diffuse photoelectric sensor
- time:2025-07-23 12:19:08
- Click:0
Diffuse Photoelectric Sensors: Your Essential Guide to Reliable Proximity Detection
Introduction: The Unsung Eyes of Automation
In the intricate dance of modern manufacturing and automation, countless processes rely on one fundamental question: “Is the object there?” Detecting presence, absence, position, or count forms the bedrock of control systems. While various sensor technologies vie for attention, the diffuse photoelectric sensor stands out as a remarkably versatile and widely adopted solution for countless proximity detection challenges. For engineers, technicians, and system designers, understanding how these sensors work and where they excel is crucial for building robust and efficient automation. Let’s delve into the world of diffuse photoelectric sensing.
How Does a Diffuse Photoelectric Sensor Actually Work?
The core principle is surprisingly elegant. A diffuse photoelectric sensor houses both an infrared (IR) or visible light emitter and a light receiver within a single compact housing. Unlike its cousins – the thru-beam and retro-reflective sensors – it doesn’t require a separate reflector or receiver unit positioned opposite the emitter.
Here’s the step-by-step breakdown:
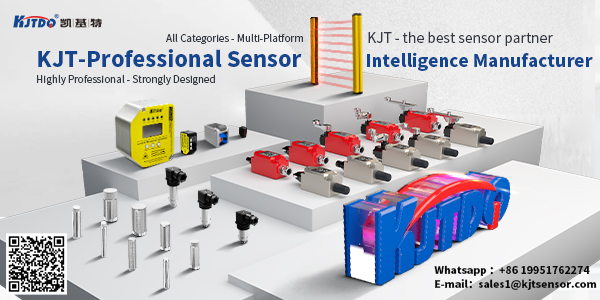
- Emission: The sensor’s built-in emitter LED projects a beam of light (typically infrared for immunity to ambient light interference, though visible red or laser versions exist) towards the target area.
- Reflection: When a physical object enters the sensor’s detection zone, this light beam strikes the object’s surface.
- Diffuse Reflection: Crucially, the light scatters diffusely in many directions off the object’s surface. This phenomenon, diffuse reflection, happens on most non-shiny, non-mirror-like surfaces.
- Reception: A fraction of this diffusely scattered light travels back towards the sensor’s housing.
- Detection: The built-in photoelectric receiver (like a phototransistor or photodiode) detects this returning light energy.
- Signal Processing: The sensor’s internal circuitry analyzes the strength of the received light signal. If the intensity surpasses a pre-set threshold (which can often be adjusted via potentiometer or teach-in functionality), the sensor’s output switches state (e.g., from OFF to ON).
- Output: This change in output state signals to the connected control system (PLC, robot, etc.) that an object has been detected within the defined sensing range.
Key Advantages: Why Choose Diffuse Sensing?
The integrated emitter-receiver design and reliance on diffuse reflection unlock distinct benefits:
- Simplified Installation: Only one device needs to be mounted and wired on one side of the detection point. There’s no complex alignment with a separate reflector or receiver across the path. This translates to significantly faster setup and reduced installation costs.
- Compact Design & Space Savings: The single-unit form factor allows installation in tight spaces where fitting both an emitter and a receiver unit would be impossible.
- Non-Contact Operation: Like all photoelectric sensors, it detects objects without physical touch, eliminating wear and tear and allowing detection of fragile items.
- Material Versatility: Capable of detecting a surprisingly wide range of materials – cardboard, wood, plastic, metal (matte finishes work best), glass (often with specialized variants), bottles, labels, biological products – essentially any surface that scatters light to some degree.
- Cost-Effectiveness: Generally, they offer a lower unit cost compared to thru-beam setups requiring two separate devices.
Navigating Limitations: Awareness is Key
While powerful, diffuse sensors do have inherent constraints to consider:
- Sensing Distance: This is the primary limitation. Detection range is typically shorter than thru-beam or retro-reflective sensors. Maximum ranges vary greatly (millimeters to several meters) depending on the sensor’s power, lens design, and especially the target’s size, color, and reflectivity. Dark, matte, or highly absorbent objects reflect less light, drastically reducing achievable range.
- Color and Surface Dependence: Performance is directly tied to how well the target reflects light back to the receiver. Highly reflective targets or very dark targets can cause inconsistent detection or require careful threshold setting. A shiny black plastic bottle might be harder to detect reliably than a white cardboard box at the same distance.
- Background Interference: Objects or surfaces located behind the intended target can also reflect light back to the receiver. If bright enough, this background reflection can trick the sensor into detecting an object even when the target isn’t present. This is particularly problematic if the background is closer than the target or highly reflective.
The Solution: Background Suppression (BGS)
To combat the critical challenge of background interference, many modern diffuse sensors employ Background Suppression (BGS) technology. BGS sensors are cleverly designed to only recognize light reflected from objects within a very specific, pre-defined distance range.
- Triangulation Principle: BGS sensors often use triangulation. The emitted light beam and the receiver’s optical path are angled differently.
- Focus on Proximity: This geometry ensures that only light reflected from objects within the chosen “spot” distance reaches the receiver optimally. Light reflected from surfaces beyond this focal point strikes the receiver at a different angle and is effectively ignored.
- Enhanced Reliability: As a result, BGS sensors reject background reflections, providing much more reliable detection of the target object, unaffected by what might be behind it. This makes BGS a highly recommended feature for most diffuse sensor applications.
Diffuse vs. Other Photoelectric Modes: Choosing the Right Tool
Understanding where diffuse fits in the photoelectric family is essential:
- Thru-Beam (Opposed Mode): Emitter and receiver are separate units facing each other. Detection occurs when the target breaks the beam. Offers the longest sensing ranges and highest immunity to target color/surface. Drawbacks: Requires mounting two separate units, precise alignment needed, higher cost per detection point.
- Retro-Reflective: Emitter and receiver are in one unit, using a special reflector placed opposite. The reflector bounces the light beam directly back. Detection occurs when the target breaks the beam. Offers longer ranges than diffuse and only requires one sensor unit (plus reflector). Drawback: Shiny targets can sometimes reflect the beam back without breaking it (“mirror effect”), causing false negatives.
- Diffuse (Proximity Mode): Single unit, detects light reflected directly off the target. Pros: Simplest installation, compact, cost-effective for shorter ranges. Cons: Shortest practical range, susceptible to target reflectivity and background interference (mitigated by BGS).
Where Diffuse Sensors Shine: Key Application Areas
Thanks to their simplicity and versatility, diffuse sensors are ubiquitous:
- Object Detection on Conveyors: Detecting boxes, totes, bottles, parts on moving lines. BGS variants excel at ignoring the conveyor belt background.
- Presence/Absence Verification: Confirming a part is present in a