flat inductive proximity sensor
- time:2025-07-09 01:31:44
- Click:0
Flat Inductive Proximity Sensors: Unlocking Space-Saving Sensing Precision
The relentless drive for miniaturization and efficiency in modern machinery presents a constant challenge: how to integrate reliable sensing into increasingly cramped spaces without sacrificing performance. This is where the specialized design of flat inductive proximity sensors truly excels. Offering a unique blend of ultra-low profile construction and robust inductive detection principles, these sensors are the unsung heroes enabling automation in applications where traditional cylindrical sensors simply won’t fit.
Understanding the Core: How Inductive Proximity Sensing Works
All inductive proximity sensors operate on the same fundamental electromagnetic principle. The sensor contains an internal coil energized by a high-frequency oscillating current, generating an electromagnetic field at its active face. When a ferrous (iron-based) or non-ferrous (like aluminum, brass, copper) metal target enters this field, eddy currents are induced within the target. These eddy currents draw energy from the sensor’s oscillator circuit. The sensor’s electronics detect this energy loss (damping of the oscillation), triggering an output signal switch – indicating the presence of the target. It’s a completely non-contact detection method, meaning no physical touch is required, ensuring long life and wear-free operation.
The Defining Advantage: Why “Flat” Matters
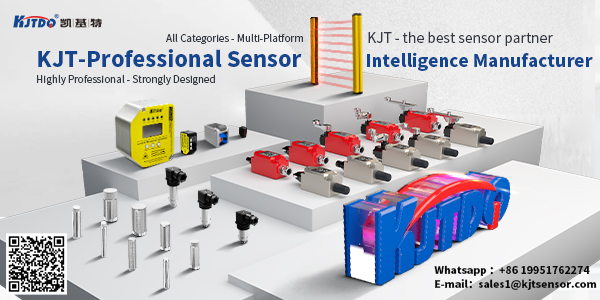
While the underlying technology is shared with standard inductive sensors, the distinct flat inductive proximity sensor configuration offers critical benefits driven by its form factor:
- Extremely Low Installation Profile: This is the primary differentiator. Measuring often just a few millimeters thick, these sensors can be installed in areas where vertical space is severely restricted – behind thin panels, between rollers, within compact tooling heads, or on the sides of narrow guide rails. Their minimal protrusion prevents interference with moving parts or the target itself.
- Flush Mounting Capability: Many flat sensors are designed for flush mounting (also called embeddable or non-flush mounting). This means they can be installed level with (or even recessed into) a surrounding metal mounting surface. Crucially, their electromagnetic field is designed so that the surrounding metal does not cause false triggering. This allows for incredibly neat, protected, and space-efficient installations.
- Resistance to Mounting Surface Effects: Thanks to their focused field design (often termed “shielded” or “suppressed field”), flat inductive proximity sensors are largely immune to the influence of adjacent metal machinery structures, unlike their unshielded (non-flush) cylindrical counterparts. This provides greater installation flexibility and reliability in metal-rich environments.
- Robust Construction: Despite their slim profile, reputable flat sensors boast durable housings (often stainless steel or specialized PBT plastics) capable of withstanding industrial environments, including impacts, vibrations, cutting fluids, coolants, and washdowns (with appropriate IP ratings like IP67/IP68).
- Discreet Integration: The low profile and often rectangular shape allow for seamless integration into machine designs where aesthetics or avoiding snag points are important.
Where Flat Inductive Sensors Shine: Key Applications
The unique advantages of compact proximity sensing translate into indispensable solutions across diverse sectors:
- Robotics & Automation: Mounting inside grippers, on slender robot arms, or within end-of-arm tooling (EOAT) where space is at an absolute premium. Detecting fingers closing or tool presence.
- Machine Building (CNC, Lathes, Mills): Tool presence/absence verification in cramped tool changers, turret indexing confirmation, chuck jaw position, and detecting small parts on pallets or fixtures within the machine envelope.
- Packaging Machinery: Sensing metallic foil seals, detecting metal components on high-speed conveyors without adding height, confirming lid placement on cans or containers – essential for fill level control and quality checks.
- Material Handling: Position detection on thin transfer slides, confirming elevator platform levels, sensing pallet presence on rollers or within automated storage systems where clearance is minimal.
- Automotive Manufacturing: Integration into tight spaces within welding jigs, assembly robots, press lines, and final assembly stations for part presence verification on moving pallets or fixtures.
- Semiconductor & Electronics: Wafer handling robotics, cassette presence detection, and other precision applications demanding reliable metal detection without bulk.
Choosing the Right Flat Inductive Sensor: Key Considerations
Selecting the optimal flat inductive proximity sensor requires careful evaluation:
- Required Sensing Range: Flat sensors inherently have shorter sensing ranges (typically 0.5mm to 4mm) compared to longer cylindrical models. Precisely define the gap needed between the sensor face and the target.
- Target Material: Ferrous metals (steel, iron) are easiest to detect and offer the longest nominal sensing distance. Non-ferrous metals (aluminum, brass, copper) require sensors specifically designed for them or will have a significantly reduced sensing range (often 50-60% less than for steel). Confirm the sensor’s suitability for your target metal.
- Size and Dimensions: Beyond thickness, consider the sensor’s length and width to ensure it fits the available mounting footprint. Miniaturization extends to various rectangular sizes.
- Output Configuration: Common options are NPN (sourcing) or PNP (sinking) transistor outputs (3-wire), 2-wire AC/DC, or analog (current/voltage). Choose based on your control system compatibility.
- Electrical Connection: Options include fixed cable, quick-disconnect (M8, M12 connectors), or solder/pigtail leads.
- Environmental Requirements: Verify the IP rating (Ingress Protection) for dust and water resistance. Consider temperature range, chemical exposure, and required housing material (stainless steel offers the highest durability and corrosion resistance).
- Mounting Requirements: Choose between flush mountable (shielded) versions or very rare non-flush types if needed. Ensure the mounting method (slots, tapped holes) suits your application.
- Performance Features: Some models offer extra features like short-circuit protection, reverse polarity protection, high switching frequencies for fast-moving targets, EMI resistance, or IO-Link capability for smart sensor integration and diagnostics.
Installation Nuances for Optimal Performance
Proper installation is vital for reliable inductive sensing:
- Follow Mounting Instructions: Adhere strictly to the manufacturer’s specified mounting distances (especially for flush mounting) and sensor-to-sensor separation distances to prevent mutual interference.
- Minimize Air Gap: Achieve the most stable and repeatable sensing by keeping the distance between the sensor face and the target as small and consistent as possible, well within the rated sensing range.
- Target Approach: Ideally, the target should approach the sensor perpendicular to its face. Angled approaches can reduce the effective sensing distance.
- Clean Sensing Face: Ensure the sensor’s active face is free of dirt, metal shavings, oil buildup, or other contaminants that could degrade performance.
- Secure Wiring: Protect sensor cables from abrasion, pinching, and strain. Use cable glands or conduits where appropriate. Ensure correct electrical connections to prevent damage.
Embracing the Low-Profile Solution
Flat inductive proximity sensors are far more than just a space-saving alternative; they are a critical enabling technology for the next generation of compact, efficient, and sophisticated machinery. By understanding their principles of operation, appreciating their distinct flat design advantages, carefully selecting the right model for the specific task, and installing them correctly, engineers and designers can overcome spatial constraints while maintaining the robustness, reliability, and non-contact precision that define inductive sensing. From the tiniest robotic gripper to high-speed packaging lines, these slim powerhouses continue to prove their indispensable value in industrial automation worldwide.