flush type proximity sensor
- time:2025-07-09 01:52:50
- Click:0
Flush-Mount Proximity Sensors: The Ultimate Solution for Compact, Protected Detection
In the tight confines of modern machinery, robotic cells, and automated production lines, every millimeter counts. Imagine a sensor protruding from its mounting surface – an accident waiting to happen. A stray tool, a jostling part, or even routine vibration can turn a critical detection point into a costly repair and downtime scenario. This is where flush type proximity sensors shine. Engineered to sit entirely embedded within their mounting surface, these robust devices offer a streamlined, protected solution for non-contact object detection where space is tight and resilience is non-negotiable.
Understanding the “Flush” Advantage
Unlike their non-flush (or “shrouded”) counterparts, flush-mount proximity sensors feature a shielded sensing face. This shielding, typically a metal ring surrounding the active sensor element, is key to their operation. This design allows the sensor to be mounted flush to a metal surface (like a bracket or machine frame) without causing the metal to interfere with its detection capabilities.
- How They Work (The Short Version): Most industrial flush proximity sensors operate on the inductive principle. An internal oscillator generates a high-frequency electromagnetic field at the sensor’s face. When a metallic target enters this field, eddy currents are induced on the target’s surface. These eddy currents draw energy from the oscillator, causing its amplitude to decrease. The sensor’s electronic circuitry detects this change and switches its output state (ON/OFF).
- The Shielded Design’s Role: The shielding effectively contains and focuses the electromagnetic field forward from the sensor face. Crucially, it channels the field lines away from the surrounding metal mounting surface. This prevents the sensor from being “fooled” by the metal it’s mounted into. Without this shielding (as in non-flush sensors), mounting into metal would drastically reduce the effective sensing range or make reliable detection impossible.
Key Advantages Driving Adoption
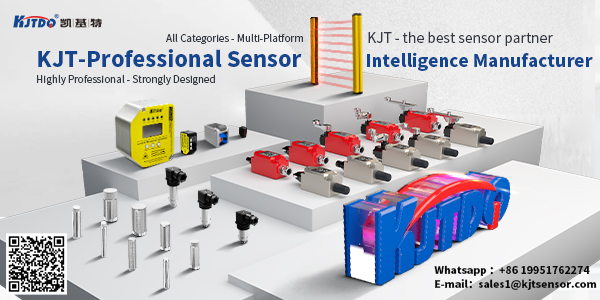
The flush mounting capability translates directly into several compelling benefits:
- Maximized Space Efficiency: Their ability to be mounted entirely within a hole means they take up zero external space beyond the mounting surface itself. This is invaluable in compact machinery, densely packed control panels, robotic arms, and applications where parts or tools move in close proximity.
- Exceptional Physical Protection: Sitting flush with the surface, the sensor face is shielded from direct impact, abrasion, and accidental knocks. The surrounding metal effectively acts as a protective barrier. This significantly enhances durability and reliability in harsh industrial environments.
- Reduced Snagging Risk: With no protruding parts, there is virtually no chance for wires, cables, moving parts, or tools to snag on the sensor, minimizing potential damage and production stoppages.
- Simplified Installation and Maintenance: Mounting typically involves simply inserting the sensor into a pre-drilled hole and securing it with a locknut. Their robust design often translates to less frequent need for replacement compared to exposed sensors.
- Resistance to Contaminants: The flush design offers better protection against the buildup of dust, chips, coolants, and other process debris compared to recessed non-flush sensors that might have crevices around them. Proper sealing ratings (like IP67, IP68, IP69K) are still essential for harsh washdown or submerged environments, but the flush face inherently helps.
Common Applications: Where Compactness and Toughness Rule
Flush-mount inductive proximity sensors are ubiquitous in automation due to their rugged simplicity:
- Robotics: Detecting end-effector positions, tool presence (is the gripper holding a part?), and guarding within the tight confines of robot joints and wrists.
- Machine Tooling: Monitoring tool position (broken tool detection), workpiece presence/clamping in CNC machines, lathes, and mills where space is tight and coolant/chips are prevalent.
- Material Handling: Verifying part positioning on conveyors, pallet presence, elevator position, and door/gate detection on AGVs and ASRS systems.
- Packaging Machinery: Counting bottles/cans on high-speed lines, verifying case sealer flaps are closed, detecting label presence – often in space-limited mechanisms.
- Assembly Automation: Confirming component placement, detecting piston/cylinder position in pneumatic/hydraulic systems, and verifying fixture states.
- General Machinery: Any application requiring reliable detection of metal objects where a protruding sensor would be vulnerable or physically impractical.
Important Considerations: Sensing Range Limitations
While offering immense benefits, the shielded design of flush-mount sensors comes with a trade-off: reduced sensing range. Because the electromagnetic field is tightly focused forward, the operating distance (Sn) is typically shorter than an equivalent-sized non-flush sensor. For example, an M12 flush sensor might have an Sn of 2mm, while a non-flush M12 could detect the same target at 4mm.
- Factor in Mounting Material: The ideal scenario is mounting into a ferrous (steel) material. Mounting into non-ferrous metals (aluminum, brass) or thick non-metallic materials can sometimes slightly reduce the effective sensing range compared to mounting in steel.
- Target Material Matters: Standard inductive sensors are primarily designed for ferrous metals (steel, iron). Detection of non-ferrous metals (aluminum, copper, brass) requires specific sensor models designed for such targets, and these will typically have a significantly reduced sensing range even compared to standard flush sensors detecting steel. Always consult the sensor datasheet for specifics on target material influence.
Selecting the Right Flush Sensor
When specifying a flush type proximity sensor, key factors include:
- Required Sensing Distance (Sn): Check the datasheet carefully for the Sn value under the specific mounting conditions and target material you need.
- Mounting Size (Thread or Body Size): Common barrel sizes include M5, M8, M12, M18, M30. Choose based on available space and required robustness.
- Output Type (PNP/NPN, NO/NC): Match the sensor’s output configuration (e.g., PNP Normally Open) to your PLC or controller’s input requirements.
- Electrical Connection: Options include pre-wired cables, quick-disconnect (M8, M12 connectors), or terminal connections.
- Environmental Protection (IP Rating): Ensure the sensor’s Ingress Protection (IP) rating (e.g., IP67, IP68, IP69K) meets the demands of the operating environment (dust, moisture, high-pressure washdown).
- Target Material: Standard flush sensors excel with steel/iron. For reliable non-ferrous metal detection, seek models specifically designed for aluminum/copper/etc., accepting the inherent range reduction.
- Performance Features: Options like high-temperature resistance, extended temperature range, resistance to welding fields, or FDA-compliant materials may be necessary for specific applications.
Embracing the Flush Advantage
The flush-mount proximity sensor is a cornerstone technology in modern industrial automation, elegantly solving the challenge of reliable detection in confined and demanding spaces. By combining robust physical protection through integrated mounting with the non-contact, wear-free benefits of inductive sensing, these devices enhance both the reliability and longevity of machinery. Carefully considering the inherent sensing range limitations ensures optimal selection, allowing designers and engineers to leverage the unique strengths of flush type proximity sensors to build smarter, tougher, and more compact automated systems.