inductive pulse sensor
- time:2025-07-10 01:52:22
- Click:0
Here is the SEO-optimized article on “Inductive Pulse Sensor” following all your requirements:
The Invisible Guardian: How Inductive Pulse Sensors Revolutionize Modern Automation
Imagine the precise, smooth rotation of a robotic arm on a factory floor, the reliable ticking over of an engine crankshaft monitored for performance, or the unwavering accuracy counting products zipping down a high-speed conveyor line. Behind these critical movements, often unseen yet indispensable, lies a workhorse of industrial sensing: the inductive pulse sensor. More than just a component, this robust device is a fundamental enabler of the feedback loops that keep automated systems running safely and efficiently.
Understanding the Core Principle: Electromagnetic Induction
At the heart of every inductive pulse sensor lies the fundamental principle of electromagnetic induction, famously discovered by Michael Faraday. Simply put, when a magnetic field near a coil of wire changes in strength, it induces a voltage (or electromotive force) within that coil.
An inductive proximity sensor leverages this phenomenon specifically for detecting the presence or absence of metallic objects within its sensing range without physical contact. However, the inductive pulse sensor takes this a step further. It is specifically designed to detect changes – specifically the passing or motion of metallic targets, translating this movement into a series of discrete electrical pulses.
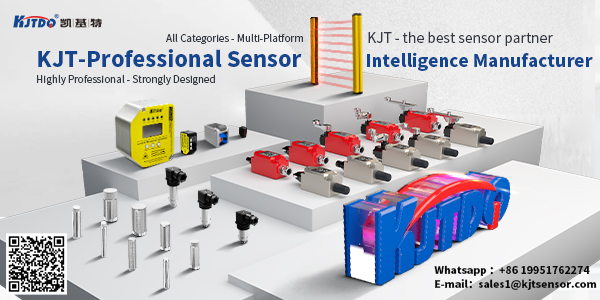
How It Generates Those Crucial Pulses: The Working Mechanism
- The Internal Oscillator: Inside the sensor, an electronic oscillator generates a high-frequency alternating current (AC). This current flows through a coil wound around a ferrite core at the sensor’s active face, creating a high-frequency electromagnetic field.
- Target Interaction: When a metallic target (like a gear tooth, a bolt head on a rotating shaft, or a flag on a linear slide) enters this electromagnetic field, eddy currents are induced on the surface of the target.
- Energy Absorption and Field Dampening: These eddy currents draw energy from the sensor’s oscillating circuit. This energy loss results in a dampening or reduction in the amplitude of the oscillation.
- Signal Processing & Pulse Generation: The sensor’s internal circuitry constantly monitors this oscillation amplitude. When the damping caused by the target’s presence crosses a predefined threshold, the circuit reacts. This reaction is output as a clean, sharp, digital pulse signal – typically switching from a low state (no target) to a high state (target detected), or vice-versa. Crucially, each pulse corresponds directly to one instance of a target passing the sensor face.
- Reset & Repeat: As the target moves away, the eddy currents dissipate, the oscillation amplitude recovers, and the output signal returns to its original state, ready to detect the next target and generate the next pulse.
Key Advantages Driving Widespread Adoption
- Non-Contact Sensing: The fundamental strength. No physical wear on the sensor or the target occurs, leading to extremely long operational lifespans and minimal maintenance requirements. This is vital in harsh or high-speed environments.
- Exceptional Robustness: Designed for the industrial battlefield. Inductive pulse sensors typically feature rugged, often metal or high-grade polymer housings, sealing them against dust, dirt, moisture, oil, and vibration. Their immunity to environmental contaminants makes them ideal for challenging factory settings, automotive under-hood applications, or outdoor machinery.
- Inherent Resistance to EMI: The nature of inductive sensing makes these sensors naturally less susceptible to interference from stray electromagnetic fields compared to some other sensing technologies, ensuring reliable signal integrity.
- High Switching Frequencies & Speeds: Capable of operating at very high frequencies, modern inductive pulse sensors can reliably detect targets moving at tremendous speeds, making them perfect for high-speed counting and rotational speed measurement (RPM) applications.
- Simple Integration: The output is a straightforward, easy-to-process digital pulse train. This simplicity allows for direct interfacing with Programmable Logic Controllers (PLCs), counters, timers, microcontrollers, and other industrial control systems with minimal signal conditioning.
Where Do Inductive Pulse Sensors Shine? Key Applications
Their unique combination of robustness, speed, and non-contact operation makes them ubiquitous across diverse sectors:
- Automotive & Transportation: Monitoring engine RPM (via crankshaft or camshaft target wheels), measuring wheel speed for Anti-lock Braking Systems (ABS) and Traction Control (TCS), detecting gear position, counting shaft rotations in transmissions.
- Industrial Automation & Manufacturing: Speed monitoring of motors, conveyors, and rotating machinery. Precise positioning of robotic arms or linear actuators using target flags. Product counting on high-speed lines (e.g., cans, bottles, packaged goods). Part presence/absence verification on assembly lines. Tool break detection in machining centers.
- Material Handling: Monitoring roller speeds, detecting the presence of pallets or metal carriers on conveyors, controlling sorting gates.
- Heavy Machinery & Equipment: Monitoring rotation speeds in large motors, pumps, fans, and turbines. Overspeed protection systems.
- Process Control: Providing feedback on valve stem position (using metallic flags) or agitator speed.
Beyond Simple Presence: The Power of Pulse Counting
While detecting a single target is useful, the true power of the inductive pulse sensor emerges in applications involving repetitive motion. By counting the number of pulses generated over a specific time period, systems can accurately calculate:
- Rotational Speed (RPM): [(Number of Pulses per Revolution) / (Time in Minutes)] = RPM. Essential for motor control, engine management, and process monitoring.
- Linear Speed: If the target spacing is known (e.g., teeth on a rack gear moving past the sensor), linear velocity can be derived from the pulse frequency.
- Position: By counting pulses from a known starting position (often combined with an index marker), relative position can be tracked accurately. This is fundamental for incremental positioning systems.
- Total Distance Traveled: Cumulative pulse counts relate directly to total rotations or linear distance covered.
Choosing and Implementing: Important Considerations
Selecting the right inductive pulse sensor involves key factors:
- Target Material: Ferrous metals (steel, iron) provide the strongest signal and longest sensing ranges. Non-ferrous metals (aluminum, brass, copper) induce weaker eddy currents, requiring sensors specifically designed or calibrated for them.
- Sensing Distance: The nominal range at which the sensor can reliably detect the specified target. Factors like target size and shape also influence actual performance.
- Switching Frequency: Max pulses per second the sensor can reliably generate. Must exceed the maximum expected pulse rate of the application.
- Output Type: Typically NPN (sinking) or PNP (sourcing) transistor outputs, compatible with different PLC input cards. Some offer integrated voltage outputs (e.g., 0-10V) representing speed.
- Connection Style: Cable exit or connector (M8, M12).
- Electrical Ratings: Supply voltage (e.g., 10-30V DC), output current capacity.
- Environmental Rating: IP67, IP68, or IP69K ratings are common for dust and water resistance. Temperature range suitability is critical.
The Future: Integration and Intelligence
While fundamentally robust and simple, trends point towards greater integration. We see more inductive pulse sensors with integrated ASICs (Application-Specific Integrated Circuits) offering advanced features like short-circuit protection, diagnostics (e.g., LED status indication), or even signal conditioning onboard. Their role remains foundational in the Industrial Internet of Things (IIoT), providing the critical raw pulse data that feeds higher-level analytics and control systems monitoring machinery health, optimizing production flow, and enabling predictive maintenance.
In a world increasingly