flush and non flush sensor
- time:2025-07-09 01:38:46
- Click:0
Flush vs. Non-Flush Sensors: Mastering Proximity Detection Choices in Automation
In the intricate dance of modern manufacturing and industrial automation, proximity sensors are the silent choreographers. They detect the presence or absence of objects without physical contact, orchestrating processes with precision and speed. But not all applications are created equal. The physical environment, target composition, and required sensing distance introduce critical variables. This is where the fundamental distinction between flush-mountable (often shortened to flush) and non-flush-mountable (non-flush) sensors becomes paramount. Choosing wisely between these two configurations isn’t just about fitting a component; it’s about ensuring optimal performance, reliability, and longevity of your system.
Understanding the Core Distinction: Mounting and Magnetic Field Shape
At the heart of inductive proximity sensors (the most common type for metal detection in these mounting styles), lies a coil that generates an oscillating electromagnetic field. The key difference between flush and non-flush models is how they manage this field in relation to their physical housing and the mounting surface:
- Flush-Mountable Sensors (Shielded):
- Designed to be installed flush with (or countersunk into) the surrounding metal mounting surface. Their sensing face is typically flat.
- Feature an internal shield (often ferrite) surrounding the coil. This shield focuses the electromagnetic field radially outwards from the front face and prevents it from extending laterally towards the mounting surface.
- Key Advantage: Immunity to metallic interference from the mounting structure itself. You can install them directly into metal brackets, panels, or machine frames without worrying about the metal causing false triggers or reducing sensitivity.
- Drawback: The focused field results in a shorter nominal sensing range (Sn) compared to an equivalent non-flush sensor.
- Non-Flush Mountable Sensors (Unshielded):
- Must be installed so that there is a clear space (free zone) around the sensor’s sensing face and cylindrical body. Mounting them flush against metal will severely disrupt their operation.
- Lack the internal shielding, allowing their electromagnetic field to extend radially from the front face and also laterally along the sides of the sensor body.
- Key Advantage: This extended, unshielded field configuration provides a longer nominal sensing range (Sn) versus a flush sensor of the same size and technology.
- Drawback: Highly susceptible to interference from nearby metallic objects, including the mounting surface. They require specific non-metallic brackets or standoffs to maintain the necessary free zone around the sensor body.
How the Magnetic Fields Behave: A Visual Comparison
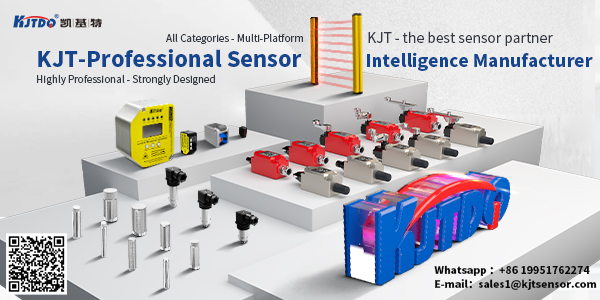
- Imagine a flush sensor’s field like a focused beam projecting straight out from its face, tapering slightly. The shield prevents the field from “leaking” sideways into the mount.
- Imagine a non-flush sensor’s field like a wider, more diffuse cone projecting from the face, with significant field lines also wrapping around the sides of the sensor housing. This wider field interacts more easily with targets approaching from a wider angle but also picks up nearby metal.
Choosing the Champion: Application is King
There’s no universal “best” sensor type; the optimal choice hinges entirely on the specific demands of the application:
When Flush Sensors Shine:
- Space-Constrained Mounting: When the sensor must be mounted directly into a metal surface or bracket due to limited space. The flush design is essential here.
- Metal Mounting Surfaces: Any application where the sensor body will be adjacent to or surrounded by metal (e.g., embedded in a machine tool, mounted on a metal frame).
- Precise Positioning/Detection: Applications requiring detection of small targets close to the sensor face, benefiting from the focused field.
- Reduced Risk of Side Impact: Flush mounting protects the sensor face from accidental damage from the side.
- Common Applications: Hydraulic cylinders (detecting piston position), metal stamping presses, robotic arms, machine tools, conveyor systems with metal frames, automated assembly lines with tight spaces.
When Non-Flush Sensors Excel:
- Longer Sensing Distances Needed: When you need the maximum possible detection range for a given sensor size.
- Non-Metallic Mounting Possible: When you can install the sensor using plastic brackets, standoffs, or in a non-metallic fixture, ensuring the required free zone.
- Detection Through Non-Metallic Barriers: The extended field can sometimes detect targets behind thin layers of non-metallic material (plastic, glass, wood) more effectively than flush sensors, though this depends on barrier thickness and material properties.
- Wider Lateral Approach: Can detect targets approaching more from the side due to the unshielded field wrapping around the body.
- Common Applications: Detecting pallets on conveyors (mounted overhead on plastic bracket), level detection in non-metallic bins, presence detection where longer range is critical (e.g., large machinery guarding), applications mounted on plastic structures.
Critical Selection Considerations Beyond Mounting
While mounting style is crucial, other factors interplay:
- Target Material: Inductive sensors detect metals, but sensitivity varies (steel highest, then stainless steel, then aluminum, then brass). Sensing range (Sn) is specified for mild steel. Flush sensors might suffer more range reduction on non-ferrous metals.
- Sensing Range (Sn): Compare the actual required distance against the rated Sn for both flush and non-flush options. Always derate the Sn for safety factors (e.g., use 70-80% of nominal range) and account for temperature, voltage, and target material effects.
- Operating Environment: Consider temperature extremes, chemicals, washdown requirements (IP rating), mechanical shock, and vibration. Both types are available in ruggedized versions.
- Sensor Size (Housing Diameter): Smaller sensors inherently have shorter ranges. A non-flush M8 sensor might offer comparable range to a flush M12 sensor.
Summary: Making the Informed Decision
Feature |
Flush Sensor (Shielded) |
Non-Flush Sensor (Unshielded) |
Mounting |
Flush into metal surface |
Requires free zone around body |
Magnetic Field |
Focused, radial only |
Extended, radial + lateral |
Key Strength |
Immune to metal mounting surface |
Longer nominal sensing range |
Key Limitation |
Shorter sensing range |
Susceptible to metal interference |
Ideal For |
Tight spaces, metal mounts |
Longer range, non-metallic mounts |
Selecting between a flush and non-flush sensor is a foundational decision in proximity sensing design. Flush sensors offer robustness and ease of installation in metal environments but sacrifice range. Non-flush sensors deliver superior range but demand careful handling regarding their surroundings. By intimately understanding the physical constraints, target characteristics, environmental demands, and the fundamental operational differences between these sensor types, engineers and technicians can implement solutions that maximize uptime, enhance process reliability, and deliver peak automation performance. The right choice ensures your sensors are not just installed, but optimally configured to keep your operations running smoothly.