection occurs when an object breaks the beam between them. Ideal for:
- Detecting objects with varying surface properties (transparent, dark, shiny).
- Applications requiring maximum sensing distances (up to 10s of meters).
- Environments with dust or light interference (the focused beam is less affected).
- Retroreflective Sensors: Combine emitter and receiver in one compact M12 housing. They rely on a dedicated reflector placed opposite. The sensor detects an object when it interrupts the beam bouncing back from the reflector. Key strengths:
- Simplified wiring (only one sensor unit needs cabling).
- Good range performance, often surpassing diffuse sensors.
- Consistent detection of objects entering the beam path.
- Diffuse (Proximity) Sensors: House the emitter and receiver together in a single M12 unit. They detect objects when light emitted reflects directly back from the target’s surface. Advantages include:
- Simplest mechanical setup – only one device to mount, no reflector needed.
- Ideal for detecting objects at relatively close ranges within the sensor’s field of view.
- High suitability for installation in confined spaces thanks to the compact M12 form factor. Performance can be influenced by the target’s color, material, and surface finish.
Beyond Size: Key Features Defining Performance
While the M12 form factor is crucial, the sensor’s internal capabilities are equally vital:
- Robust Environmental Protection: The IP67 or IP69K ratings are standard-bearers for M12 photoelectric sensors. This signifies exceptional resistance against dust ingress and protection against the effects of immersion in water (IP67) or even high-pressure, high-temperature washdowns (IP69K), making them indispensable in food processing, pharmaceuticals, and harsh outdoor settings.
- Output Flexibility: NPN and PNP transistor outputs are the industry mainstays, allowing seamless integration with virtually any Programmable Logic Controller (PLC) or machine control system. Some advanced models offer analog outputs for distance measurement or configurable IO-Link digital communication for enhanced diagnostics and parameterization.
- Light Sources & Range: Infrared (IR) is the most common, offering good range and invisibility to the human eye. Visible Red Light aids in precise alignment during setup. Laser variants provide extremely small, focused beams for detecting minute objects or achieving high positional accuracy.
- Response Time & Switching Frequency: Measured in milliseconds or microseconds, this determines how fast the sensor can detect an object passing by. High-speed models are critical for applications like bottling lines or electronic component placement.
- Specialized Variants: Background Suppression (BGS) sensors excel at detecting objects close to a background surface. Contrast Sensors differentiate based on color or mark contrast, vital in printing and packaging. Fork Sensors (U-Shaped) integrate emitter and receiver in a rigid fork, ideal for small part detection.
Where Compact Vigilance Matters: Diverse Applications
The versatility of the M12 photoelectric sensor ensures its presence throughout the industrial landscape:
- Packaging & Bottling: Precision bottle/can counting, cap presence verification, fill level monitoring (using thru-beam or diffuse), label detection.
- Material Handling & Logistics: Detecting parcels on conveyors, confirming pallet presence, controlling gate operations at the end of conveyor runs, stacking height verification.
- Automotive Manufacturing: Ensuring component presence in robots, verifying assembly steps (e.g., door panel placement), detecting vehicles entering wash stations.
- Food & Beverage: Position sensing on production lines, detecting toppings on pizzas, confirming packaging film feed (often requiring high IP69K ratings for washdown).
- Electronics: Verifying component placement on PCBs, detecting miniature parts flowing in tubes, confirming tray loading/unloading.
M12 photoelectric sensors, with their potent combination of robust construction, standardized interchangeability, and diverse sensing capabilities, are far more than mere components. They are the essential eyes of automated systems, providing the reliable detection data that modern processes fundamentally depend upon. Their compact M12 form factor makes them the ideal solution for space-constrained applications where performance cannot be compromised. From ensuring precision on high-speed assembly lines to operating reliably under the spray of a washdown hose, these sensors deliver the consistent, non-contact detection that underpins productivity, quality control, and seamless operation across countless industries. In the intricate dance of industrial automation, the M12 photoelectric sensor is an indispensable, continuously vigilant partner.