capacitive and inductive proximity sensor
- time:2025-07-08 02:06:51
- Click:0
Capacitive and Inductive Proximity Sensors: Sensing the Unseen in Automation
Imagine machines reacting instantly to the presence of an object without ever touching it. This isn’t science fiction; it’s the everyday reality powered by proximity sensors. Among the most prevalent types are capacitive proximity sensors and inductive proximity sensors. These unsung heroes of automation operate silently and reliably, enabling countless processes in manufacturing, packaging, food production, and beyond. Understanding the distinct principles, strengths, and ideal applications of each unlocks the potential for smarter, safer, and more efficient system design.
At their core, both sensors offer non-contact detection, a crucial advantage where physical contact is undesirable – whether due to potential damage, contamination risks, or the sheer impracticality of touch-based methods. However, the physics governing their operation differs fundamentally.
Inductive Proximity Sensors: Masters of Metal Detection
Inductive proximity sensors are the go-to choice when the target object is metallic. Their operation relies on electromagnetic induction.
- Core Principle: The sensor’s active face houses an oscillator coil that generates a high-frequency oscillating electromagnetic field.
- Detection Trigger: When a conductive metal target enters this field, eddy currents are induced within the metal.
- Energy Drain: These eddy currents draw energy from the sensor’s oscillating circuit.
- Signal Change: This energy loss causes a measurable reduction in the amplitude of the oscillation.
- Output Switching: An internal circuit monitors this amplitude change. Once the amplitude drops below a preset threshold (indicating the target is close enough), the sensor’s output state switches (e.g., from OFF to ON, or vice-versa).
Key Advantages and Characteristics of Inductive Sensors:
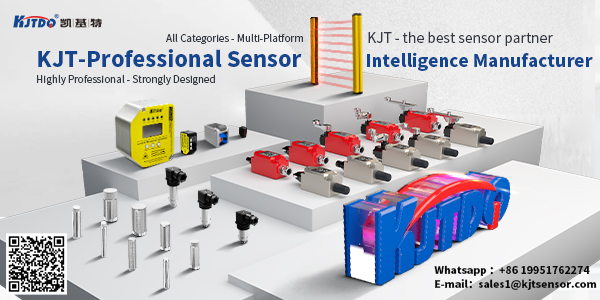
- Unrivaled for Metal: Exceptionally reliable and accurate for detecting ferrous (iron-based) and non-ferrous metals (aluminum, brass, copper), though detection range varies based on metal type.
- Robust Construction: Typically housed in rugged metal bodies (stainless steel or nickel-plated brass), making them highly resistant to physical impacts, vibration, and harsh industrial environments like machine shops or foundries.
- Unaffected by Non-Conductors: Water, oil, dust, wood, plastic – these materials generally do not trigger a standard inductive sensor, minimizing false positives. This makes them ideal for dirty or wet conditions.
- High Switching Frequencies: Capable of detecting very fast-moving targets, essential for high-speed counting or positioning applications.
- Long Operational Life: No moving parts and robust design contribute to exceptional longevity with minimal maintenance.
Primary Applications: Metal part detection on conveyors, position sensing of cylinders or actuators, presence verification of gears/bearings, high-speed counting of cans/metallic packages, end-of-travel limits in machinery, and level detection of metallic liquids.
Capacitive Proximity Sensors: Detecting Nearly Anything
While inductive sensors reign over metal detection, capacitive proximity sensors boast a much broader detection palette. They function based on capacitance – the ability of a system to store an electrical charge.
- Core Principle: The sensor face acts as one plate of a capacitor. The other “plate” can be a ground reference or the target object itself. An internal oscillator generates an electrostatic field extending from the sensor face.
- Detection Trigger: When any material (solid, liquid, granular, powder) enters this electrostatic field, it alters the capacitance of the system. The dielectric constant of the target material significantly influences how much the capacitance changes. Materials with high dielectric constants (like water, metal, wood, plastic, glass) cause a larger change.
