high pressure proximity sensor
- time:2025-07-09 02:21:01
- Click:0
High Pressure Proximity Sensors: Unlocking Reliable Detection in Extreme Environments
Operating machinery or conducting critical processes in environments where immense pressure reigns is no small feat. Standard sensors buckle under the strain, leading to failures, inaccuracies, and potential safety hazards. Enter the high pressure proximity sensor – a specialized breed of non-contact detection devices engineered to thrive where others falter. This article delves into their working principles, vital applications, and the cutting-edge technology enabling precision sensing against crushing forces.
Defying the Crush: Why High Pressure Demands Specialized Sensors
Proximity sensors, at their core, detect the presence, absence, or distance of an object without physical contact, typically using electromagnetic fields, capacitance, or ultrasonic sound waves. However, when deployed in scenarios involving hydraulic systems, deep-sea applications, high-pressure processing (HPP) for food, oil and gas drilling, or industrial presses, standard sensors face insurmountable challenges:
- Physical Deformation: Excessive external pressure can crush sensor housings, distort diaphragms, or damage sensitive internal electronics.
- Seal Failure: Maintaining a hermetic seal preventing internal electronics from exposure to high-pressure fluids or gases becomes exponentially harder.
- Signal Interference: High-pressure environments can alter the properties of the surrounding medium (e.g., fluid density), potentially affecting the sensor’s field or wave propagation and leading to false readings.
A high pressure proximity sensor is specifically designed to overcome these hurdles. It’s built to withstand immense external pressure while reliably performing its detection function, ensuring continuity and safety in critical operations.
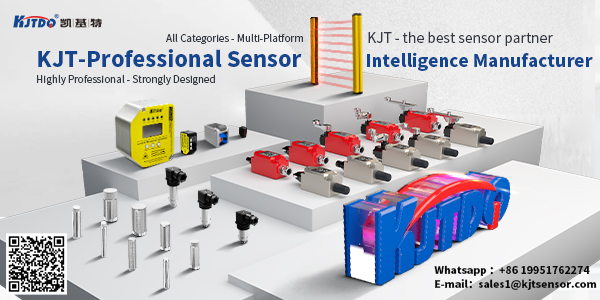
Engineering the Resistance: Core Technologies and Design
The robustness of a high pressure proximity sensor stems from meticulous design and material selection:
- Ruggedized Housings: Constructed from high-strength alloys like stainless steel (e.g., 316L) or specialized titanium. These materials resist deformation and corrosion prevalent in harsh environments.
- Advanced Sealing: Multiple redundant seals, often utilizing specialized elastomers (like FKM/Viton or FFKM/Kalrez) and metal-to-metal seals, create a formidable barrier against fluid or gas intrusion. Techniques like welded housings or glass-to-metal hermetic seals are frequently employed for ultimate integrity. Achieving high IP (Ingress Protection) ratings (like IP67, IP68, IP69K) and pressure ratings (commonly ranging from 100 bar to over 1000 bar / 1450 PSI to 14,500+ PSI) is paramount.
- Pressure-Compensated Electronics: In certain designs, particularly for subsea or deep oil/gas applications, internal compensation mechanisms equalize pressure inside the sensor housing to the external environment. This prevents housing collapse while protecting the delicate core electronics from differential pressure stress.
- Sensor Element Protection: The actual sensing element (whether inductive coil, capacitive plate, or ultrasonic transducer) is shielded and potted using specialized, pressure-resistant compounds to maintain stability and accuracy.
- Temperature Resilience: High-pressure environments often coincide with extreme temperatures. These sensors incorporate designs and materials capable of operating reliably in wide temperature ranges.
Inductive vs. Other Technologies
- Inductive Proximity Sensors: The most common type used in high-pressure industrial settings. They detect metallic targets via an electromagnetic field. Their solid-state nature (no moving parts) and ability to be potted effectively make them highly suitable. Key specifications include high pressure rating, temperature range, and the sensing distance achievable despite the robust housing thickness.
- Capacitive Proximity Sensors: Can detect non-metallic materials but are more sensitive to changes in the dielectric constant of the medium separating them from the target, which pressure fluctuations can influence. Less common for pure high-pressure applications than inductive types, though specialized versions exist.
- Ultrasonic Proximity Sensors: Use sound waves. Pressure affects sound wave propagation speed and attenuation. While used in some high-pressure applications (like tank level sensing), careful calibration and compensation for pressure effects are crucial.
Mission-Critical Applications
- Hydraulic Systems: Monitoring cylinder rod position, valve spool position, or component presence within high-pressure hydraulic circuits is critical for control and safety. High pressure inductive sensors are ubiquitous here.
- Oil & Gas Exploration/Production: Downhole tools, subsea equipment (Christmas trees, manifolds), and surface processing units operate under extreme pressures. Sensors monitor valve positions, actuator states, and equipment proximity vital for remote operation and safety.
- High-Pressure Processing (HPP): Used in food and beverage industries for non-thermal pasteurization. Sensors ensure vessel closure integrity, component positioning, and safety interlocks under pressures exceeding 6,000 bar (87,000 PSI).
- Industrial Presses & Stamping: Detecting die positions, material presence, and safety guards in presses generating enormous forces requires sensors that won’t fail under incidental or operational pressure.
- Deep-Sea Exploration: ROVs (Remotely Operated Vehicles), AUVs (Autonomous Underwater Vehicles), and fixed subsea installations rely on sensors capable of withstanding the immense hydrostatic pressure of deep water. Pressure compensation is often critical here.
- Chemical & Petrochemical Processing: Monitoring valves, actuators, and equipment status in pipelines and reactors handling high-pressure fluids and gases.
Choosing and Implementing Correctly
Selecting the right high pressure proximity sensor requires careful consideration:
- Pressure Rating: The absolute critical factor. Ensure the sensor’s rating exceeds the maximum possible system pressure, including potential pressure spikes or surges. Include a safety margin.
- Temperature Range: Must cover both operating and storage temperatures.
- Media Compatibility: Housing material and seals must resist corrosion from the surrounding fluids or gases (e.g., seawater, hydraulic oil, chemicals).
- Sensor Technology & Target: Match the technology (inductive, capacitive, ultrasonic) to the material being detected.
- Electrical Requirements: Voltage, output type (PNP/NPN, analog), connection type (connector, cable), and required protection ratings.
- Mechanical Integration: Size, thread type, mounting options must fit the application space and pressure boundary requirements. Proper installation, including correct gasket usage and torque specifications, is essential to maintain the pressure rating. Overtightening can be as detrimental as undertightening.
The Future: Smarter Sensing Under Pressure
As industries push into deeper waters, higher pressures, and more automated processes, demand for reliable proximity detection in extreme environments will only grow. Advancements focus on:
- Even higher pressure ratings in smaller form factors.
- Improved integration of diagnostics and communication (IO-Link) for predictive maintenance.
- Enhanced resistance to combined stresses (pressure, temperature, vibration, corrosive media).
- Development of new sensing principles offering greater accuracy or target material flexibility under extreme conditions.
High pressure proximity sensors are the unsung guardians of reliability and safety in some of the world’s most demanding industrial environments. By combining rugged mechanical design, advanced sealing technologies, and robust sensing principles, they provide the critical non-contact detection necessary to keep complex, high-stakes operations running smoothly and safely, defying the crushing forces that would silence lesser instruments. Their continued evolution is key to unlocking new frontiers in automation and exploration.