id ideal proximity sensor
- time:2025-07-09 02:28:04
- Click:0
ID Ideal Proximity Sensor: Defining Peak Performance for Industrial Detection
Imagine a world where assembly lines screech to a halt because a tiny sensor failed to detect a passing component. Or where robotic arms malfunction due to inaccurate position feedback. In the intricate dance of modern manufacturing and automation, proximity sensors are the silent, unwavering sentinels. But not all sensors are created equal. When reliability is non-negotiable and performance demands are extreme, the quest becomes finding the ID ideal proximity sensor – a device embodying the pinnacle of what this critical component should achieve.
So, what defines ID ideal? It transcends basic functionality. It represents the synthesis of robustness, precision, longevity, and adaptability specifically tailored for Industrial Duty (ID) environments. An ID-ideal proximity sensor isn’t just about detecting presence or absence; it’s about delivering unwavering accuracy and resilience under the harshest conditions, day in and day out.
The Pillars of ID-Ideal Performance
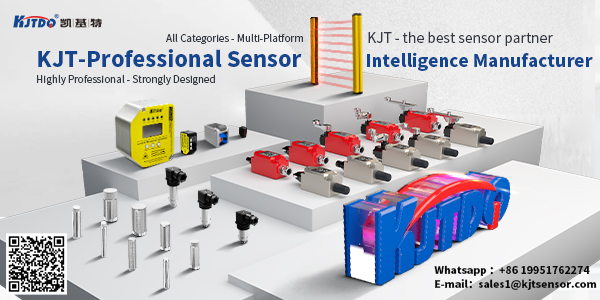
- Unwavering Sensing Consistency: An ideal sensor provides consistent and reliable detection at its specified range. Factors influencing this include:
- Stable Operating Point: Minimal shift in switching distance despite temperature fluctuations, voltage variations, or component aging. This is crucial for precision applications like robotic positioning or high-speed counting.
- Minimal Hysteresis: Hysteresis is the difference between the switch-on point (when the target approaches) and switch-off point (when it moves away). An ID-ideal sensor exhibits low hysteresis, ensuring crisp switching without false triggers near the threshold, vital for accurate position control.
- Repeatability: Delivering the exact same switching point repeatedly under identical conditions is fundamental for process control reliability.
- Industrial-Grade Durability: Factories are tough. An ideal proximity sensor must be built like a tank.
- Extreme Environmental Resistance: Superior sealing (IP67, IP68, IP69K ratings) is essential to withstand dust, coolants, oils, high-pressure washdown, and humidity. Resistance to chemicals commonly found in industrial settings is non-negotiable.
- Temperature Resilience: Consistent operation across broad temperature ranges (e.g., -40°C to +85°C or beyond) is critical for foundries, cold storage, and outdoor applications. Internal components and housing materials must endure thermal shock and cycling.
- Impact and Vibration Immunity: Robust stainless steel or high-grade polymer housings protect sensitive electronics from physical knocks, drops, and constant vibration prevalent in machinery and conveyors.
- Electrical Robustness and Stability: Electrical noise is the enemy of reliable sensing. An ID-ideal sensor combats this through:
- Superior Noise Immunity: Advanced circuitry designed to reject electromagnetic interference (EMI) and radio frequency interference (RFI) from motors, drives, and welding equipment.
- Output Protection: Built-in safeguards against short-circuits, overcurrent, reverse polarity, and overvoltage spikes protect both the sensor itself and the connected control system.
- Stable Power Operation: Maintaining consistent performance even with fluctuations in the supply voltage common in industrial power grids.
- Output Flexibility and Compatibility: Seamless integration into diverse control systems is key.
- Output Configuration: Availability of NPN/PNP sourcing/sinking types, both NO (Normally Open) and NC (Normally Closed) variants.
- Versatile Connection Options: Standard M8, M12, or larger cable/connector types, including quick-disconnect options for easy replacement and maintenance.
- Application-Specific Adaptation: True ID-ideal performance often hinges on specialized features:
- Enhanced Sensing Ranges: Longer detection distances for specific mounting challenges.
- Non-Ferrous Target Detection: Ability to reliably sense aluminum, brass, copper, or stainless steel targets, which standard inductive sensors struggle with.
- Compact Form Factors: Miniature housing sizes for installation in tight spaces without compromising performance.
- High Switching Frequencies: Essential for detecting very small or fast-moving objects on high-speed production lines.
Choosing Your ID-Ideal Sensor: Beyond the Spec Sheet
Selecting the right sensor goes beyond just matching basic specs. It requires a deep understanding of the application’s demands:
- The Target Material: Ferrous metal, non-ferrous metal, plastic, liquid? This dictates the sensor type (inductive, capacitive, magnetic).
- Environmental Conditions: Temperature extremes, humidity, dust, chemicals, pressure washdown? Define the required IP rating and material compatibility.
- Electrical Environment: Level of electrical noise? Required switching speed? Voltage supply type?
- Mounting Constraints: Available space? Required sensing distance? Flush or non-flush mounting capability?
- Performance Tolerance: How critical is exact switching point consistency and minimal hysteresis? What level of reliability is demanded?
Investing in Peak Performance
While basic proximity sensors serve many purposes, demanding industrial applications require the ID-ideal level. The investment in sensors engineered for exceptional durability, uncompromising precision, superior electrical immunity, and application-specific optimization pays dividends. It translates directly into:
- Reduced Downtime: Fewer sensor failures mean production lines keep running.
- Enhanced Quality: Consistent, accurate detection leads to fewer defects and scrap.
- Lower Total Cost of Ownership: Longer lifespan and reduced maintenance outweigh a higher initial purchase price.
- Improved Process Reliability: Confidence that critical position, presence, and movement detection functions will perform flawlessly.
The ID ideal proximity sensor isn’t a mythical concept; it’s the benchmark for sensors designed to conquer the most challenging industrial environments. By prioritizing the core pillars of robustness, precision, stability, and adaptability, these devices become the reliable foundation upon which efficient, high-performance automation systems are built. When the stakes are high, settling for anything less than ideal performance is a risk manufacturers simply cannot afford.