- Oscillation Change: This change in capacitance affects the oscillator circuit. As the target approaches, the oscillation amplitude increases.
- Output Switching: An internal circuit detects this amplitude increase. Once it surpasses a defined threshold, the sensor’s output switches state.
Key Advantages and Characteristics of Capacitive Sensors:
- Material Agnosticism: The standout feature. Capable of detecting metals, plastics, glass, wood, cardboard, paper, liquids (water, oil, chemicals), powders, granules, and even biological materials. The detection distance depends on the target material’s dielectric constant.
- Level Sensing Prowess: Excellent for detecting the presence or level of liquids, pellets, powders, or granular materials through non-metallic container walls (plastic, glass). This makes them invaluable in food & beverage, pharmaceutical, and chemical processing.
- Solid-State Reliability: Like inductive sensors, they have no moving parts, ensuring long life.
- Sensitivity Adjustment: Most capacitive sensors feature a potentiometer to fine-tune sensitivity. This allows compensation for different container wall thicknesses or materials and helps ignore unwanted background objects.
Key Considerations:
- Environmental Influence: Moisture, dirt, or humidity buildup on the sensor face can affect readings or cause false triggering. Careful mounting and selection are crucial.
- Tuning Requirement: The sensitivity adjustment is essential for optimal performance but requires setup for the specific application.
Primary Applications: Liquid level detection in tanks (through walls), powder/pellet level monitoring in hoppers, non-metallic object detection (bottles, boxes, plastic parts), presence detection of materials on conveyor belts (regardless of material), and label detection.
Choosing the Right Sensor: Capacitive vs. Inductive Head-to-Head
Here’s a quick comparison to guide selection:
Characteristic |
Inductive Proximity Sensor |
Capacitive Proximity Sensor |
Detection Principle |
Electromagnetic Fields (Eddy Currents) |
Electrostatic Fields (Capacitance Change) |
Ideal Target Material |
Metals (Ferrous & Non-Ferrous) |
Virtually Any Material (Metals, Plastics, Liquids, Powders) |
Detection Through Walls |
Very Limited or None |
Effective Detection through thin non-metallic walls |
Sensing Range |
Shorter, highly material-dependent (metal type) |
Moderate, adjustable, material-dependent (dielectric) |
Environmental Resistance |
Highly Robust (oils, dust, vibration-resistant) |
Sensitive to surface contamination (moisture, dirt) |
Sensitivity Adjustment |
Limited or fixed |
Adjustable, essential for optimizing performance |
Top Application Focus |
Metal detection, high-speed counting, position sensing |
Level sensing, non-metallic object detection |
Key Selection Criteria Recap:
- Target Material: Inductive for metals. Capacitive for non-metals, liquids, powders, or detection through containers.
- Detection Distance: Consult sensor specifications, considering both nominal range and necessary reduction factors.
- Environment: Consider temperature, potential for chemicals, oils, dust, and washdown requirements. Inductive generally handles harsher physical environments, while capacitive must be protected from excessive buildup on the sensing face.
- Installation: Ensure sufficient space for mounting and the required sensing distance. Account for background interference (e.g., metal near an inductive sensor, other materials near a capacitive one).
- Output Type: Select Normally Open (NO), Normally Closed (NC), or analog outputs (for distance measurement) matching the control system input.
Optimizing Automation with the Right Non-Contact Detection
The choice between a capacitive and an inductive proximity sensor hinges fundamentally on what you need to detect and where. Inductive sensors are the rugged, high-speed specialists for metallic targets, indifferent to most non-conductive debris. Capacitive sensors are the versatile material detectors, excelling in level sensing and handling diverse non-metallic objects, albeit requiring more attention to their environment. By leveraging their complementary strengths – the robust metal detection of inductive sensors and the broad material versatility of capacitive sensors – engineers and technicians can implement highly reliable and efficient non-contact sensing solutions. This insight drives smarter automation across industries,