photo electric sensor
- time:2025-07-23 12:14:00
- Click:0
The Essential Guide to Photoelectric Sensors: How Light Powers Modern Automation
Ever wondered how a factory line knows a bottle is present for filling, how an automatic door opens seamlessly, or how a conveyor belt stops when an object jams? The silent hero behind countless automated processes is often the photoelectric sensor. These versatile devices, fundamental to modern industrial automation and beyond, use light beams to detect the presence, absence, or distance of objects with remarkable precision. Understanding their operation, types, and applications is key to unlocking efficient and reliable sensing solutions.
The Science Behind the Beam: How Photoelectric Sensors Work
At its core, a photoelectric sensor operates on a simple yet powerful principle: it uses a light emitter (usually an LED or laser diode) to project a beam of light towards a receiver (a phototransistor or photodiode). The receiver constantly monitors the characteristics of this received light. Detection occurs when the target object interacts with the light beam, causing a measurable change. This interaction can manifest in several ways:
- Interruption: The object physically blocks the light beam from reaching the receiver (used in through-beam sensors).
- Reflection: The object reflects the emitted light back towards the receiver (used in retro-reflective and diffuse reflective sensors).
- Deflection/Scattering: The object deflects or scatters the light beam, altering the amount or angle of light reaching the receiver.
The sensor’s internal circuitry detects this change in the light signal received and triggers an electronic output signal (ON/OFF or more complex analog/digital outputs), communicating the object’s status to a control system like a PLC.
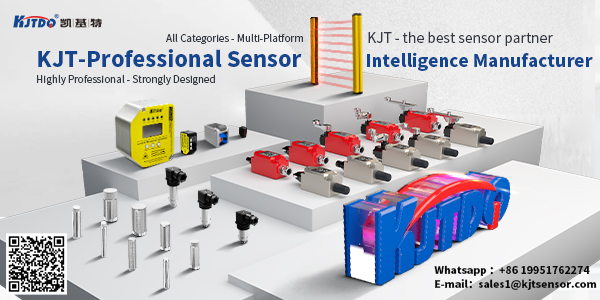
Common Photoelectric Sensor Types: Choosing the Right Tool
Not all photoelectric sensors are created equal. Different operational principles suit varying application needs. The three primary configurations dominate the landscape:
- Through-Beam Sensors (Sender/Receiver Pair):
- Principle: Separate emitter and receiver units face each other. The emitter projects a continuous beam directly to the receiver. Detection occurs when an object interrupts this beam.
- Key Advantages: Offers the longest sensing ranges (often tens of meters). Very reliable and immune to target object color, surface finish, or reflectivity. High immunity to ambient light interference.
- Key Considerations: Requires mounting two separate components, aligning them precisely, and ensuring wiring to both sides. Can be bulkier and more expensive than other types.
- Retro-Reflective Sensors:
- Principle: A single housing contains both the emitter and receiver. It projects a beam towards a specialized reflector (corner-cube or tape). The reflector sends the light beam directly back to the receiver within the same housing. Detection occurs when an object interrupts this return beam path.
- Key Advantages: Easier installation than through-beam as only one unit and the reflector need mounting (though alignment is still important). Good sensing range (typically meters). Generally immune to the object’s color or surface finish, as it relies on beam interruption.
- Key Considerations: Performance can be affected if highly reflective objects enter the sensing field at certain angles (potentially mimicking the reflector). Requires keeping the reflector clean. Sensing range less than through-beam.
- Diffuse Reflective Sensors (Proximity Mode):
- Principle: Emitter and receiver are housed together, but the sensor relies on light reflecting directly off the target object itself. The emitted light hits the object, scatters, and some portion reflects back to the receiver.
- Key Advantages: Simplest installation – only one device needs mounting; no separate reflector required. Ideal for detecting objects on the same side.
- Key Considerations: Sensing range is typically shorter than the other types. Performance is highly dependent on the target object’s size, color, reflectivity, and surface texture (dark or matte objects are harder to detect). More susceptible to ambient light interference. Background suppression (BGS) variants mitigate some issues by focusing only on objects within a specific distance.
Where Light Meets Application: Ubiquitous Uses
The versatility of photoelectric sensors makes them indispensable across countless sectors:
- Manufacturing & Packaging: Detecting product presence/absence on conveyors, counting items, verifying fill levels in bottles/cans, checking label presence, controlling robotic assembly arms, jam detection.
- Material Handling: Controlling automatic doors and gates, detecting pallets in warehouses, positioning lifts and elevators, verifying package dimensions.
- Automotive: Checking part placement on assembly lines, verifying component assembly (e.g., windshield in place), monitoring paint booth entry/exit, controlling robotic welding paths.
- Food & Beverage: Ensuring proper container filling levels, detecting lids or caps, verifying label application, detecting broken containers on high-speed lines.
- Building Automation: Controlling lighting based on occupancy, detecting people for security systems, managing HVAC flow based on room presence.
Why Choose Photoelectric Sensing? Key Advantages
Photoelectric sensors offer compelling benefits that drive their widespread adoption:
- Non-Contact Sensing: Objects are detected without physical touch, eliminating wear and tear on both the sensor and the target. This ensures long operational life and avoids damaging delicate objects.
- Fast Response Times: Light travels incredibly fast, enabling photoelectric sensors to detect objects at high speeds, crucial for modern, rapid production lines.
- Long Sensing Ranges: Especially through-beam and retro-reflective types can detect objects meters away, offering greater flexibility in machine design.
- Versatility: Available in numerous form factors, beam types (visible, infrared, laser), output configurations, and specialized variants (e.g., fiber optic amplified sensors, color sensors, contrast sensors) to tackle diverse challenges.
- Contactless Detection of Various Objects: Capable of detecting nearly any solid object, regardless of material (metal, plastic, wood, glass, cardboard, liquid surfaces), provided the appropriate sensor type is chosen for the specific conditions.
Selecting the Ideal Photoelectric Sensor: Key Factors
Choosing the right photoelectric sensor for your application involves carefully considering several parameters:
- Application & Object: What are you detecting? (Size, shape, color, material, surface finish). How does it need to be detected? (Presence, absence, distance).
- Required Sensing Range: How far away is the object from the sensor?
- Environment: Consider factors like ambient light levels, dust, mist, fog, temperature extremes, and potential for mechanical impact or vibration. IP ratings indicate environmental protection level.
- Mounting Constraints: Available space and orientation for mounting the sensor (and reflector, if needed).
- Required Output Type: Simple digital (PNP/NPN)? Analog output for distance measurement? IO-Link for smart sensor capabilities?
- Target Properties: As mentioned, color, reflectivity, and surface texture are critical, especially for diffuse sensors. Contrast sensors are specifically designed for detecting differences.
- Speed: How fast is the object moving? Ensure the sensor’s response time is adequate.
By carefully evaluating these factors, you can confidently select the photoelectric sensor type that delivers reliable, efficient, and cost-effective object detection for your specific needs, solidifying its role as a cornerstone of automation efficiency.