inductive sensor distance
- time:2025-07-10 01:59:24
- Click:0
The Art of Distance: How Inductive Sensors Revolutionize Non-Contact Measurement
The seamless operation of modern machinery often hinges on an invisible, precise interaction: accurately knowing how far one object is from another, all without physical contact. This critical task, central to countless industrial automation, automotive, and manufacturing processes, is expertly handled by inductive proximity sensors. Understanding inductive sensor distance capabilities is fundamental to harnessing their power for reliable detection and measurement. This article dives into the core principles, capabilities, and practical considerations surrounding distance measurement with these versatile workhorses of industrial sensing.
At their heart, inductive proximity sensors exploit the laws of electromagnetic induction. When an electrical current flows through a coil housed within the sensor, it generates an oscillating electromagnetic field around its active face. This field is the sensor’s “sensing zone.” When a conductive target – typically made of metal – enters this field, eddy currents are induced within the target material. These swirling electrical currents create their own opposing magnetic field, which interacts with the sensor’s original field.
The Key to Distance Measurement: Damping
This interaction is the magic behind detection. The presence of the target and its eddy currents effectively dampens the energy of the sensor’s oscillating circuit. The closer the target is to the sensor’s face, the stronger the eddy currents generated, and consequently, the greater the damping effect on the sensor’s internal circuit. The sensor’s electronics are meticulously calibrated to detect this change in oscillation amplitude (or sometimes frequency). When this damping exceeds a pre-set threshold – the switching point – the sensor triggers its output signal (ON/OFF), indicating the target’s presence within its nominal sensing range.
This fundamental switching behavior forms the basis of proximity detection. However, the concept of distance manifests in several crucial ways:
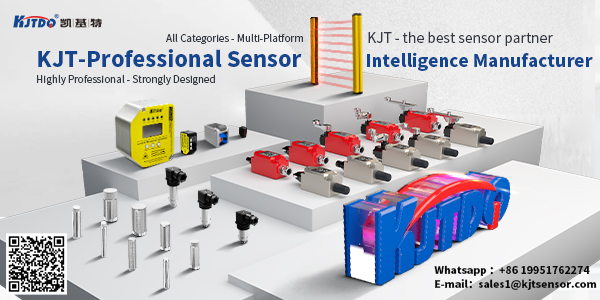
- Nominal Sensing Distance (Sn): This is the standardized operating distance under ideal conditions (usually defined with a specific target material, size, and shape – often mild steel). It’s the headline figure quoted in sensor specifications. A sensor with an Sn of 5mm will reliably detect a standard target when it comes within 5mm of its face.
- Effective Sensing Distance (Sr): This represents the actual operating distance achievable under specific, real-world conditions. It factors in variables like supply voltage tolerance and the specified operating temperature range. Sr typically falls between 90% and 110% of Sn.
- Repeat Accuracy: For applications demanding precision positioning or measurement, repeat accuracy is paramount. This refers to the sensor’s ability to consistently trigger its output at the exact same distance from the target under identical conditions (temperature, humidity, target approach direction). High-quality sensors boast exceptional repeatability, often in the micron range.
- Hysteresis: To prevent output signal oscillation (“chatter”) when a target sits right at the switching point, inductive sensors incorporate hysteresis. This means the distance at which the sensor turns OFF as the target moves away is slightly greater than the distance at which it turned ON as the target approached. This small buffer ensures clean, stable switching signals.
Factors Influencing Inductive Sensor Distance Performance:
While seemingly straightforward, achieving optimal and reliable distance measurement relies on understanding and mitigating influencing factors:
- Target Material: Not all metals are created equal in the eyes of an inductive sensor. The conductivity and magnetic permeability of the target material drastically affect sensing distance. Ferromagnetic materials (like mild steel) induce the strongest eddy currents and offer the longest sensing ranges. Austenitic stainless steel or aluminum (which are non-ferrous) have lower permeability, resulting in significantly shorter sensing distances – sometimes as little as 1⁄3 of the Sn for steel. Copper and brass induce even smaller sensing ranges. Always consult the sensor datasheet for correction factors.
- Target Size and Shape: For optimal performance, the target should be at least equivalent to the sensor’s face diameter or the standard target specified (often defined as a square plate 3 times the Sn thick). Smaller or irregularly shaped targets can significantly reduce the effective sensing distance.
- Operating Frequency: The oscillation frequency of the sensor’s field impacts penetration depth and susceptibility to interference. Higher frequencies offer better resolution for small targets but have shorter ranges and are more affected by surrounding metals. Lower frequencies penetrate deeper and are less susceptible to interference but offer coarser resolution.
- Temperature Drift (Temperature Coefficient): Like most electronics, inductive sensors experience slight shifts in their operating characteristics with temperature changes. This primarily affects the switching distance. High-quality sensors specify a temperature coefficient value (e.g., ≤10% change in Sn over operating temperature range), allowing engineers to factor this into critical applications.
- Embedding (Flush vs. Non-Flush Mounting): Shielded (flush mountable) sensors can be installed flush within a metal bracket. Their magnetic field is concentrated directly in front, reducing side interference but also slightly decreasing the nominal sensing range compared to unshielded (non-flush) models. Unshielded sensors have a larger lateral field, offering longer ranges but requiring clearance around the mounting hole to prevent false triggers from nearby metal.
Beyond Switching: Distance Measurement with Analog Sensors
While standard inductive sensors excel at proximity detection (ON/OFF), specialized analog inductive sensors take distance measurement a step further. Instead of simply triggering at a threshold, these sensors provide a continuously variable output signal (e.g., 4-20mA, 0-10V, or IO-Link) that is proportional to the distance between the sensor face and the target. This enables precise position monitoring, dimension checking, runout measurement, and thickness control in demanding industrial environments. Their operating principle remains based on the damping effect, but with sophisticated electronics translating the varying oscillation amplitude/frequency into a linear (or defined) analog output.
Selecting the Right Sensor for Precise Distance Control
Choosing the ideal inductive sensor hinges on your specific distance requirements:
- Define the Application: Is simple presence detection sufficient, or is precise analog measurement needed?
- Identify Target Material: Determine the conductivity and permeability of the target metal. This is critical for estimating the achievable sensing range.
- Determine Required Range and Accuracy: Specify the nominal distance needed and the required repeatability/resolution. Remember the material correction factor!
- Consider Environmental Factors: Account for temperature extremes, potential chemical exposure, mechanical vibrations, and electrical interference.
- Review Mounting Constraints: Ensure sufficient space and choose between shielded (flush) or unshielded (non-flush) mounting based on installation needs and desired field shape.
Inductive sensor distance capabilities form the bedrock of their widespread success in automation. From ensuring robotic arms position accurately and counting metal parts on fast-moving conveyors to monitoring critical clearances in engines and controlling sheet metal thickness, their robust, non-contact method of gauging separation delivers unparalleled reliability in harsh industrial settings. By mastering the principles of electromagnetic induction, target influence, and key performance factors, engineers can unlock the full potential of these sensors, ensuring machines operate safely, efficiently, and with pinpoint precision.